Two sets of seals, in service for 11 and 15 years, still meet baseline standards.
08/12/2015
Advanced thermoplastic materials offer several advantages over aluminum and other metals for turbo-compressor labyrinth seals. Polymer seals eliminate the risk of metal tooth deformation and mating shaft damage during shaft rubs. This enables end users to tighten initial clearances and reduce clearance loss over time. Overall compressor efficiency improves greatly over the life of the seals. This article provides mechanical property data from two different sets of seals. The integrity of the seals after 11 and 15 years in service was compared with new, off-the-shelf seals of the same material.
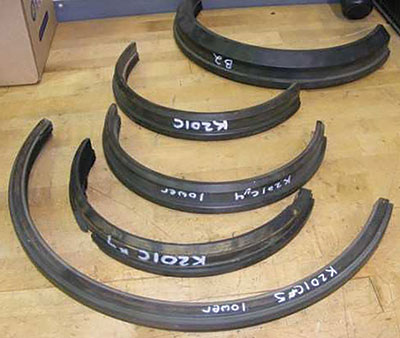
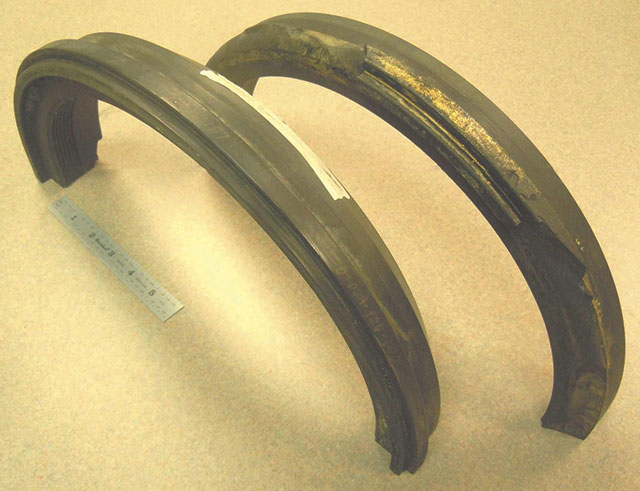
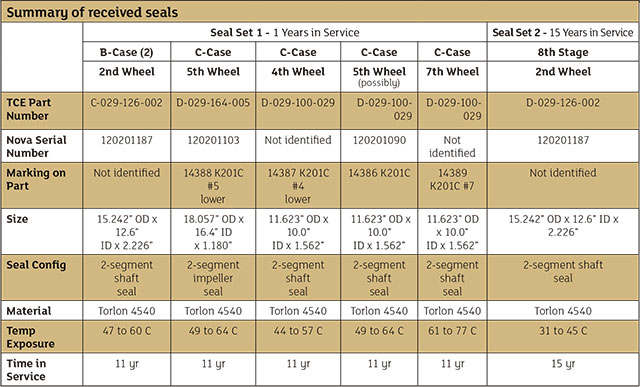
Evaluating the Seals
To evaluate the integrity of the seals, the mechanical properties of the returned seals were compared with those of standard seals. Only one seal—from the initial set, B-case, 2nd wheel—was large enough to allow full-sized tensile test bars to be machined. Tensile properties are the fingerprint of a material's integrity. Full-sized tensile bars are needed to yield a full complement of tensile properties, including strength, modulus and elongation values. In addition, other mechanical properties were evaluated, including compressive strength and modulus. For the initial set of seals, only compressive test samples could be machined and tested because of the limited sample size of the other, smaller cross-section seals.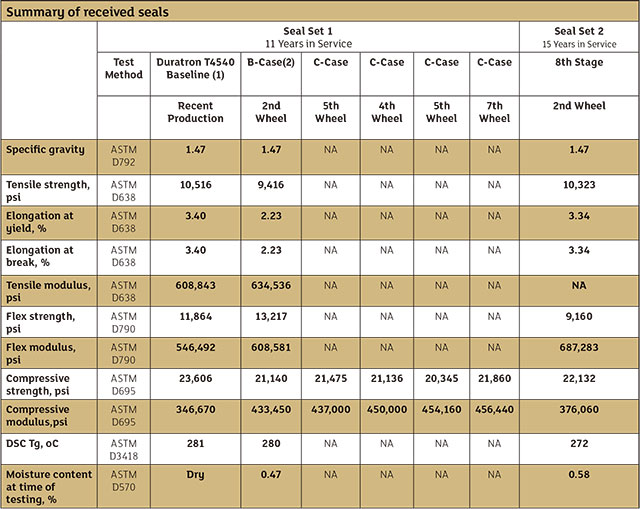
Results
The property values of both the 11-year-old and 15-year-old compressor seals revealed consistent performance compared with standard data for the product. For the 11-year-old seals, the tensile strength and elongation properties of the B-case sample were a little lower than baseline, but the tensile modulus was higher. The lower properties were due to slight embrittlement during service.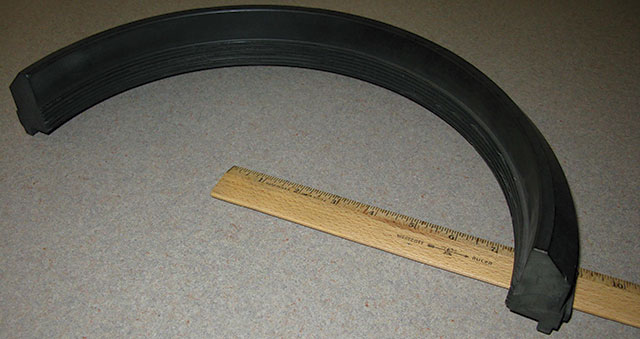