Pressure gauges are inexpensive components that can predict the causes of poor reliability in centrifugal pumps and prevent costly repairs and downtime.
06/19/2014
In today’s industrial facilities, using reliability-centered maintenance as the primary approach to reduce maintenance costs and operational downtime is more commonplace. This approach may be hindered because most petrochemical facilities were built before this maintenance strategy became a priority. Even today, expansion projects planned to reduce costs often under-instrument equipment at the expense of losing the capability to effectively troubleshoot and predict issues. For rotating equipment, field instrumentation serves three purposes:
- Operators are often required to make decisions based on the parameters measured directly in the field.
- Maintenance and engineering professionals often use gauges to troubleshoot problematic equipment to determine the root cause of failure.
- Instrumentation can predict the causes of poor reliability before repeat equipment failures.
Pump Operating Point
Pumps are designed to achieve a specified design flow rate and differential head at which they should operate. Running within 10 to 15 percent of its best efficiency point (BEP) allows the equipment to minimize the vibrations associated with imbalanced internal forces. Note that the percentage off of BEP is measured in relation to the BEP flow rate. As shown in the pump curve in Figure 1, reliability suffers dramatically the farther a pump is operated from its BEP.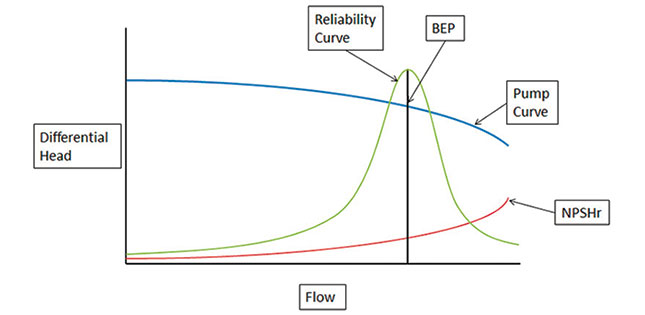
Net Positive Suction Head
Net positive suction head (NPSH) is a measure of a fluid’s propensity to stay in a liquid state. At zero NPSH, the liquid is at its vapor pressure or boiling point. Centrifugal pumps have a net positive suction head required (NPSHr) curve that defines the suction head required to prevent the fluid from vaporizing while going through the low pressure point at the eye of the impeller.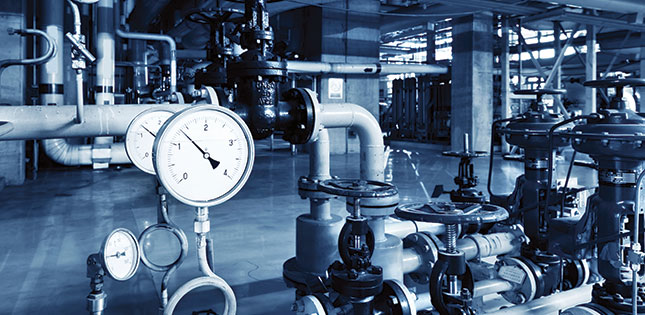