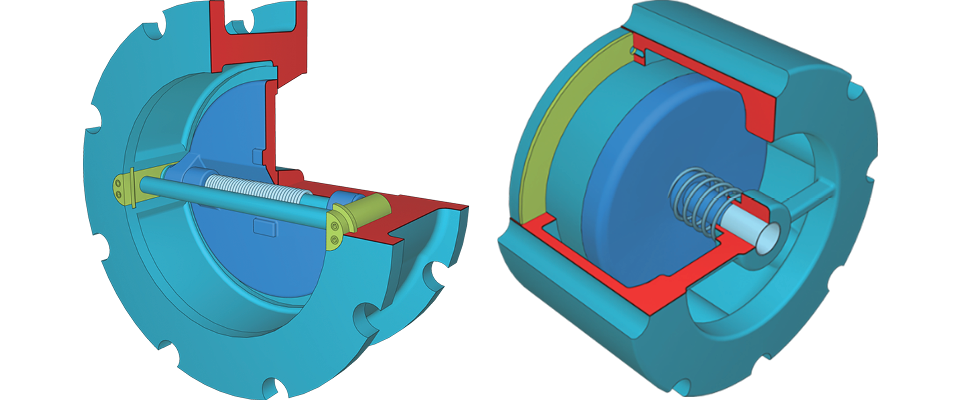
Check valves are crucial in fluid control systems. They protect pumps, compressors and pipelines from backflow damage and contamination. Used in various applications, from industrial piping and processes to household plumbing, check valves enhance system performance, prevent equipment damage and reduce maintenance costs. This article explores the different types of check valves, their functions and key considerations for choosing the correct check valve for a specific application.
What Is a Check Valve?
The fundamental purpose of a check valve, also known as a nonreturn or one-way valve, is to prevent a reversal of flow in the pipeline. They allow fluid, whether liquid or gas, to flow in one direction but close to prevent backflow in the opposite direction. They control the flow direction rather than starting, stopping or regulating flow.
All check valves are typically closed. When the pressure differential across the valve increases in the correct direction of the flow, the internal component (disc, ball, flap or diaphragm) pushes away from the seat, allowing the fluid to pass through. This minimum upstream pressure at which the valve opens is called cracking pressure—the specific cracking pressure changes based on the check valve design and size. If the fluid tries to flow backward, the internal component returns to its seat (due to gravity, spring force or reverse pressure), blocking the flow. A check valve must be fully closed before the line flow reaches zero to prevent reverse flow.
Types of Check Valves & Their Functions
Check valve closing depends on gravity, spring force, external weights and downstream pressure or a combination of these factors. Based on service conditions, each type offers unique advantages and limitations.
Swing check valves
As the name suggests, the valve uses a hinged disc that swings open when the fluid flows in the desired direction and swings back onto the seat to block flow in the reverse direction. These valves are ideal for large pipelines with high-volume and steady-pressure fluid flow systems. The top-hinged design allows the disc to fully open, thus reducing turbulence and lowering the pressure drop. However, when installed in high-pressure or variable flow applications, they are highly susceptible to water hammering when the disc slams shut suddenly. Swing checks are often used in wastewater and water supply systems.
The other two configurations of a traditional swing check are the dual disc and tilted-disc check valves.
Dual disc check valve
This valve is also known as a “double disc” or “double door” check valve. Instead of a single central disc, two spring-loaded, independently functioning half-circular discs are hinged on a central pivot point. The spring-loaded dual plate closes when the upstream pressure decreases, preventing backflow. These valves are ideal where space is limited. They are not recommended for wastewater applications and can be prone to vibration and wear over time. Dual disc check valves are most commonly used in heating, ventilation and air conditioning (HVAC), water supply lines and oil and gas systems.
Tilted disc check valve
While a traditional swing check valve’s disc swings on the hinge at the top edge, a tilting disc check valve’s disc pivots on a hinge offset from the center. The eccentricity of the pivot point reduces the travel distance of the disc, allowing quicker closure.
It also allows the disc to open at low flow rates. This makes these valves ideal for low and pulsating flow conditions. Fast closure speed minimizes reverse flow, making them well-suited to reduce the risk of water hammering. They are not recommended for wastewater applications. Tilted disc check valves are commonly used in pump discharge lines, water treatment plants, cooling water systems and industrial process lines.
Lift check valves
A lift check valve uses linear motion to lift a component to open and close a valve rather than the rotational movement of a swing check valve. Traditional lift checks rely on gravity to close the valve. On reaching sufficient fluid pressure, the disc lifts off the seat to open the valve. The disc drops back onto the seat due to gravity when the pressure drops or flow decreases. The valve can be installed horizontally or vertically in an upflow position. They are commonly used in high-pressure, clean fluid steam, oil or gas lines. The ball check valve and silent check valve are other configurations of a traditional lift check valve.
Ball check valve
A ball check valve uses a spherical ball that moves in and out of the seat within the valve body to control flow. The movement is either based on gravity or a spring. The simple design with minimal moving parts and an unobstructed full bore makes them ideal for viscous fluids and fluids with suspended soft solids. A ball check with a free-floating ball must be installed in a vertical flow-up position to function correctly. These valves are most commonly used in wastewater applications, pump stations and industrial processes.
Silent check valve
Also known as a “nonslam” check valve, a silent check valve improves upon a traditional lift check by incorporating a spring to open and close the valve instead of relying on gravity or flow reversal. As soon as the flow decreases, the spring pushes the disc back into the seat before the flow reverses. This ensures a smooth and quiet closure.
The silent check valve provides the fastest closure speed and minimum travel, which is ideal for eliminating water hammer. Some disadvantages are higher pressure drops and difficulty to repair. It is not suitable for fluids with high particulates. These valves are most commonly used in HVAC, water supply systems and power plants.
Nozzle check valve
Nozzle check valves are high-performance specialty check valves similar in function to silent check valves, but they also
provide lower head loss. The improved design works using the venturi effect. The internal shape is designed to improve flow. As the fluid comes through, the shape of the disc and flow path speeds it up while lowering the pressure at the narrowest point. Then, as the flow expands again, the pressure is recovered before it exits. This minimizes the head loss and improves performance.
Nozzle check valves are ideal for high-pressure, high-flow applications requiring minimal pressure drop and water hammer prevention. However, they are not suitable for fluids with suspended solids. These valves are commonly used in power plants, the oil and gas industry, industrial processing and water distribution and pumping systems.
Foot valves
A foot valve is a type of check valve installed at the inlet of a suction line to prevent backflow and maintain prime in pumps. Typically, a piston-type valve is fitted with a strainer on the inlet side of the valve. This allows fluids to flow into the suction pipe while the pump is running and, when the pump stops, prevents water from draining back, avoiding the need for repriming. The strainer filters the debris and prevents pump damage. It can clog over time and requires periodic maintenance. Foot valves are used in well pump systems, irrigation systems and fire protection systems.
Other specialty valves
Duckbill, diaphragm and stop check valves are specialty check valves designed for unique and demanding applications. These valves provide enhanced features such as improved backflow prevention, reduced pressure drop, minimized water hammer and the ability to handle extreme conditions like high temperatures, corrosive fluids or heavy solids.
Key Factors to Consider
Before selecting a check valve, users should consider the following factors:
Valve sizing and flow conditions
- The valve should consistently be sized for the application and not just matched to the line size. It should be sized to fit the actual flow conditions of the system, ensuring the valve remains fully open at normal operating conditions.
- Oversized check valves with insufficient flow can lead to chattering and wear.
- Undersized check valves will experience untimely wear and tear due to high-pressure drops and excessive flow velocity.
- Always use the valve manufacturer’s flow curves or valve flow coefficient (Cv) data to match the system’s flow rate and make an informed decision.
Type of fluid
- Consider whether the fluid is liquid, gas or slurry.
- Check valves handling compressible fluids require different considerations than those for incompressible fluids.
- Clean fluids will allow for a broader choice of valve types.
- Dirty or abrasive fluids may impact the valve performance and require more robust and specialized valves like a swing check with an external lever and spring or duckbill check valve.
Pressure and temperature ratings and material compatibility
- Always select a check valve with pressure and temperature limits suitable for the operating conditions.
- The valve should withstand the system’s operating condition and proof pressure ratings to ensure a safety margin and protect from unexpected pressure spikes.
- Check that the valve material is compatible with flowing fluid media. Generally, the valve material matches the system piping material.
- Sealing material should be compatible with the fluid flowing through the valve.
- Material compatibility is essential for ensuring the longevity and performance of the valve.
Valve location and installation orientation
- When installing a check valve, it is critical to maintain a proper distance from pumps and fittings to allow smooth flow and prevent turbulence.
- It is recommended to have at least five pipe diameters downstream from elbows and ten pipe diameters downstream from tees and control valves (MSS-SP-92 valve user guide). Consult with the valve manufacturer to install at less than the recommended distance.
- Always make sure the flow arrow is pointing toward the flow.
- Most check valves will work in horizontal piping, but only axial flow check valves like spring-assisted silent checks and nozzle checks would suit vertical flow up. Swings checks are susceptible to water hammer in vertical upflow from the discs slamming against the seats.
- Horizontal position should be the preferred option whenever possible.
Space limitations
- Consider available space for installation.
- Ensure the valve’s dimensions are compatible with the system layout.
- Wafer-style check valves and compact configurations are perfect for tight spaces.
Compliance with industry standards
- Adhering to industry standards ensures safety, durability and regulatory compliance.
o Water applications: AWWA C508
o Oil and gas pipeline: API 6D, API 594
o High-pressure industrial use: ASME B16.34
o General testing and performance: API
598, ISO 5208
Maintenance and life cycle costs
- Whenever possible, select a valve that allows easy inspection and maintenance. Valves with fewer moving parts are generally more reliable.
- Consider the cost of replacement and potential downtime. Investing in a high-quality valve may lead to long-term cost savings due to reduced maintenance and better system efficiency.
Check valves are integral in any fluid system. Engineers and operators can make informed decisions by understanding the different types of check valves and their specific applications. Proper selection and installation of check valves contribute to the reliability and longevity of fluid control systems, making them an essential component in various industrial applications.