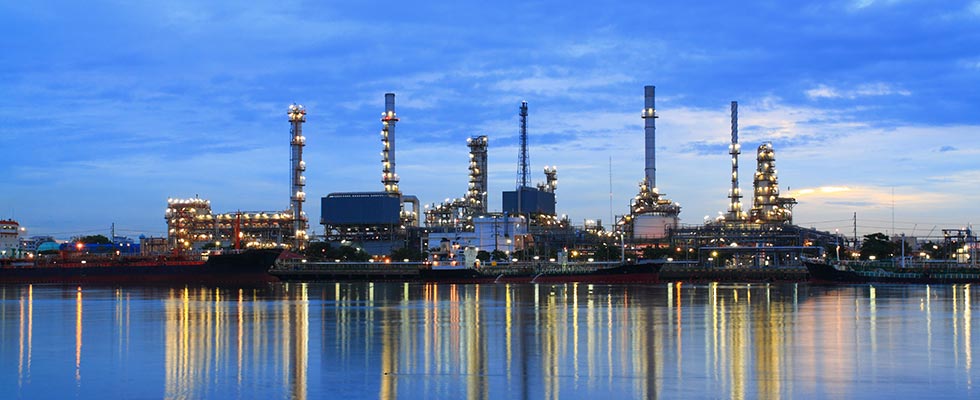
Each day, hundreds of thousands of industrial boilers heat water to generate steam for turbines and generators to make electricity. Plants running boilers range in scale from large utilities to smaller co-gen facilities that provide heat and power for universities, hospitals and industrial buildings.
Each plant requires a number of pumps to move water through various stages in the process. This article examines pumping requirements and also highlights two areas where pumps play an important role in reducing harmful emissions created during the power generation process.
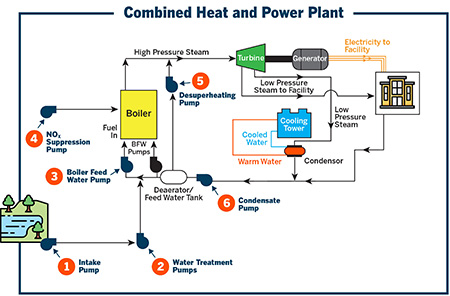
1 - Raw Water Intake Pumps
Before water is recycled in the loop depicted in Image 1, large volumes of raw water must enter the plant from a nearby lake, river or other body of water. Vertically suspended (VS) pumps are typically used for this application.
Selection criteria includes flows up to 39,600 gallons per minute (gpm) and head up to 490 feet. Reliability is also important, as submerged pumps are difficult to reach for maintenance.
2 - Water Treatment Pumps
Once water enters a plant, it must be cleaned to manage micro-bio organisms and to prevent scaling and corrosion. Clean condenser heat transfer surfaces have a direct impact on efficiency, and fouling can lead to expensive plant derates and unplanned outages. To clean water, chemicals like sulfuric acid (for pH control) and sodium hypochlorite (for disinfection) are used. These can be dosed via metering pumps, however, in higher flow applications, less complex and more reliable pumps such as sealless magnetic drive pumps are often used. The key requirements are high flow rates and relatively low pressures. Simplicity and reliability are important criteria, as many plants run operations around the clock so unplanned maintenance is to be avoided wherever possible.
Traditional demineralizer systems are also used to purify water for steam generating loops. Large ion exchange resin beds remove contaminants by substituting H+ ions and OH- ions for dissolved salts, resulting in water that is free of any dissolved salts. When exhausted, resins are regenerated by pumping sulfuric acid and sodium hydroxide, typically via sealless mag drive pumps. This regeneration process also requires large dosing rates at relatively low pressures.
3 - Boiler Feedwater Pumps
Boilers require continuous feedwater, which is delivered by feed pumps. Boiler feed applications require high pressures because of the high temperatures of the feedwater. Water changes to gas at 212 F, but boiler feedwater can range anywhere from 225 F (107 C) up to 350 F (177 C). In order to maintain feedwater in a liquid state, the pump (and the inlet piping) must maintain pressures that are higher than the water vapor pressure.
For most cogeneration plants, integrally geared pumps are suited to transfer feedwater into steam drums and back from condensers in closed loop cycles. Pumps must generate enough pressure to overcome the steam pressure in the boiler. Many boiler feedwater pumps should be able to deliver flows up to 230 gpm with heads up to 3,000 feet and a temperature range up to 650 F (340 C).
For larger plants with high flow and high head requirements, BB3 multistage pumps (up to 14 stages) are an option. Often, heavy duty pumps that can deliver heads to 4,260 feet with flows of 2,640 gpm are American Petroleum Institute (API) pumps, which are more expensive. Although a full range of API features and packaging is not always necessary for boiler feed pump applications, some operators consider the ruggedness and reliability of API pumps to be worth the incremental cost. Many horizontal axial split case pumps, running back-to-back impellers in heavy-duty double volute casings, are deployed at larger plants for boiler feed applications.
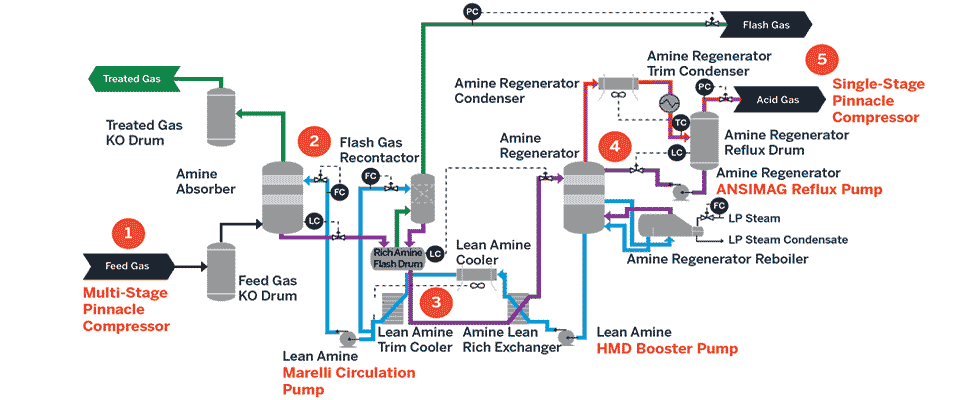
4 - NOx Suppression Pump
Nitrogen oxides (NOx) are a family of poisonous, highly reactive gases that form when fuel is burned at high temperatures in industrial boilers and turbines. NOx forms when heat forces nitrogen atoms to split and re-combine with oxygen atoms. This process increases exponentially at combustion temperatures. NOx is a strong oxidizing agent that reacts with volatile organic compounds (VOC) in the atmosphere to produce smog.
One of the best ways to reduce NOx is to keep it from forming in the first place. A simple (precombustion) method is achieved by reducing temperatures in boilers via water injection applications. Centrifugal high head, low flow pumps are often used to inject demineralized water (at high pressure) into boilers to lower flame temperature, reduce local oxygen concentration within the boiler, and decrease the formation of thermal and fuel-bound NOx.
Another type of post-combustion NOx reduction is selective noncatalytic reduction (SNCR). This reduces NOx from boilers by injecting ammonia or urea into the furnace or cyclone inlet where it mixes with the hot flue gas. Ammonia reacts with nitrogen oxides to produce water and nitrogen. The ammonia is typically injected using a centrifugal high head, low flow pump.
5 - Desuperheating Pumps
Steam performs mechanical work by turning turbines. Every power plant is different, and each plant has an optimal steam velocity for its process. Water can flow through piping at velocities of 15 to 25 feet per second (ft/sec), but steam line velocities can range as high as 400 ft/sec. Unintentional superheat lowers efficiency, and excessive steam pressure can harm pipes. To optimize steam temperature and pressure for a given plant, desuperheating and steam-conditioning systems are used. These skids feature monitors, valves and pumps, which are typically centrifugal high head, low flow pumps.
6 - Condensate Pumps
As indicated in Image 1, steam exiting the turbine is routed to cooling towers and condensers that turn the steam back into warm water. Often, impurities (such as carbonic acid) form during this stage of the process, which can reduce pH and potentially corrode pipes and pumps that are not made of stainless steel. Condensate pumps (made of stainless steel or other resistant alloys) are used to move water into a deaerator, which takes oxygen and carbon dioxide out of the feedwater before it is recycled to the boiler.
A Common Deaerator Issue & a Simple Fix
Plant operators and maintenance personnel in smaller co-gen facilities should ask two simple but important questions: How high is the roofline, and how much vertical distance is there between the deaerator and the boiler feed pump?
In most boiler rooms at smaller co-gen plants in universities, hospitals or industrial office buildings, the height of the roofline limits the vertical distance between the deaerator and the boiler feedwater pump. As a result, net positive suction head available (NPSHa) to pumps is limited, and suction transient conditions enable vapor to travel from the deaerator to the pump. This causes cavitation and can lead to fierce radial and axial thrust loads on a pump’s rotating assembly. Some pump types—such as segmented ring pumps—feature multistage designs with a dynamic hydraulic balancing disc. Under normal operating conditions, water flowing through the pump keeps everything in balance—but suction transient conditions can enable vapor to reach the bearings, which upsets the balance and causes the rotor to shift back and forth. Because the clearances are tight in ring pumps, even a slight shift can cause the impeller to hit the casing, which can lead to pump failures.
Larger utilities do not suffer from this because the physical distance between the deaerator and boiler feedwater pumps can be three to five times larger. For smaller cogeneration plants, pumps with thrust bearings included in their modular shaft assembly should be chosen because these pumps are designed to handle axial thrust without problematic balancing devices.
A Carbon Capture, Utilization & Storage (CCUS) Application
Water moves around a power plant in numerous ways to make steam that delivers the mechanical power needed to turn turbines and generators. But what happens at the end of the process? The remnants of the hydrocarbon heat source used to heat the boilers exit the plant in the form of flue gas, which is the combustion-exhaust that comes out of a smokestack. Flue emissions in many power plants (or refineries) are approximately 67% nitrogen (N2), 20% water (H2O) and 10% carbon dioxide (CO2). The remaining 2% to 3% is soot or particulate matter containing sulfur oxides. Removing CO2 from flue gas is a CCUS application that can be accomplished in many ways, one of which is via amine scrubbing. While advanced technologies are being developed to capture and remove CO2 emissions, amine scrubbing has a proven process for removing CO2 that is energy efficient and dates back to the 1930s.
How Does Amine Scrubbing Work?
Amines are aqueous chemical solvents (such as monoethanolamine [MEA] or diethanolamine [DEA]) that bond with hydrogen sulfide (H2S) and CO2 in a way that absorbs and removes them from gas streams. The scrubbing process works as follows:
Multistage gas compressors move gas into a vapor-liquid separator (called a KO or knockout drum), which removes water and liquid hydrocarbons from the gas stream.
The untreated “sour” gas enters an amine absorber, where API 610 circulation pumps inject aqueous amine solutions containing molecules that bind onto CO2 and H2S. A key requirement for pumps is the ability to handle high suction pressures. Safety and reliability are important because amines are corrosive and dangerous to plant personnel.
The “rich amine” (containing the CO2 and H2S) settles at the bottom of the absorber, where it goes to a multiphase separator. At this point, light hydrocarbons are flashed out of the amine. Heavy hydrocarbons are separated, and the rich amine is heated and fed to a regenerator column via sealless booster pumps. The pumps must be capable of supporting extremely high temperatures. Sealless pumps are a preferred choice. They provide leak-free performance and a small footprint, as there are no seal support systems taking up space on crowded amine skids.
Steam generated in the reboiler heats the amine and removes the H2S and CO2 from the amine. Regenerator reflux pumps move liquid hydrocarbons at, or close to, their bubble points (the phase at which gas bubbles emerge at a specific temperature). Sealless pumps, made of ethylene tetrafluoroethylene (ETFE) or metallic construction are the preferred choice for this application.
The lean amine from the regenerator is cooled in an exchanger, where it is returned to the absorber. The H2S is removed from the amine and cooled in a condenser. From there it could be sent to sulfur recovery units for processing into sulfur. Similarly, the removed CO2 can be processed into catalysts/polymers that are used to make plastics, adhesives, pharmaceuticals and many other products. Sealless pumps, made of ETFE or metallic construction (duplex stainless steel, alloy 20 and alloy C276) are the preferred choices because they are specifically designed for toxic, aggressive, hot or crystallizing processes.
Pumps move water around power plants in many ways. The hydrocarbon heat sources used to make steam contain impurities. Everyone understands the need to treat, absorb, capture and, wherever possible, eliminate these impurities. While new approaches and soon-to-be-developed technologies may one day deliver on the promise of lowering harmful emissions, existing technologies such as NOx suppression and amine scrubbing can be efficiently deployed today to eliminate 5% to 10% of the pollution that comes out of the smokestack of every power plant, refinery, chemical manufacturer and petrochemical plant.