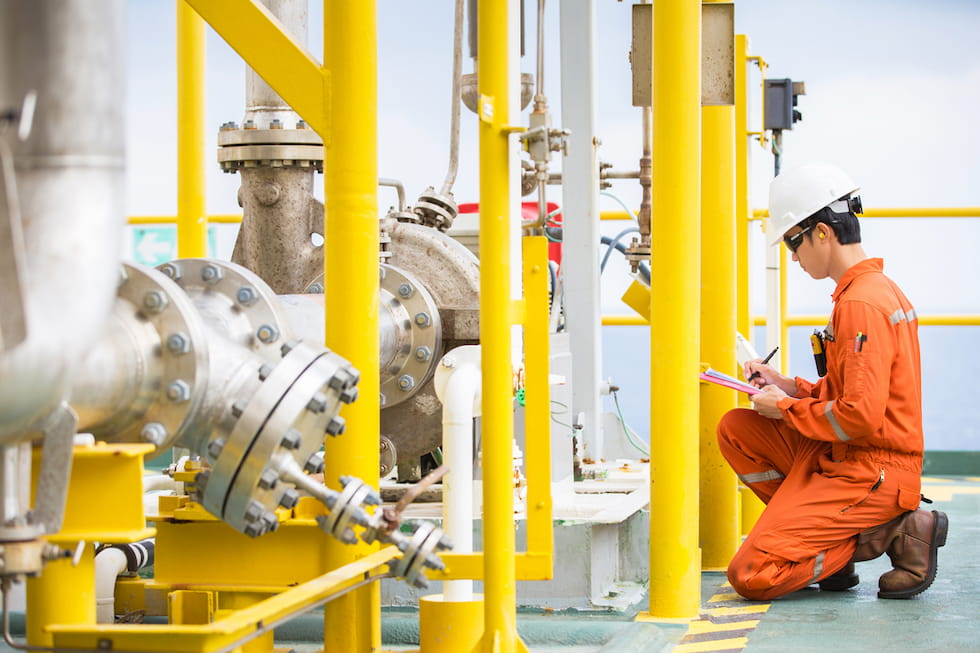
Unscheduled shutdown, failure, maintenance and part replacement are key factors for operation, efficiency and economy of any plant or facility. As rough indications, 20 to 40 percent of overall operating costs are due to maintenance actions. This can add up to a considerable amount of money. A key factor for improving maintenance policies, preventing failures and avoiding unnecessary part replacement is the ability to predict remaining life of machinery.
Prediction of remaining life is challenging and difficult, as any branch of science/engineering for prediction (such as weather forecasting) would be error-prone and subject to numerous changing variables. The estimation of remaining life is usually considered a theoretical topic that deals in extensive mathematical formulations and numerical simulations. This article discusses practical guidelines on prediction of remaining life of pumps and their key components.
Unscheduled Shutdowns & Scheduled Maintenance
Scheduled shutdowns are costly and should be delayed as far as safely and reliably possible. The time intervals between overhauls should be long. Unscheduled shutdowns can be expensive and troublesome and should be avoided. Prediction of remaining life is an important step to avoid unscheduled shutdowns and delay the scheduled maintenance or part/pump replacement.
This prediction can have a positive impact on the overall operation, reliability, safety and economy of the production. This can result in lower operational costs, higher availability and optimized operational time intervals between part replacement actions or major overhauls. Timely maintenance actions as the result of such predictions can contribute to avoiding catastrophic failure or unnecessary repair/part replacement.
Prognosis & Remaining Life
Prognostics is an engineering discipline focused on predicting the failure time or the time at which an equipment or system will no longer perform its intended function. Prognosis is the knowledge of future condition of equipment and machineries. It is usually performed through sensor-signal monitoring and, therefore, it is closely related to diagnosis and condition monitoring. The final outcome of prognosis is the knowledge of the remaining/operational life.
A good knowledge of modes of failure of the pump and key components is essential in developing remaining life estimates for them. Unless the degradation/wear mechanisms are understood, steps toward reliable condition monitoring and estimation of remaining life cannot be taken.
In many plants, condition-monitoring data from pumps (and other machineries) have unfortunately not translated into enhanced fault diagnosis, good detection/identification, prognosis, and remaining-life/operational data. There have been considerable volumes of condition-monitoring data (vibration, performance monitoring, oil analysis, etc.) in plants or facilities with no analyzing to find the rate of changes, diagnosis or prognosis.
Multiple/Independent Monitoring
Remaining life estimations usually depend on the accuracy of the monitoring sensors and fusion of monitored data. It is closely related to condition monitoring and data collection using multiple and independent sensors (monitoring methods) such as vibration monitoring, lubrication oil analysis, wear debris monitoring, acoustic emission (AE) monitoring and others. Using a single condition-monitoring method might be misleading for prediction. However, if multiple, independent monitoring methods indicate similar results and lead to similar predictions, such produced life predictions are reliable.
In other words, prognosis is linked with the use of multiple sensors, monitoring and combining/fusion of data. This should be conducted by experienced experts.
The automation aspect of it is related to digital signal processing and machine learning techniques.
Degradation, Wear & Damage
If there is a serious problem in a pump, its key components or its assembly/installation—such as if a wrong seal is selected or the seal is installed incorrectly—it will usually show up during startup or in the first weeks of operation. If a pump is operated successfully for the guarantee/warranty period (say, 12 or 18 months), then degradation, wear and damaging mechanisms will be the most likely reasons for possible future failures.
In many degradations, after an initial nonlinear phase, there are two phases of wear/damage developments:
A linear phase, with an almost constant rate.
A short, nonlinear terminal phase where the wear/damage rate increases exponentially. This is an explicit indication of an imminent failure.
Transitions & Rate of Change
There are usually subtle shifts (transitions) from “normal operation” to “defective operation” and, finally, failure. The rate of changes are important in this regard. Monitored or measured parameters can be categorized to slowly varying parameters and fast varying parameters.
There are usually more concerns on fast varying parameters. A key factor is how fast a parameter—such as vibration measured, leaked fluid through seals, an oil parameter, drop in head, or drop in flow rate—is changing from its baseline to its alarm set points (or other defined limits). It is important to assess how quickly a parameter changed from its normal value to the defined limits. This rate of change is usually more important than the normal/baseline or limit themselves.
Often in the case of concerning degradation or developing damaged (or in nonlinear terminal degradation/damaging), changes are relatively fast. On the other hand, in the case of normal and slow wear/degradation (or in linear low-speed wear/degradation), the speed of change is most often relatively slow.
Data-Driven Life Prediction Methods
Various data-driven methods have been proposed for predicting the remaining life of a degrading pump or degrading components of a pump (the time left before the failure). Data-driven methods are of interest when an explicit model of the degradation process is not known. They are based on observations of the degradation/wear process of one or more similar pumps (or similar components), and usually perform the regression of the future degradation path until predefined criteria of failure are met. This is based on predicting the remaining life of a degrading pump/component and providing a measure of confidence on the prediction, based on a set of reference trajectories experienced by similar pump/components that failed in the past.
Two key elements in the application of this group of methods are:
- How strong is the desired interpretation of similarity?
- What is the degree of trust given to the reference degradation trajectories?
Among data-driven methods, there are two main subcategories:
Degradation-based (wear-based) approaches, modeling the degradation/wear evolution. These are statistical models that learn the degradation evolution (wear, damage, etc.) from the time of the observed degradation/wear states. The predicted degradation/wear state is, then, compared with the failure criteria.
Direct life prediction approaches. These methods directly predict the remaining life. These are typically artificial intelligence techniques that map the relationship between the observable parameters and the remaining life, without the need of predicting the degradation/wear state evolution toward a failure threshold.
Degradation-based prognostics provide more informative and transparent outcomes than direct remaining life prediction prognostics since it supplies a prediction not only of the current remaining life, but also of the entire degradation trajectory. However, degradation-based prognostics require identification of a degradation indicator and a failure threshold, which may be difficult in practice, especially in cases where few or irregular degradation trajectories are available. This may introduce further uncertainty and sources of errors.
Challenges & Uncertainties
The remaining life estimates of pumps should consider intrinsic uncertainties due to the variability of the degradation, wear and damage processes caused by factors including unforeseen future loads, operational settings, external conditions and more. A major source of uncertainty is randomness in the future degradation/wear dynamics of the pump. This stems from changes in parameters, such as head, flow rate, load, temperature or the appearance of a sudden failure.
Another challenge is the scarcity of information typically available about remaining life of pumps and associated wear, degradation and failure. Actual failure histories are difficult to obtain. The exact replication of such events in a laboratory is insufficient by nature, costly, difficult and time-consuming. To bypass this, simulations are often proposed. The framework of such simulations should be based on real-life experiments. However, there are also many challenges, difficulties and inaccuracies associated with simulations.
There are many different wear, degradation and damaging mechanisms—such as fatigue, corrosion, erosion, creep, crack-developing, etc.—acting on each part or component and some of them interact with each other. Many degradation and wear processes are nonlinear, and they depend on various factors, parameters and conditions.
There are many parts and items in each pump that interact with each other, too. The complexity of the pump itself and the conditions in the operating environment make it hard to establish a set of reliable processes for remaining life estimations. All of these complicate the matter.
Comparisons of identical pumps may be proposed. However, there are still challenges. Considering the history of operation, so-called identical pumps do not experience the same degradation and wear path up to the present time and will not keep following exactly the same path in the future. In general, there are uncertainties in current, past and future degradation/wear.
Considering all the above-mentioned challenges, difficulties, ambiguities and errors, uncertainty management becomes a fundamental task in the prediction of remaining life.