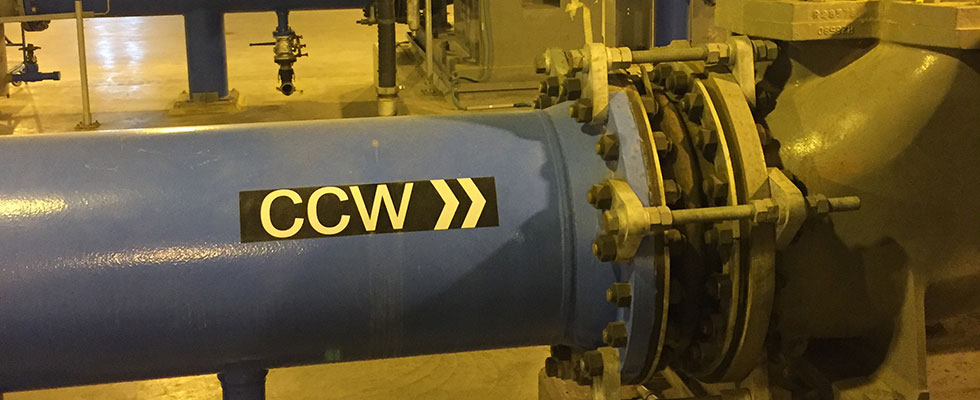
Elastomeric expansion joints are used in many diverse ways and systems within the power industry. Elastomeric expansion joints are flexible connectors comprised of natural or synthetic elastomers, fluoroplastics and fabrics and, when necessary, are reinforced with metal to provide stress relief in a piping system due to thermal expansion/contraction and mechanical vibration. Expansion joints play an important role when used in different power generating facilities from hydroelectric, nuclear, coal, thermal power to oil- or natural gas-fired combined-cycle or cogeneration power plants. Although these types of power generating facilities are different when it comes to expansion joints, they share some commonalities on which types of expansion joints are used and in which systems.
.jpg)
The most common type of expansion joint used in the power industry is the spool-type elastomeric expansion joint, which comes in a variety of design configurations—from single and multiple open and filled arch design to concentric and eccentric reducer designs (Image 1).
The spool-type expansion joints have an integrated full face rubber flange and are typically available in more design configurations as well as custom engineered solutions for unique installations/applications.
Power generating facilities are different based on their power generating techniques but share common processes and systems. Some of the common processes they can share are a boiler system, heat exchangers, condensers and cooling towers. The most common is a water circulation system.
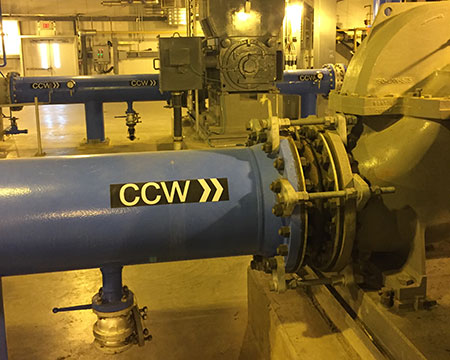
Depending on the power generating technique, these processes and systems can be applied differently but use expansion joints similarly. For instance, in a boiler system, heat exchanger, condenser or cooling towers, expansion joints can be found on both the supply and return lines, conveying fluid of varying temperatures based on the stage of the process.
The expansion joint is also typically used at the inlet and discharge of the pumps for the systems to dampen mechanical vibration, as well as further in the supply and return lines to account for thermal growth/contraction of the adjacent piping, reducing stress on the system.
Some common systems where expansion joints are found based on the power generating process:
Hydroelectric power generation
- pump storage stations: inlet and discharge of pumps
Nuclear power generation
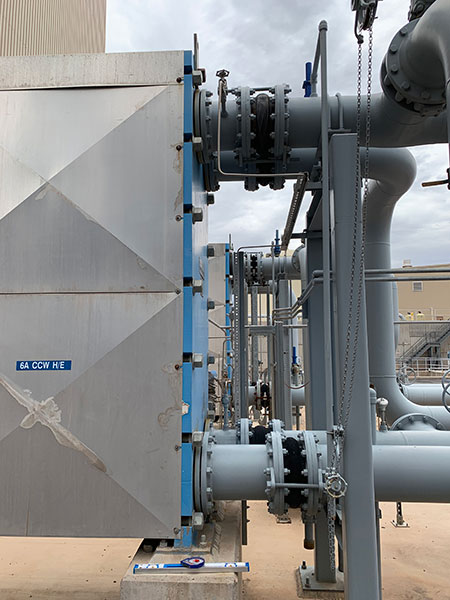
- cooling water circulation systems: supply and return lines, inlet and discharge of pumps
- heat exchanger systems: supply and return lines
Coal power generation
- raw water intake
- water circulation systems: supply and return lines, inlet and discharge of pumps
- condenser/condensate pumps: supply and return lines
- turbine to condenser connections
- heat exchanger systems: supply and return lines
- cooling towers: supply and return lines, building connections
- scrubber/absorber recirculating pump systems
- water redirect (CCR and ELG) systems
Thermal power generation
- water circulation systems: supply and return lines, inlet and discharge of pumps
- heat exchanger systems: supply and return lines
- condenser systems: supply and return lines
- cooling towers: supply and return lines

Combined-cycle or cogeneration power generation
- water circulation systems: supply and return lines, inlet and discharge of pumps
- condenser/condensate pumps: supply and return lines
- turbine to condenser connections
- heat exchanger systems: supply and return lines
- cooling towers: supply and return lines, building connections
Elastomeric expansion joints have a diverse and important role when used across the power industry and are applied in different systems in the power generating process. Although the processes may be different, the application of the expansion joints to compensate for mechanical vibration and thermal expansion/contraction are the same and found in many common systems shared among the power industry.