Seal upgrade and pump repair in the U.S. midwest boost efficiency and reliability with minimal downtime.
Hydro Inc., John Crane
11/21/2016
Mechanical seals on pumps in the oil and gas industry often need to be upgraded to meet more stringent standards, such as tighter emissions regulations. More advanced seals also offer companies increased efficiency and reliability. Older pumps, however, sometimes need to be modified to accommodate these enhancements because the newer parts may not be the same size and shape as the ones they are replacing. In these cases, a parts supplier can partner with an aftermarket engineering firm to come up with a long-term plan for revitalizing older pumps. The refurbished pumps can offer benefits including direct cost savings and a reduction in repair and maintenance.
An Upgrade Plan Emerges
In 2011, a field service engineer was at a pipeline station for service when a technician informed him that the company was considering overhauling all of its pumps as preventive maintenance. The company planned to investigate the possibility of upgrading mechanical seals. The field service engineer and his team decided to analyze all of the user’s pumping stations from Illinois to Iowa—about 500 miles of pipeline. Every field service engineer who worked on the pipeline met in Cedar Rapids, Iowa, where a regional engineer led a meeting about what would be the best technology solution for this user. The team decided to replace the existing single mechanical seals with a mechanical seal developed specifically for single-seal installations and designed to attain maximum achievable controllable technology (MACT) compliance in light hydrocarbons and other volatile organic compounds (VOCs).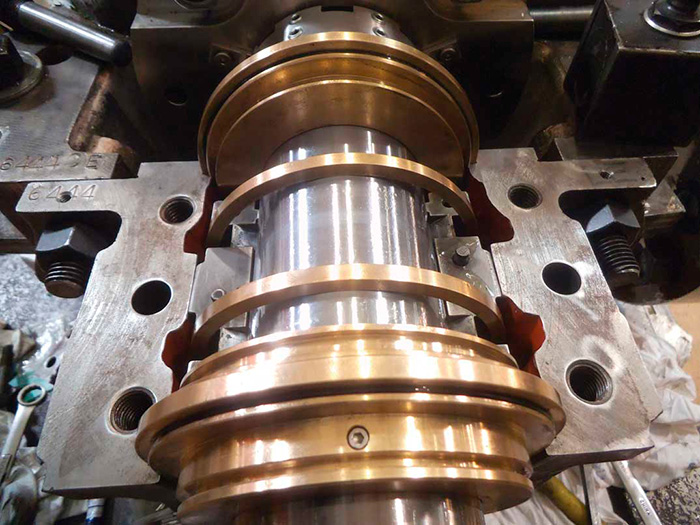
Suggested Seal Replacement
The first pump to undergo seal upgrade resides at a mainline pump booster station for a 10-inch propane/butane pipeline that connects the user’s assets with Midwest markets, including Chicago.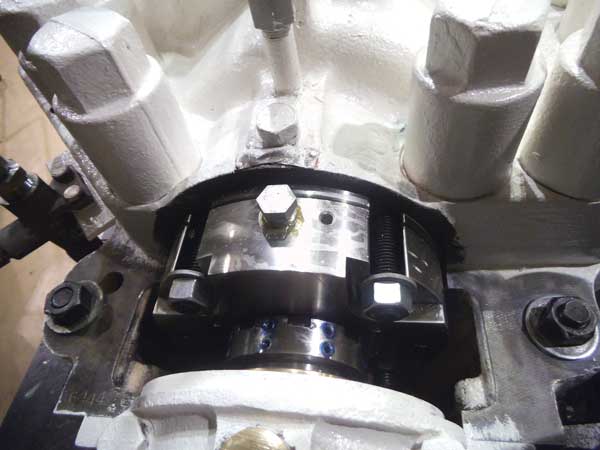
Modifying the First Pump
The new seal—a larger, double seal—would fit in the pipeline station pump with slight modification. While the pump was pulled to complete this adjustment, the end user also desired a high-quality pump inspection and repair to ensure the overall reliability of the complete pump. As an added benefit, the user could simultaneously have the service provider assess the condition of each pump and carry out any additional repairs resulting from wear and tear. The user’s reliability team worked with the seal company’s sales and engineering support group and the service provider’s management team to develop a comprehensive work scope. This required layout and specification of customized bearing isolator seals to fit the limited distance to the nearest obstruction. In addition, the case required drilling for seal flush and drain connections to ensure cooling and lubrication of critical seal-face areas. The repair and service provider also carried out a disassembly, cleaning and inspection (DCI) service, which identifies repairs, maintenance and upgrades that can be made to ensure optimal pump performance. The repairs included manufacturing of a new shaft modified with improved material and geometry to reduce stress and equipment fatigue, as well as replacement of the wearing components with tighter running clearances. These modifications were achieved by comprehensive inspection of parallelism, perpendicularity and concentricity of critical components as well as re-machining of the bearing housings.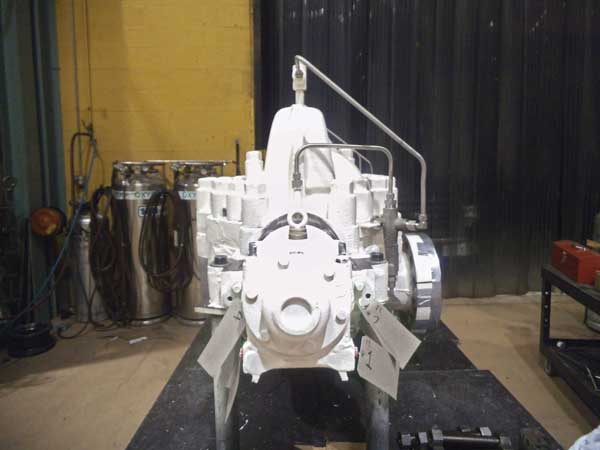