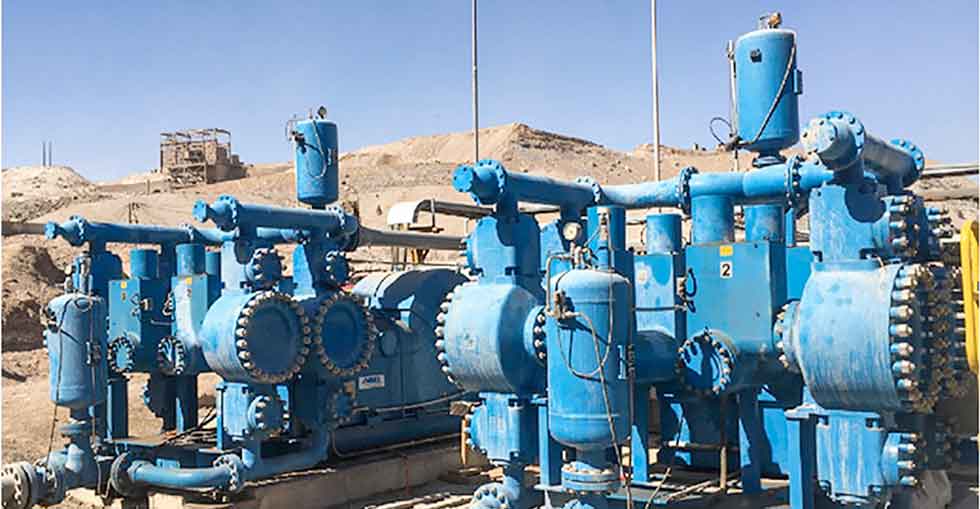
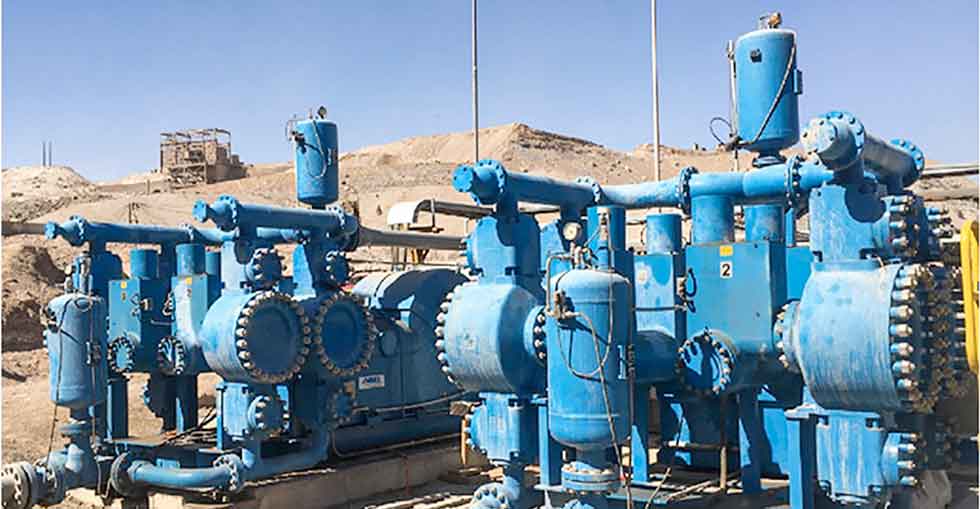
Maintenance is a word that sometimes takes on an “it can wait until it is scheduled” meaning. It is like a spare tire in a car—never appreciated until it is needed. But in mining, any slight interruption or even minor disruption to a harmonic production process can be the beginning of a potential costly death spiral to overall productivity. Dormant pumps mean valuable capital that was spent is not earning back its return on investment (ROI). Whether above or below ground, there is a need for a robust, long-lasting and a volumetrically efficient workhorse.
Constant pump adjustments, frequent parts changes due to poor duty life, fickle and high-maintenance problems are signs of a “pump in a box” approach to a severe duty application that seldom works in a hot, dry, long life cycle maintenance program or unforgiving environment. Pumps in this kind of service are usually forgotten unless there is a problem. Then they suddenly become center stage because many, if not all, processes come to a standstill.
The following are some advantages and disadvantages of a positive displacement piston-actuated diaphragm pump for both maintenance and operation:
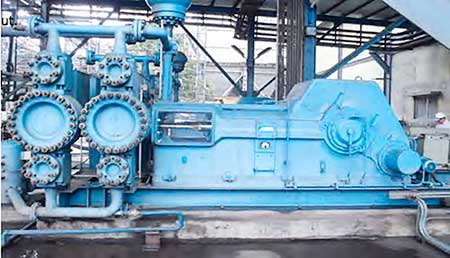
Benefits of Piston-Actuated Diaphragm Pumps
- The ability to have multiple diaphragms that split and share the hydraulic load.
- High volumetric pumping efficiency by nature.
- The ability to pump fluids and slurries with a high temperature.
- The ability to pump fluids and slurries with high solids content and suspended particulates.
- The ability to pump at relatively high pressures.
- The ability to work in either single- or double-acting design.
- Stroke adjustment for maximum efficiency, slow pump speed and low to no vibration.
- Low horsepower requirements.
- No seal problems because the diaphragm is the seal (technically hermetically sealed).
- Most have integral pressure relief systems.
- The diaphragm is positioned to the side of the product being pumped and, therefore, is passive pumping.
- Can last for many years with less overall maintenance.
- The option of ball check valves, cone valves or flapper valves depending on the application characteristics.
Cons of Piston-Actuated Diaphragm Pumps
- Higher initial cost.
- Sometimes take up more space than other pump types. (This may be important in a constricted environment.)
- Pump size needs to be increased if the pressure goes up.
- Higher average cost of spare parts.
- Longer production delivery times in some cases.
- Diaphragm pumps are not historically run in parallel or tandem.
- The piston-actuated diaphragm pump has earned its place in the pump pantheon over the last 40 years of service, but not as an off-the-shelf pump. It has become even less of a niche or custom pump these days as the requirements are ever-changing.
At its best, this kind of pump can earn back the capital investment in a short time due to the low maintenance, repair time, heavy-duty design and energy efficiency. The lack of packing, a mechanical seal, oilers or seal flush plans can make up for the initial higher cost. The diaphragm pump is efficient and often reliable—it can be a set it and forget it proposition.