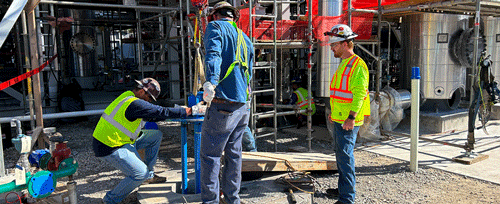
In the oil and gas industry, efficient and reliable pumping systems are crucial for the smooth operation of processing plants. The complex nature of oil and gas production requires pumps that can withstand extreme pressures, harsh environments and the demanding fluid characteristics often encountered in these pumping scenarios.
With the growth of energy demand and the shift toward more complex extraction and refining techniques, the need for advanced pumping solutions in oil and gas plants has never been more critical. However, having a single source that handles the project from start to finish in this process is also valuable to developers.
Oil and gas refineries are a maze of complex mechanical and electrical componentry and equipment that act as a single unit, working together to provide a finished product. In this type of application, package pump systems are a good option because they reduce the number of moving parts for a pumping system and provide a “plug and play” experience.
- Industrial refineries are a maze of complex mechanical parts.
- Industrial refineries are a maze of complex electrical parts.
- Typically, construction of these facilities relies on a single entity overseeing other manufacturers completing their smaller portions of the overall scope.
All these points emphasize the need for successful custom blocks of scope coming together to achieve a common goal. For the pumping systems required for an oil and gas plant, having a single source design, manufacture and supply the complete system is valuable to know for certain that this critical piece is covered.
- Package systems allow for a single entity to have control over the complete scope. This removes moving parts and helps to ensure success.
- Package systems are prefabricated in a controlled environment, allowing for a more “plug and play” experience.
- Package systems are customizable, fitting into the unique process equipment (both mechanical and electrical) configurations of a refinery.
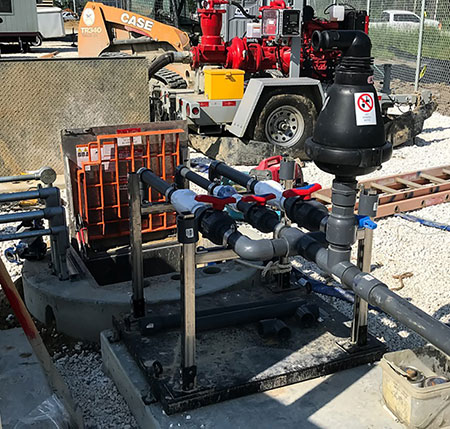
Electrical/Controls
Controls on a pump system, such as what are found in oil refineries, are of the utmost importance. The package system typically has its own custom functionality. In addition, the overall refinery must be considered its own package system. As such, the controls are all typically interlinked with systems such as a building management system (BMS). This allows someone to have true supervisory control and data acquisition (SCADA) and control the system remotely.
Being able to handle all the work to make sure the controls that come with the pump station meet the end user’s requirements for both operations and communication with the site’s overall SCADA or BMS is an important part of the single source.
This means when the lift station and its associated controls are installed and ready to start, it will meet the end owner’s expectations and easily integrate into the overall BMS. This allows for a quicker and cleaner system commissioning, which saves the contractor time and money.
A proper design-build, single-source will ensure all equipment is prepped, packaged, painted and tested in a controlled environment prior to delivery to the site. This reduces potential issues around troubleshooting and technician time on-site. After commissioning the system, if any issues arise, the user can contact the single source instead of contacting other entities or manufacturers on a system that already has many involved.
Equipment Requirements
Most pump systems at oil and gas facilities are installed in what are called classified areas. These areas are classified as a portion of the National Fire Protection Association (NFPA) code. There is more than one type of classified area, but typically they involve Class 1, Division 1 and Class 1, Division 2 areas. In both cases, explosive gases may be present, and this drives what equipment is allowed to be used.
Even if the pump station is not in a classified area, there are typically still a lot of restrictions on what type of equipment can be used. Most end users want all the valves, piping, etc. to match even if it is supplied as part of the package system.
Additionally, something that is not often considered is that for industrial projects, the force mains are not typically buried in the ground. They are in fact part of an overhead piping system that is called a pipe rack. The force main in the pipe rack is routed overhead through the site to the discharge point. This is a common way to handle piping in industrial sites, as it is easier to maintain piping that is overhead versus piping that is buried. The only real change is that the connection point is
above grade, along with the valves that are supplied.
An industrial stormwater and process water pump system at an oil and gas plant plays a critical role in managing water generated from both storm events and industrial processes. The system is designed to prevent environmental contamination, ensure regulatory compliance and maintain safe and efficient operations.
Natural Gas Plant
A cryogenic natural gas processing plant with a capacity of 150 million cubic feet per day needed an industrial stormwater and process water lift station.
The dual purposes of this pump station required shaft-driven centrifugal pumps with motors located above grade. The precast concrete sump was cast with a rectangular monolithic base to eliminate extra joints below the grade. The rectangular sump included a barrier wall, or weir wall, to separate grit and suspended particles from any stormwater runoff to protect the valves and pump impellers.
The package approach to pump stations was attractive to the developers because aspects of the pump station, such as the electrical controls, could be managed by its engineering staff.
This approach was attractive to civil engineers on the project because it would complete one aspect of the total construction project, allowing their staff to focus on the key systems of the operation of the natural gas processing plant.
The station was engineered with vertical sump pumps for industrial water applications. These pumps are intended to handle the suspended particles, like grit and hydrocarbons, that wash into the system during a stormwater event.
All the stormwater gets pumped into what is called a slop holding tank. The tank is emptied into trucks, which transport the water to an off-site treatment facility.
Being able to utilize a single-source company that can handle the entire scope of work to deliver a fully functional package pumping system that fits the exact needs of that plant and location cuts out other companies, providing a streamlined installation process where the system is prefabricated and fits into the unique process equipment configurations of a refinery.
Knowing the environment of these pumping systems and how to provide the correct equipment that will ensure the system lasts are important aspects where a single source can provide added value.