Although the traditional application is as a bearing surface, the technology is suitable for a seal face surface in pumps.
Flowserve
05/05/2017
A common theme in sealing pumps is to adapt existing mechanical seals to the application. An example is taking non-cartridge component seals and making them into cartridge seals, or taking single seal designs and placing them in series to create dual seals. This practice can result in a seal design that is not optimized for the intended service.
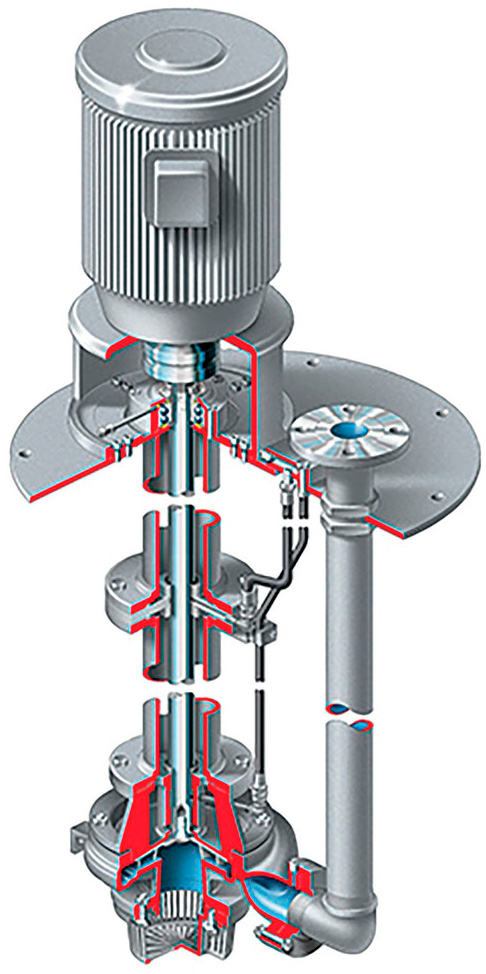
The Outlying Equipment
There are many pieces of equipment that require seals but are not well-covered by any sealing industry standard. As a result, their needs can be overlooked. Examples of plant specialty equipment include screw conveyers; blenders, mixers and agitators; rotary valves; and vertical sump pumps. This challenge affects vertical sump pump applications, which have a distinct seal chamber environment compared to its pumping peers. The vertical sump pump is found throughout industrial plants in open and closed sumps. Because these pumps feature side discharges to transport pumped fluid, the shaft column is effectively dry, with only some liquid lubrication for line shaft bearings. The seal chamber, which is near the mounting plate, creates the vapor-proof seal when the pump is installed in closed sumps. The vertical sump pump is described in the oil and gas standard for pumps, API 610, where it is given the designation of pump type VS4. It is notable that there is no API 682 qualification test that duplicates the dry sealing environment in these pumps, and API 682 provides no specific guidance to applying seals in VS4 pumps. This makes API 682 qualification status largely immaterial for demonstrating suitability for these pumps.Seals for VS4 Pumps
Pumps installed in open sumps have little need for a vapor-tight seal about the pump shaft, but closed sumps often contain dangerous vapors that cannot be permitted to vent into the atmosphere. The most basic sealing options include lip seals and packing, which may be optionally purged with nitrogen gas to reduce emissions.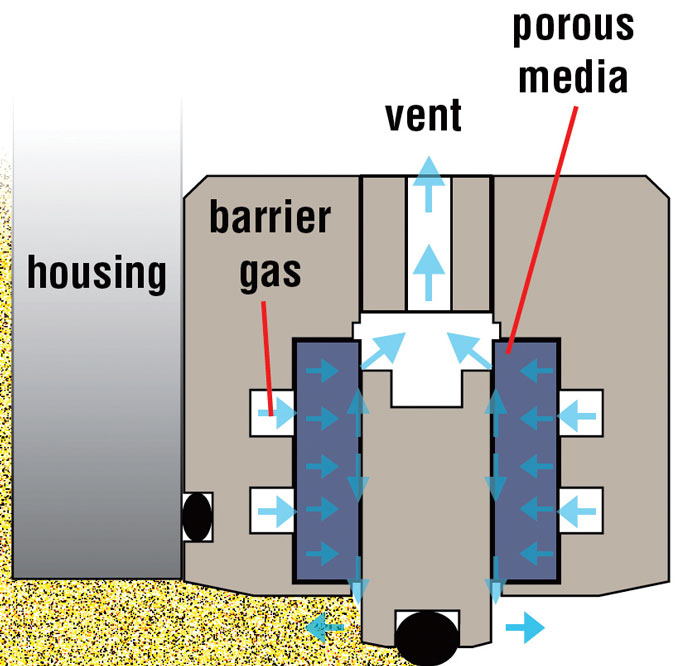
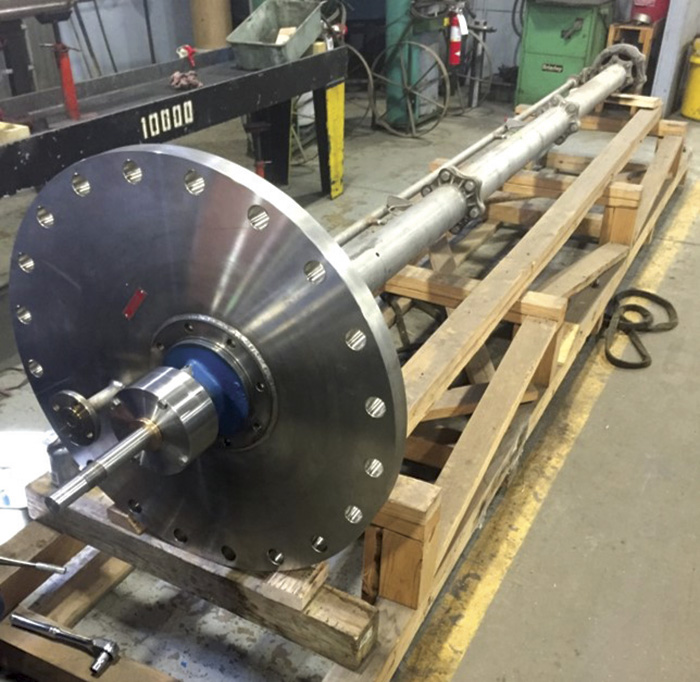
In the Field
Pumping acid in a chemical plant proved to be an ideal application for the porous media gas seal. The chemcial plant was using nitrogen-purged packing, but continued to experience downtime because of packing failures approximately every nine to 12 months.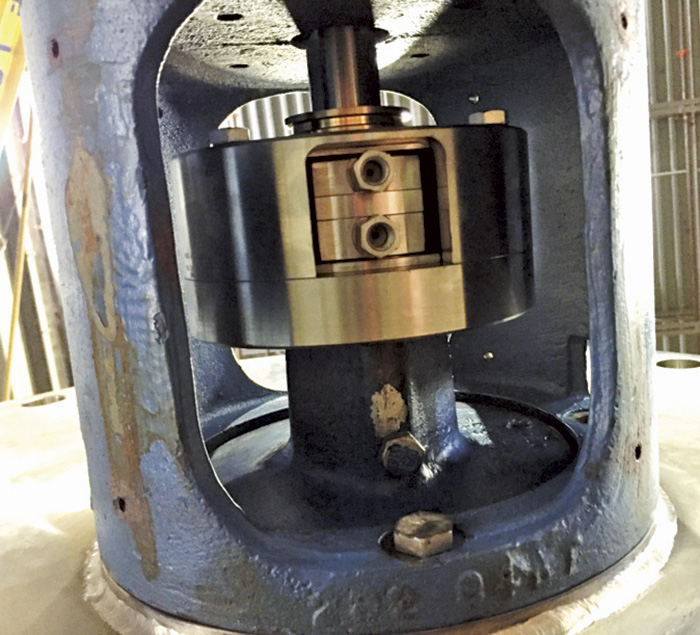
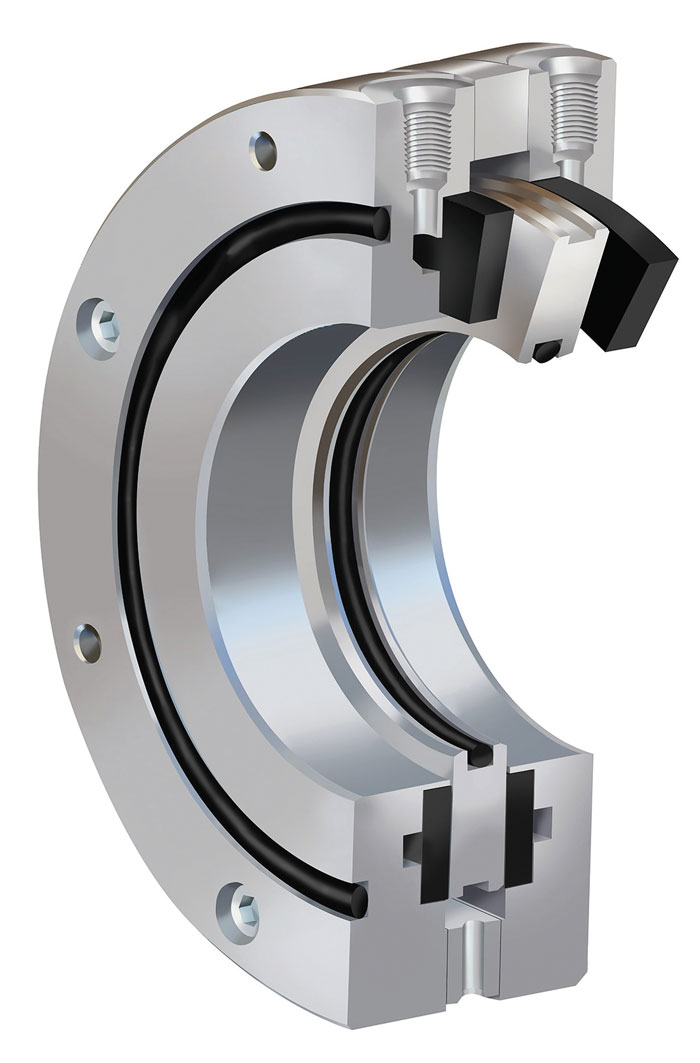