Bundling technologies leads to enhanced system efficiency for a Connecticut water supply.
Xylem Inc.
01/23/2017
As corporate citizens, businesses must evaluate their impact on the environment and assess how their product applications affect the communities in which they operate and serve. To address aging infrastructure and conserve water, a growing number of operators are bundling existing pumps and vertical turbines with more advanced solutions to drastically cut energy costs while meeting their increasing water needs. Advanced solutions such as variable speed drives (VSDs) and intelligent pump controllers (IPCs) are two ways operators can vary pump speeds to reduce overall operating costs and extend product life. Proper selection of pumps, motors and controls is essential to ensure pumping systems operate efficiently and reliably.
Integrated Pressure Boosting
The goal of boosting water is to match the load profile precisely, reducing the energy required to run the system when water use is low. A booster system operates at 20 percent capacity or less nearly 80 percent of the time. As a result, many pumping systems benefit from variable flow to minimize power during reduced demand. VSDs are electric controllers that vary the speed of the current to the pump and change the operating speed, enabling pumps to respond smoothly and efficiently to fluctuations in demand. These robust, reliable and cost-effective solutions help users avoid the wear and tear of repeated on-off cycling. In a variable-speed application, as the flow decreases and the potential pump pressure increases, the drive slows the pump to match a constant discharge pressure. VSDs provide additional benefits otherwise unattainable in a fixed-speed application for operations with large flow variations and low static head. Static head, in its most simple form, is the difference in the supply’s height and the destination of the liquid being moved, or the pressure into which the pump is discharging. Some estimates suggest that VSDs can lead to a 50 percent reduction in hydraulic shock, often referred to as water hammer. Hydraulic shock is a brief increase in pressure inside a pipe caused by a sudden change in direction or velocity of water in the pipe. This phenomenon can lead to complete pipe failure. VSDs are often applied to existing systems to increase efficiencies. When a VSD is installed properly, pumps can work more efficiently, extending product life, reducing energy consumption, and decreasing mechanical and electrical system stress.Optimizing the System
A solution involving an IPC and VSD can be an economical answer for municipal and industrial water systems that have low water pressure. The extended hydraulics and advanced technology of one IPC can provide a distinct role in automating the regulation tasks of today’s superior systems because of its ability to withstand incoming power issues. These capabilities make it well-equipped to provide variable frequency control of speed, pressure, flow and level over a wide range of submersible and above-ground applications. VSDs and other optimized systems boost water for end users who need to maintain water pressures when demand is high or fluctuating. Greater flow and more friction lead to a reduction in the system’s water pressure. As water use increases, the IPC changes pump speed to keep line pressure constant. Systems built on hills or at the end of the water line are susceptible to fluctuating water supply and reduced pressure.Connecticut Case
In a rural Connecticut community, a VSD was faulting on a phase loss and experiencing random pump failure issues. This problem was similar to a drive running a pump and a motor when one of the legs of incoming power unexpectedly becomes lost or disconnected. Experts from the equipment manufacturer teamed up with distributors D&S Pump Supply Co. and Foley’s Pump Service to provide a reliable water source to the community.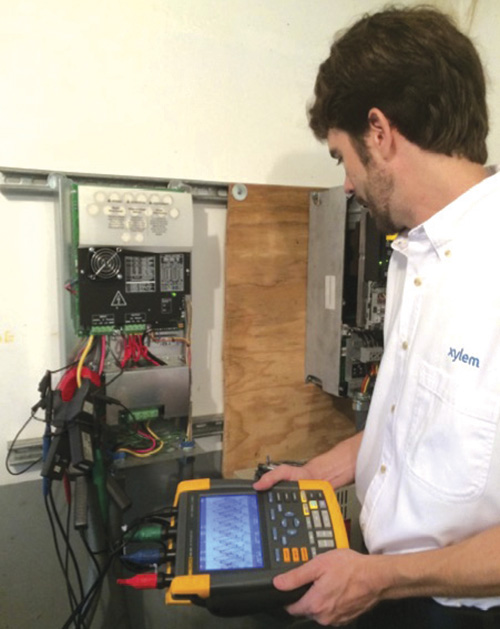
To read more Motors & Drives articles, go here.