This technology assists with preventing costly equipment failures while increasing production reliability and personnel safety.
Meg-Alert Inc.
04/11/2017
ExxonMobil’s Hebron platform off the coast of Newfoundland and Labrador, Canada, in the North Atlantic is a massive structure. At 230 meters tall, Hebron operates in 93 meters of water and is attached to the ocean floor using a stand-alone concrete gravity-based structure (see Figure 1). The structure contains more than 40 million cubic feet of concrete—more than what was used in New York’s Empire State Building. It is designed to store some 120 million barrels of crude oil and support 52 well slots.
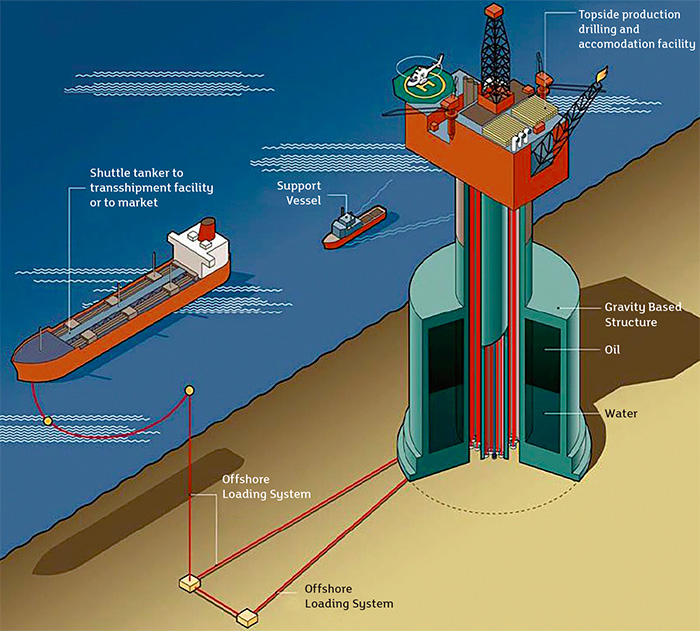
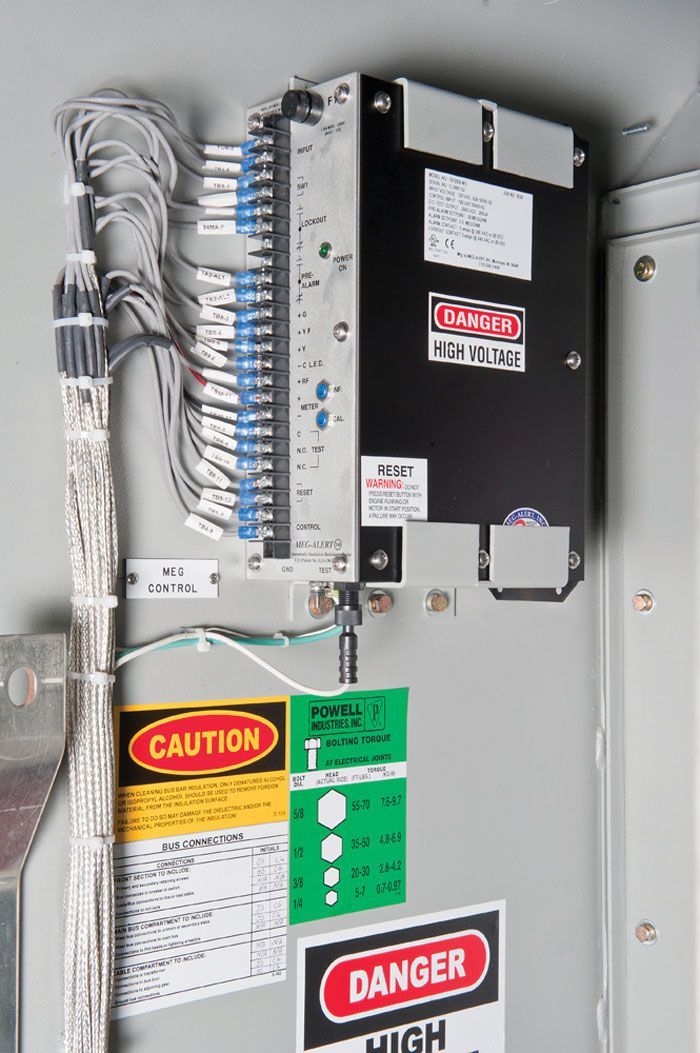
AIRT Installation
The AIRT system consists of a testing unit, a megohm meter display, a remote-control alarm assembly, a high-voltage (HV) test lead and an HV fuse assembly. The testing unit is located inside the high-voltage compartment of the MCC or switchgear and directly connects to the motor or generator windings (see Image 1). The testing unit is connected using an HV test lead with a built-in current-limiting resistor that limits the maximum testing current to a safe level for the equipment as well as the personnel. The current-limiting resistor is located at the end of the HV test lead where it terminates to the motor or generator leads. The HV fuse assembly is then installed into the HV test lead near the current-limiting resistor, between the resistor and the testing unit, to protect the system in the event of a fault. The megohm meter and the remote-control alarm assembly are located outside of the MCC or switchgear, normally on the LV door panel. The megohm meter indicates the real-time IR levels of the motor or generator windings and cables. The remote-control alarm assembly allows maintenance personnel to view the alarm indicators and operate the testing unit without accessing the inside of the MCC or switchgear cabinet. Some AIRT systems have a lock-out, tag-out power switch located on the remote-control alarm assembly in order to lock out the input power to the testing unit when hands-on maintenance work is being performed on the motors or generators (see Image 2).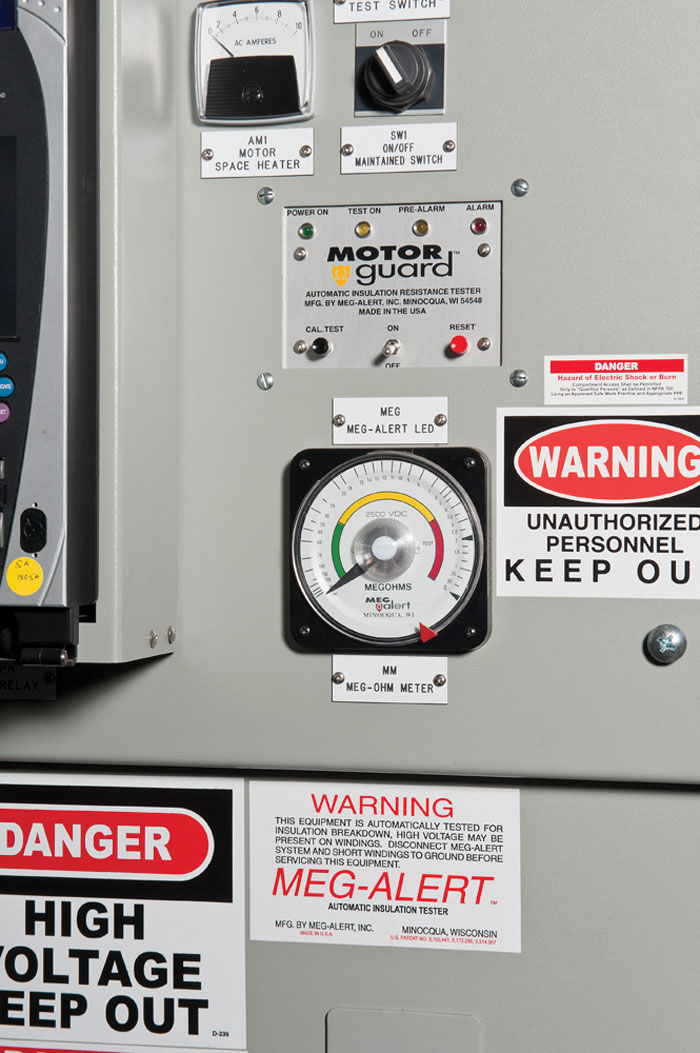
System Operation
Whenever a motor or generator is offline, a dry contact or voltage signal is sent from the contactor or switchgear control circuit to initiate the IR testing. The AIRT system will test and monitor the IR level continuously until the equipment is started again or the AIRT system is turned off. This allows the motors and generators to be tested before every startup, which is the most common time for an electrical failure to occur. Manual testing before every start-up is not practical. The AIRT system applies a non-destructive, current limited, DC test voltage to the phase windings and then safely measures any leakage current through the insulation back to ground. The leakage current is then converted to megohms of resistance on an analog meter display that indicates good, fair and poor insulation levels. When the predetermined IR set point levels are reached, indicator lights will turn on to signal an alarm condition. Most AIRT systems will have two adjustable alarm levels with dry Form C contact outputs. When the first alarm level is reached, a set of contacts can be used to send a pre-alarm warning, and when the second level is reached another set of contacts can be used to send a low-alarm warning to the motor or generator control circuit. The low-alarm contacts may also be used to disable the start circuit to prevent the motor or generator from being operated if the IR level is unsafe for operation.AIRT Benefits
The AIRT systems increased personnel safety on Hebron by eliminating the manual task of hands-on IR testing, commonly known as megging. The technicians no longer have to access the MCC or switchgear control cabinet and be exposed to dangerous arc flash and electrocution accidents. The AIRT systems also help prevent catastrophic equipment failures that can cause explosions and harm personnel. These systems help optimize equipment reliability and platform efficiency by detecting impending electrical insulation problems before unexpected downtime and forced outages result. Early-warning capability gives maintenance personnel the ability to take corrective action ahead of time and avoid a failure that would interrupt production. This ability helps maximize the reliability of the platform’s operations. By preventing catastrophic failures, the AIRT systems can help extend the useful operating life of the motors and generators.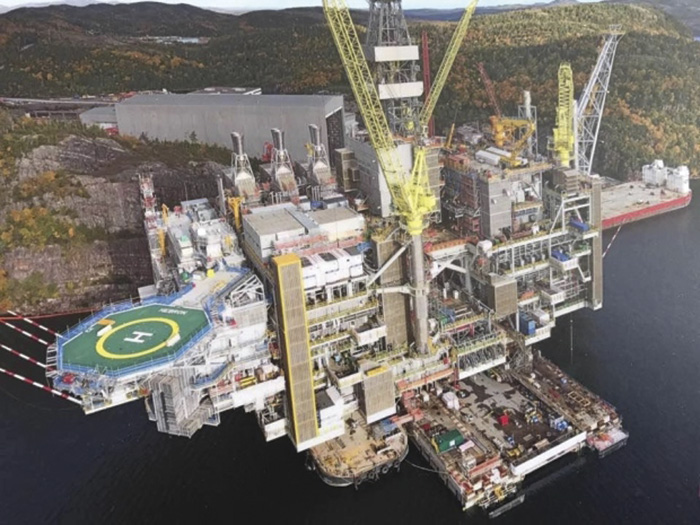