With large numbers of people retiring in the coming years, the industry is emphasizing training opportunities more than ever.
Pumps & Systems
01/19/2017
When Zoeller Company started planning the development of its Center for Excellence training facility at its Louisville, Kentucky, headquarters a few years ago, educating its employees and others throughout the pump-related industry was the goal. But there was another important reason driving the need to increase training opportunities.
“We recognize that about 20 percent of our workforce (at the Louisville offices) would be able to retire in the next 10 years,” Zoeller Company Corporate Human Resources Director Dwight Newton said in a recent interview. Corporate-wide, Newton put the figure at about 15 percent. “That represents our most seasoned and knowledgeable staff, experience from all realms of both hands on the line all the way through senior management. It covers the gamut.” He added, “It’s exciting, but it puts us in a position to have to think about, ‘How do we transfer the knowledge?’ And that is what the Center for Excellence was built for.”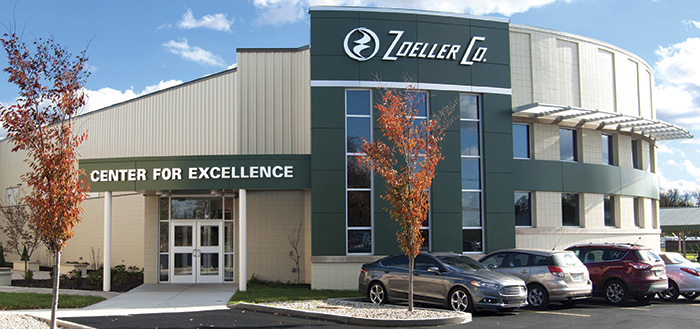
Center for Excellence
Industry organizations such as the Hydraulic Institute and the Submersible Wastewater Pump Association are offering a host of educational opportunities for clients, while many pump-related companies are focusing on training as they prepare for the future. Zoeller and its Center for Excellence, a 12,000-square-foot facility that opened in September 2015, are a prime example of a company focused on education. “This is not a new process—this is something we have been doing as long as we have been in business,” John Enyard, director of the Center for Excellence, said about providing education. “But we have seen it’s something that needed to be elevated to a different level. What we looked at is doing training, taking people into the shop, showing them what’s going on. … This has all been going on for a number of years. About three years ago, we decided we had to do it better at a more permanent location.” Zoeller started construction in early 2015 on the Center for Excellence and completed the facility in September 2015. The company’s entire workforce has been through classes at the training site, and about 600 other people have received training at the facility. “It’s something that we have to do,” Enyard said. “This is some of the stuff in the last two weeks that we have done: We have our customer support people, our product support people, come into a training, and they would take a pump apart … to install a new switch in it, so when they talk to customers on the phone, it’s not that they’re just reading it out of a manual. They have physically done it themselves,” Enyard said. “There’s nothing better than that to train somebody.” During the same time frame, Zoeller provided safety training for the company’s shop personnel, while a group from Alaska traveled to the facility to learn.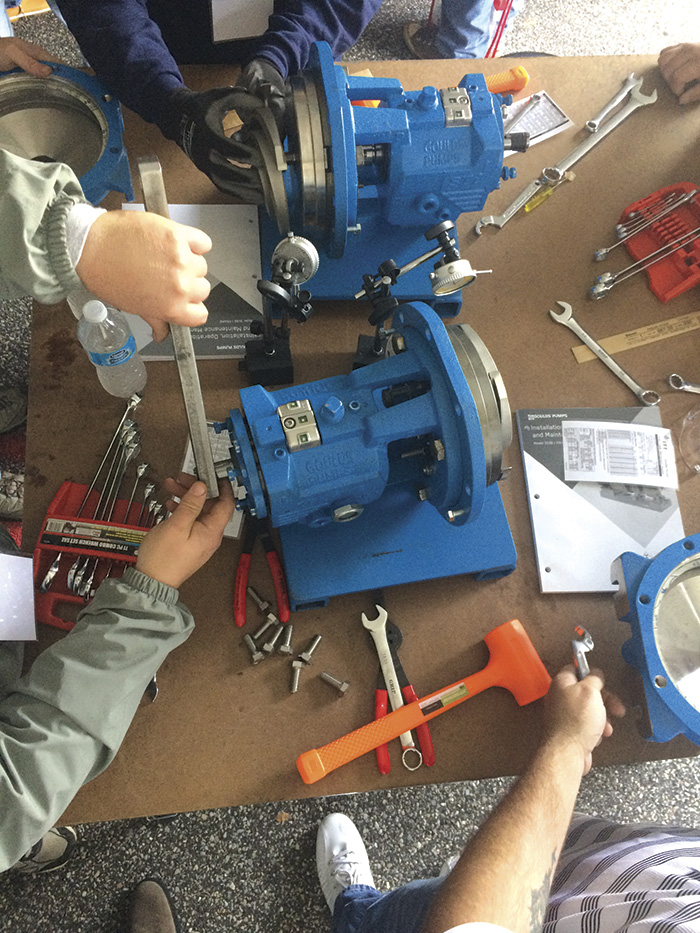
Demand for Training
At Grundfos, Steve Schmitz, the company’s director of technical education for the Americas, has seen a booming demand for training offered by the Grundfos Technical Institute, which provides a range of courses from the beginning through the advanced level. “Absolutely, it’s been growing since we started it” in 2015, Schmitz said in an interview. “I don’t see anything changing that’s going to lessen it. With rules and regulations in industry becoming more paramount and restrictive, people who are putting buildings up and designing systems that are going into them have their hands full,” he said. “We view our job here as a way to help them along in that process.” The Grundfos Technical Institute addresses the growing need to provide qualified, educated workers throughout the industry, Schmitz said. “It does touch on whether you have a lot of retirements in your system or not. It does touch on if you have the most qualified people in your positions that you’re filling,” he said. “People who are more knowledgeable about the products and applications they can go into can first of all realize the issues the customers have and give the most correct answer to the problem,” Schmitz said. “It’s always been very important for Grundfos that we have people who are properly trained in the marketplace.” The Grundfos Technical Institute serves workers in North and South America by providing virtual classroom courses and webinars that are “100 percent free,” Schmitz said. “The only thing we charge for is face-to-face courses,” he said, but “in the last couple of years, we have … really moved away from the traditional model that’s out on the marketplace, the face-to-face training.” The virtual courses allow anyone with an internet-connected tablet or computer to learn about a myriad of subjects at their own pace. Courses are available in Spanish and English. Visitors to the website grundfos.us/training can register for courses in categories including agriculture and irrigation; commercial and residential plumbing; heating, ventilation and air conditioning; fire pumps; municipal water systems; water treatment and dosing systems; and more. “If you look at the courses some of these students are taking coming out of the engineering schools, there’s not as much focus as you would see on basic foundational blocks,” Schmitz said. “Our approach is very much an application-based approach, what is the best-practice way to accomplish what is trying to be done.” Considering the courses are free and students can take them at home or from an office, the demand at the Grundfos Technical Institute continues to increase. “It’s expensive to travel and even more so having people out of the office for several days,” said Schmitz, noting that thousands of people have taken courses since 2015. “Grundfos employees, depending on their job positions in the company, are required to do a certain number of courses every year. … Outside of the company—overwhelmingly where we see the usage—it comes from all spectrums across the board as far as titles and positions.”Hands-On Learning
One day last October, beneath one of the four big-top tents temporarily set up at Geiger Pump & Equipment Company’s facility in Aston, Philadelphia, the company’s Todd Jenner led a class on centrifugal pump assembly and repair. The bustling activity at the facility signaled the arrival of Geiger’s Mid-Atlantic Pump & Process Equipment Symposium XI.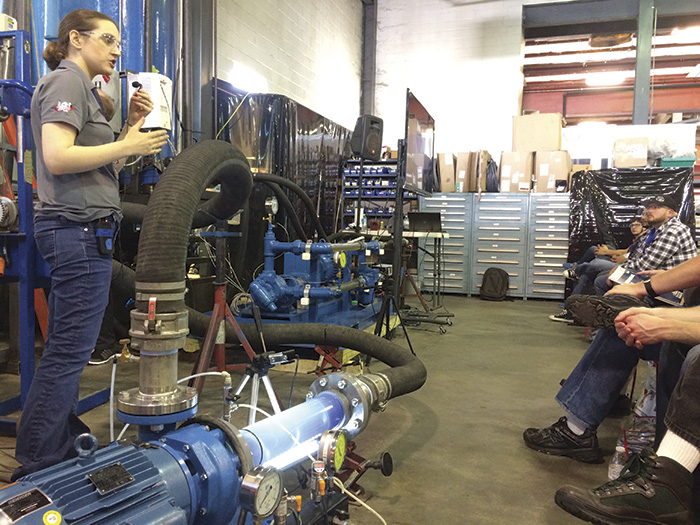
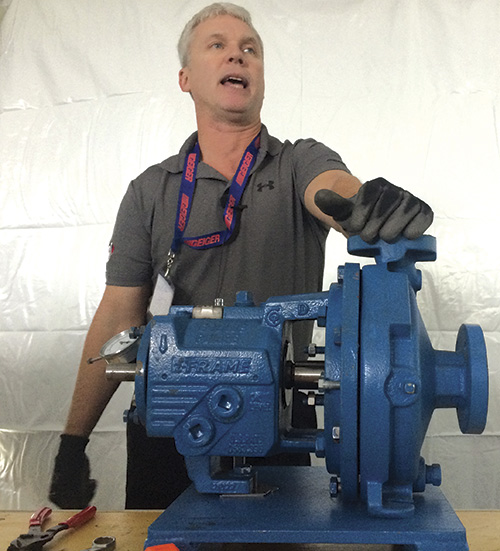