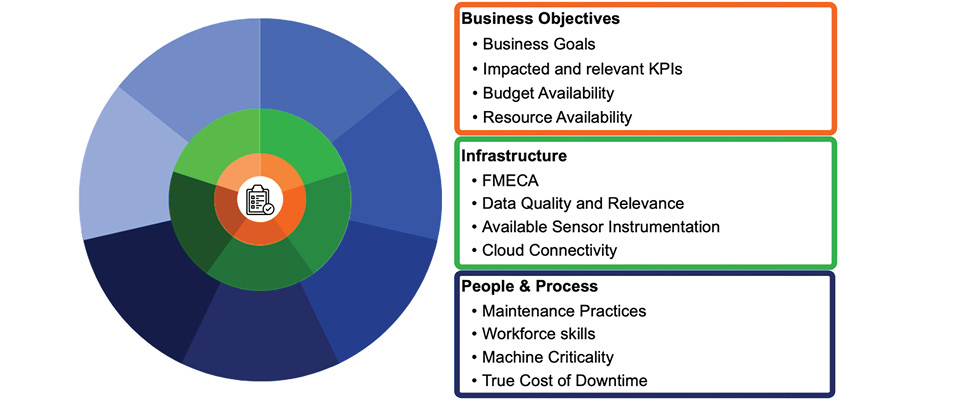
Imagine this: A user’s factory machinery, like a psychic, anticipates problems before they even occur. Welcome to the world of predictive maintenance (PdM). This is not merely a technological upgrade; it is an integrated approach involving people, processes and technology.
Despite its potential, not every plant is ready for this transition, and the path to success contains traps resulting from inadequate preparation or misconceptions about PdM requirements or capabilities.
Why Predictive Maintenance?
PdM is like having a crystal ball for factory equipment. It uses data analytics, machine learning and internet of things (IoT) technologies to predict and prevent equipment failures. This foresight is not just a matter of operational efficiency; it is a financial gamechanger, potentially saving millions annually for a modest-sized factory. It is no surprise then that PdM is rapidly becoming a staple in modern industrial operations, with 87% of operators considering making this shift and 60% already making moves to start rolling it out, according to a 2023 report by market intelligence firm IoT Analytics.
Game Plan
The benefits of PdM are significant, but realizing them requires a well-thought-out plan. Proper preparation ensures
alignment with business goals, a clear understanding of the technological requirements and readiness of the workforce. Conversely, rushing into PdM without this groundwork can lead to misallocated resources, technology that does not fit user needs and a workforce ill-prepared to leverage the new system.
The key lies in users understanding their factory’s specific needs, understanding what is possible with today’s PdM technology, evaluating gaps in existing infrastructure and aligning the PdM strategy with their business objectives. This initial effort pays dividends in smoother implementation, appropriately sets expectations for all stakeholders, allows for better integration with existing processes and maximizes return on investment.
The Anatomy of an Assessment
The first step in the plan is assessing plant readiness. What assets and capabilities are already in place that can enable PdM, and where does investment need to be placed? Let’s break down what is needed in an analysis:
Business goals and objectives: Users should start by aligning PdM with their business objectives. What do they want to achieve? Improved safety, reduced downtime, cost savings? All the above? These should align with corporate-level goals to increase the likelihood of executive sponsorship and budget availability. Keep these goals in focus.
Machine criticality: Not all machines are created equal. Identify which are vital for operations and which are the bad actors.
Failure mode, effect and criticality analyses (FMECA): If possible, users should undertake FMECA for each critical machine. This evaluation is beneficial for understanding which failure modes matter.
Data quality and relevance: PdM runs on data. Make sure there is access to high-quality, relevant data from the machines and the sensing infrastructure allows for the detection of the fault modes that matter. This includes not only having data of the right modality (e.g., vibration, temperature, pressure, etc.) but also the right range and frequency.
Technology infrastructure: Assess the factory’s tech setup. This includes connectivity, data storage, processing capabilities, sensor instrumentation and cybersecurity. For early detection of certain failures sensors, high-frequency sensors may be required.
Maintenance practices: Look at current maintenance strategies. Where can PdM fit in or replace them?
Workforce skills: A team needs the right skills to manage PdM systems. Training might be required and will always be helpful.
The true cost of downtime: Understand how downtime affects the bottom line. Consider both direct and indirect costs.
Budget and resources: Finally, does the user have the budget and resources for PdM? Do they have an executive sponsor that can allocate budget and resources to ensure success?
How to Get Started
If a user has made their assessment and understood their readiness, they may be ready to take the plunge. Here are a few concrete steps to begin the PdM journey:
Assemble a cross-functional team: This team should comprise of individuals from various departments, including maintenance, operations, IT and management.
Clearly define success metrics: Establish clear objectives and metrics to measure the success of the initiative.
Implement a pilot project: Start with a significant but manageable project. Avoid the trap of pilots with too small of a scale, as these may not provide comprehensive enough insights. Users will want to select machines where
they would expect at least a couple of dozen faults to develop during the pilot period. This can either be accomplished through a larger number of similar machines or a smaller number of machines that fail frequently.
Continuous improvement: Remember, readiness for PdM is not a one-time thing. Keep evolving with changing technology and business needs. A good idea is to review the readiness assessment yearly to ensure the conclusions still hold and the right set of machines continue to get the right monitoring performance.
Shifting to predictive maintenance is a strategic shift that can impact business outcomes. By thoroughly assessing a factory’s readiness and taking a structured approach to implementation, users will be setting the stage for a smarter, safer, more efficient and more cost-effective operation. The journey might seem daunting, but with the right preparation, PdM can be a game-changer for businesses.