HI Pump FAQs
Hydraulic Institute
09/20/2017
Q: What are the advantages of a progressive cavity pump?
A: A single screw pump is a type of rotary pump known as a progressing cavity pump. The single screw construction of the pump and positive displacement pumping method lend this type of pump to a wide range of applications. Progressing cavity pumps have a rotor with external threads and a stator with internal threads (see Figure 1).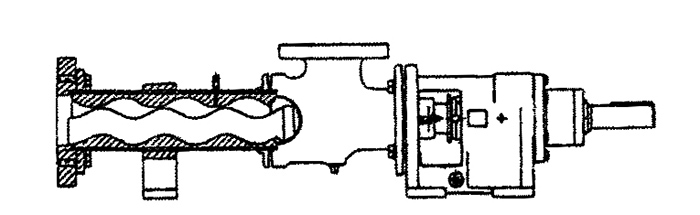
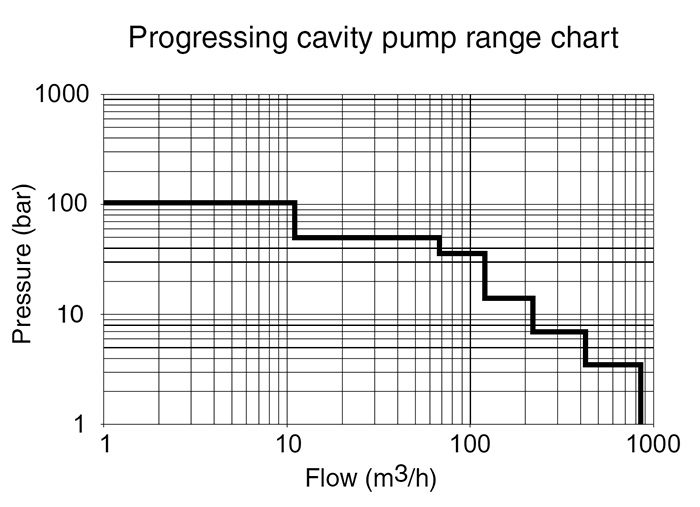
Q: What types of mechanical seals are used in wastewater applications?
A: Mechanical seal technology is continuously progressing and can be applied to almost any pumping application when the right considerations have been addressed. In wastewater applications the two seal arrangements commonly used are single seal (see Figure 3) that can be traditional or split design and dual pressurized (double) seal.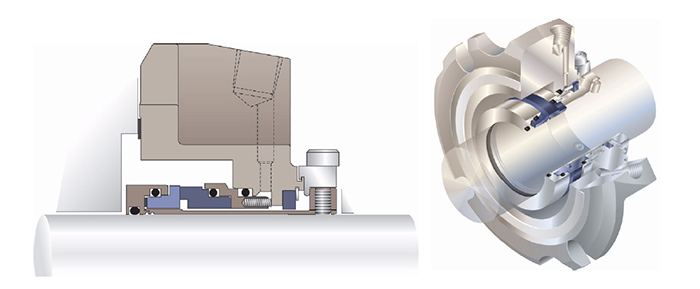
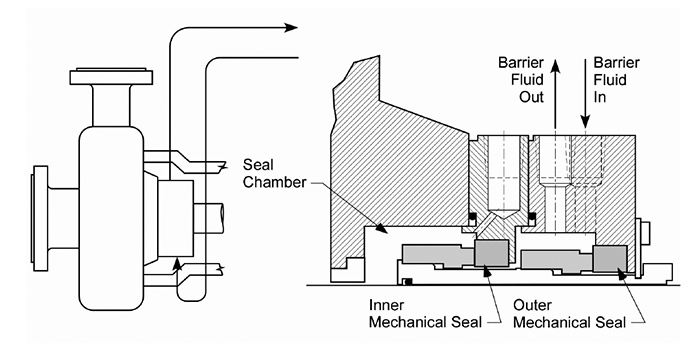
See other HI Pump FAQs articles here.