Somewhere in North America today, a pump that is responsible for delivering residential drinking water through a municipal pipeline will stop working. Whatever the cause, the result will be largely the same: water supplies will be diverted, lives will be disrupted, and emergency repair funds will be spent. The good news is that events like these may not be typical for much longer. Thanks to a precipitous drop in monitoring technology costs and powerful new predictive analytics, it is now far easier—and less expensive—than ever to avoid pipeline, pumping and other system failures. And municipal water systems are the tip of the iceberg of beneficiaries. New stand-alone predictive maintenance solutions like these can be integrated into new and existing applications across a wide range of industries.
What a Difference a Sensor Makes
Monitoring of pumping systems and pipelines is not new. Water pressure has long been monitored by the nation’s water utilities. Regulations require midstream oil and gas pipeline companies to invest in leak detection systems. But traditional electronic monitoring processes like these are not particularly effective at signaling operators when system failure might be imminent. That takes data on other warning signs, such as equipment vibration and temperature. To obtain that kind of data, operators traditionally have been required to contract third-party specialists who survey conditions along a specific route. The data they collect can later be compared to previous reports to identify signs of deterioration. But because the data is collected only intermittently, it can be difficult, if not impossible, to pinpoint when or how a specific problem is triggered. Today’s advanced remote monitoring systems can deliver all that, and more. By adding sensors to motors, pumps and other equipment, it is now possible to collect continuous, real-time data that suggests a pump is approaching an unexpected shutdown or experiencing conditions that might negatively impact process performance. Depending on the application, that data can include everything from current and voltage information, to flow and pressure monitoring. This is just the kind of information a maintenance service company or in-house staff can use to prevent unexpected and costly equipment failure, improve performance and lengthen equipment service life.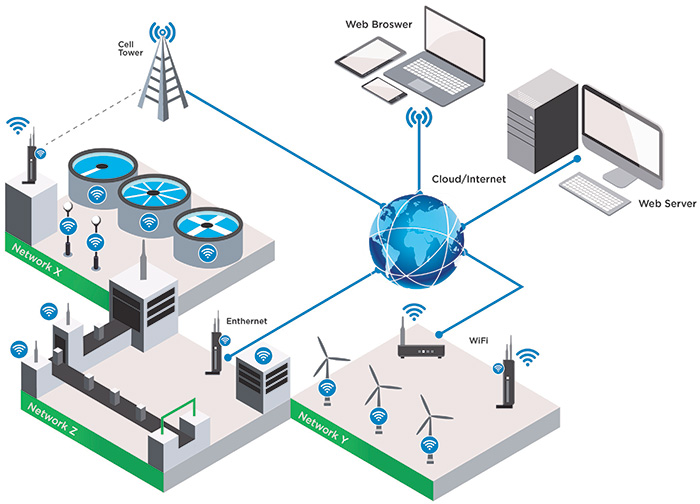