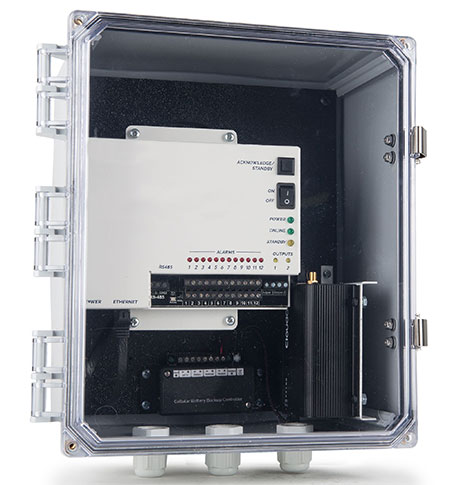
Pump failures can cause operational disruptions, costly repairs and potential environmental hazards. By integrating remote monitoring and sensor technology, plant personnel can detect possible issues early and prevent pump failures.
Common Causes of Pump Failures
A variety of circumstances can cause pump malfunctions, depending on the type of pump and the application. Here are some frequent causes of pump failures:
- Mechanical wear and tear: Wear of pump components such as bearings, seals and impellers due to continuous operation
- Electrical issues: Motor overheating and winding problems, insulation deterioration, electrical surges and short circuits
- Hydraulic issues: Cavitation, air entrainment, flow blockages and sudden changes in flow rate or pressure
- Operational errors: Incorrect installation, improper pump selection, inadequate maintenance and dry running
- Environmental factors: Corrosive fluids, extreme temperatures, blockages and contaminants
Types of Issues Detected by Remote Monitoring
Remote monitoring and sensor technology can identify a wide range of issues that may lead to pump failures, including unusual vibration patterns that can indicate misalignment, bearing wear or cavitation.
Sudden changes in temperature can signal motor overheating or lubrication problems. Abnormal pressure levels can suggest blockages, leaks or pump cavitation. Flow rate deviations can indicate issues like clogs, leaks or inefficiencies in the pump system. In addition, monitoring electrical parameters can detect irregularities such as voltage spikes, motor insulation failure or electrical imbalances.
Benefits of Early Detection of Potential Pump Failures
Preventive maintenance based on real-time data can reduce the frequency and severity of pump failures, lowering repair costs and extending the life span of equipment. Continuous monitoring ensures pumps operate within optimal parameters, enhancing system reliability and reducing downtime.
Early detection of issues can enhance safety by helping to prevent catastrophic failures that may pose safety risks to personnel and the environment. In turn, consistent and reliable pump operation helps facilities meet regulatory standards and avoid fines or penalties.
Remote Monitoring Systems
Remote monitoring systems alert operators to environmental and equipment changes that could lead to significant issues. These systems are installed at both staffed and unattended sites to provide continuous monitoring. The core component is a base unit that continually gathers data from existing equipment or sensors placed at critical points within the facility.
Each monitored condition requires a dedicated sensor input on the base unit. Advanced remote monitoring systems integrate with equipment operated by programmable logic controllers (PLC) or building automation systems (BAS).
Cloud-based remote monitoring systems leverage industrial Internet of Things (IIoT) technology, allowing operators to access devices in real time from anywhere in the world. These systems provide current status updates of all monitored conditions and send alerts to personnel whenever changes occur that could indicate potential problems. In addition, they automatically log data, allowing operators to analyze trends and enhance performance across the entire system.
Cloud-based systems store large volumes of data in networks of remote servers. Providers of remote monitoring services use private cloud systems to protect data security and prevent unauthorized public access. These platforms are monitored 24/7, with multiple backup server sites across the country to ensure continuous operation.
Operators can access remote monitoring systems through an internet or Wi-Fi connection. Alternatively, users can opt for cloud-based monitoring systems with a cellular modem, which transmits data to the cloud via a cellular connection.
A cloud-based unit continuously sends signals to the cloud to confirm it is online. If the internet connection is lost or a cellular communication issue arises, the system alerts designated users via phone, text or email. Data is not lost during interruptions because the device internally stores all information gathered during the downtime and uploads it to the cloud once the connection is restored.
Monitoring Electrical Current & Voltage to Extend Pump Life
Remote monitoring systems are essential for continuously measuring a pump motor’s electrical current (amperage) and voltage. This practice enables operators to identify potential issues before they become major problems. Significant increases or decreases in current can signal a malfunction that needs immediate attention.
Running a pump at overcurrent for extended periods, even by small margins of 5% to 10% over its rating, can cause overheating, internal damage and premature failure. Overcurrent can result from failing bearings, clogged lines or material jams within the pump.
When overvoltage occurs, the increased current can cause motor temperatures to rise when the load decreases, leading to a surge in voltage to the pump’s motor. Conversely, blockages that reduce flow can cause undercurrent situations. If voltage drops under heavier loads, the motor can experience a low-voltage state, increasing its electrical current.
Problems like suction loss and jams can cause severe damage to the motor or pump long before thermal overloads trip. These issues can be detected almost immediately by monitoring the drive motor current with a current transformer.
In any pump setup, the current drawn by the motor is directly related to the load size. Using a current transformer on the pump’s incoming power line can monitor this current draw. A current transformer is a coil inductively coupled to the motor’s alternating current (AC) input. It produces a signal that is directly related to the current used by the motor, and that signal trips an alert.
Wastewater treatment plants also use current transformers to monitor motor conditions at remote lift stations. The data gathered from each motor can be analyzed to forecast potential failures.