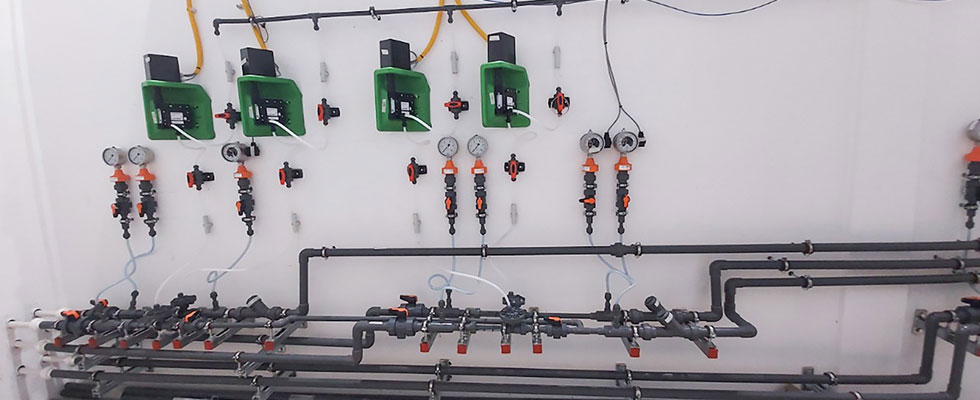
With today’s methods of treating drinking water being effective, users rarely think about what happens behind the scenes prior to turning on the tap. Much of the water that users consume or use on a daily basis has contained a collection of harmful microorganisms at one point in time. Prior to the introduction of water treatment and disinfection technology, there was a large risk of becoming ill from the available water sources, as they were often contaminated.
Early cases of diseases or sicknesses such as typhus, paratyphoid, cholera and diarrhea with vomiting, as well as viral infections such as hepatitis and poliomyelitis, can be directly linked to contaminated drinking water. Many public water circuits including municipal water supplies, lakes, pools, commercial building systems and cooling towers can also provide an environment susceptible to Legionella contamination. Exposure to this bacteria can cause respiratory illness and even lead to death, which is why proper water treatment techniques are so important.
Chlorine has been used to treat drinking water for more than 100 years due to its low cost and effectiveness against harmful disease. It is the most widespread disinfectant in the world and is used for a wide range of applications such as potable water treatment, wastewater treatment and pool water treatment. Chlorine can be introduced into these water systems in a variety of ways to help target the elimination of certain strains of harmful bacteria and viruses such as hepatitis, E. coli and Salmonella. The levels of added chlorine are just enough to kill off the bacteria while remaining safe for users to consume.
Manufacturers around the world offer a variety of chemical disinfection systems to ensure appropriate treatment for water applications. The method of treatment depends on a few variables like the application, size of the system, present bacteria and costs constraints. Options include chlorine gas, sodium hypochlorite and chlorine dioxide.
Chlorine gas dosing systems work in accordance with the full-vacuum principle that regulates the addition of gaseous chlorine reliably and precisely. These systems reduce the pressure of the chlorine gas to a vacuum, which successfully eliminates the risk of leakage. In the event of a pipe breakage, no chlorine gas can escape and only ambient air is drawn in.
Vacuum Regulator
The vacuum regulator is a pressure-reducing valve that reduces the overpressure from the chlorine tank side to the negative pressure on the vacuum side. The valve opens when a sufficient vacuum is present on the outlet side. Vacuum regulators with pressure gauge and liquid trap are available for more safety.
Dosing Regulator
The chlorine gas volume flow is adjusted with the dosing regulator. This can be done manually or automatically via motor control. Models can combine a vacuum regulator and a dosing unit in a compact enclosure.
Injectors
Injectors create the vacuum for the transport of the chlorine gas into the water flow. They operate according to the principle of a water jet pump. An integrated non-return valve protects the chlorine gas dosing system from the ingress of chlorine solution.
Changeover Devices
Changeover devices ensure a continuous supply of a chlorine gas dosing system by changing over from the empty bank of cylinders or drums to the standby bank.
Case Study
An OEM’s disinfection team in Mexico was involved in a major project to provide a chlorine gas dosing system in Nicaragua. The WTP Bluefields in Nicaragua is an important project to cover and secure potable water for more than 6,700 people in the city. The water treatment capacity in the plant is 260 liters per second (lp/s), and the disinfection process involves chlorine gas technology with prechlorination (4 kilograms per hour [kg/h] capacity) and post-chlorination (2 kg/h capacity). The complete chlorine gas treatment system was supplied by the OEM.
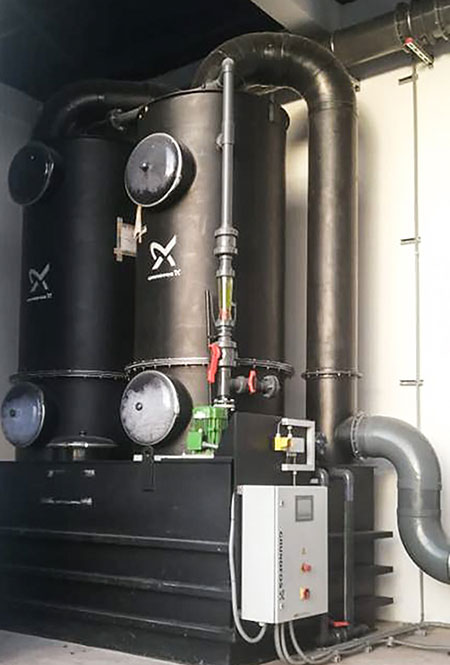
The main components provided were chlorine gas extraction, main and final chlorination including a dosing regulator, a vacuum regulator, an injector, a changeover device and water booster pumps. This was all controlled by a dedicated chlorine gas control panel. The system also includes a neutralization chamber containing sensors that detect gas leaks and alerts operators of any critical conditions.
The OEM partnered with personnel from the Bluefields Water Treatment Plant, along with local contractors to successfully install and commission the chlorine gas dosing systems.