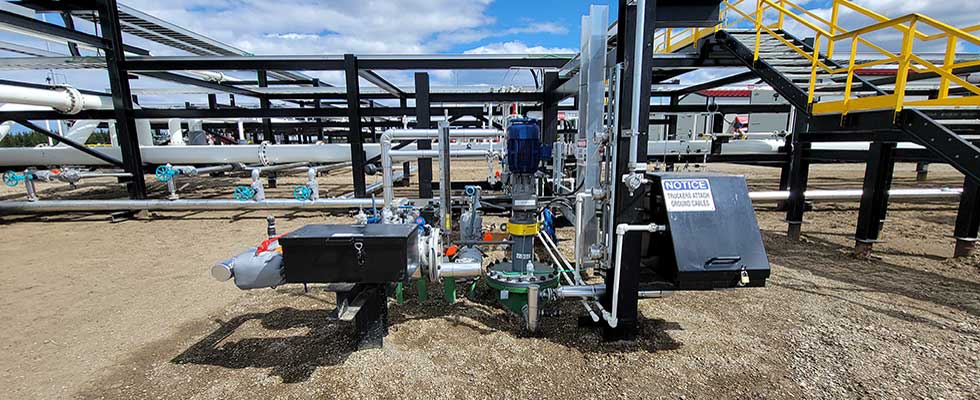
In the past, centrifugal pumps were the norm for many oil and gas applications. But such pumps require relatively high net positive suction head available (NPSHa) levels and are often susceptible to cavitation. Operators at two different types of oil and gas facilities have found progressive cavity pumps to be an efficient alternative solution, offering better suction capabilities at lower net positive suction head required (NPSHr) levels than centrifugal pumps. Progressive cavity pumps are also an energy efficient option, resulting in operational cost savings.
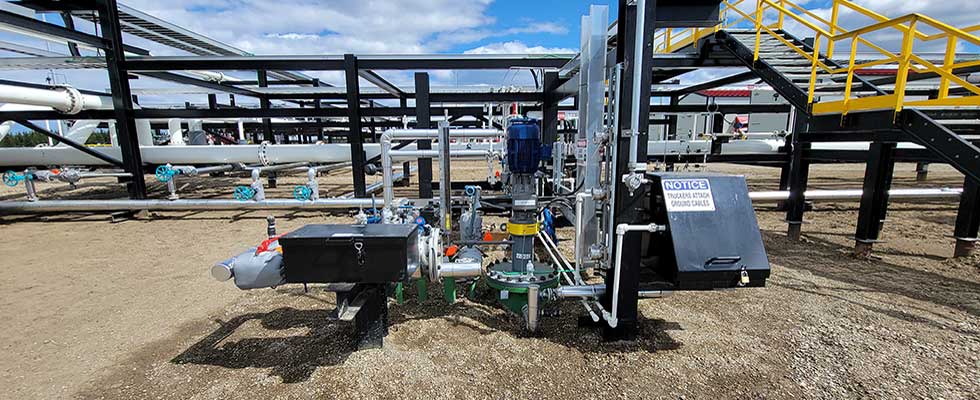
Pump Solution Needed
Engineers for a pipeline company that transports lighter hydrocarbon liquids produced in Canada were designing a high-pressure flare system for a bulk storage terminal project. They needed a pump solution to empty the flare knockout drum (FKOD) vessel, an integral part of the flare system.
FKODs are essential components of industrial pressure relief systems at gas and petroleum sites and play a crucial role in safe operations. Also called vapor liquid separators or knockout pots, liquid knockout drums capture and remove accumulated liquids that condense during the ordinary expulsion of relief gases. Flare systems generally require an FKOD to separate liquid from gas and to hold the maximum amount of liquid that can be relieved during an emergency situation or maintenance activities.
Knockout drums are typically located on the main flare line upstream of the flare stack. These vessels are either above-grade or below-grade and typically operate at vapor pressures of up to 103 kilo-pascals-absolute (kPaA). There is often not a lot of energy to get the fluid into the pump suction. In this project, the fluid was light oil/condensates (C5+) with a low viscosity of 0.2 to 0.7 centipoise (cP), so the engineer sought pump options other than typical centrifugal pumps, which require higher NPSHa levels and can be susceptible to cavitation. The client also required a pump that can achieve high discharge pressure.
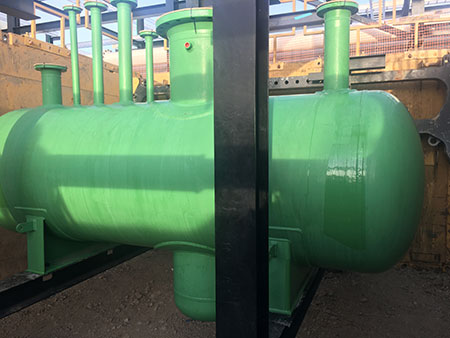
The project engineers were trying to make the FKOD pump more efficient because they wanted to operate within the specified best efficiency point (BEP). They eventually selected a vertically mounted progressive cavity pump, which provides better suction capabilities at lower NPSHr levels than some other pumps. Progressive cavity pumps can handle low (or high) viscosities; they can operate more efficiently with less wasted energy.
Progressive cavity pumps work well for above-grade and below-grade sump tanks. Semi-immersing the pump in the tank enabled operators to drain the tank down to only a few inches of liquid at the bottom.
Moreover, progressive cavity pumps are better at handling variable flow and pressure rates where the time needed to empty the tank also varies. They are also able to adapt to changes in viscosities, vapor pressure and specific gravity—factors that influence pump performance and reliability.
Another benefit of the vertically mounted progressive cavity pumps over horizontally mounted pumps under an above-grade tank is the availability of a sealing design that channels any leakage from the mechanical seal back into the sump, reducing the risk of environmental contamination.
Waste Oil Storage Tank Reinjection
A major energy pipeline company was seeking to streamline its waste oil storage tank pumping system. It wanted an option that could replace its two-pump system, in which a cantilever pump lifted the waste oil out of the tank and a high-pressure piston plunger injection pump moved the oil back into the pipeline system.
Two pumps for each storage tank resulted in double the maintenance. In addition, the high pressure required to operate the piston pump resulted in significant pulsation that caused pipe stress. The company wanted to eliminate the pipe stress and simplify the system with one pump that could provide smooth, pulsation-free conveyance.
The company operates one of the world’s longest crude oil and liquids transportation systems, conveying crude oil and other liquid hydrocarbons to refining markets in the Midwestern United States and Eastern Canada. Pumping stations are located all along the pipeline powering the liquid fuels through the pipeline. At each pump station, a 5,000-gallon (19,000-liter) underground storage tank (buried below the frost line to prevent the liquid from freezing) is used as a collection point for waste oil from service work that is performed on main pipeline pumps. As the collection tanks filled, the company needed to pump the liquid from the tank back into the pressurized pipeline.
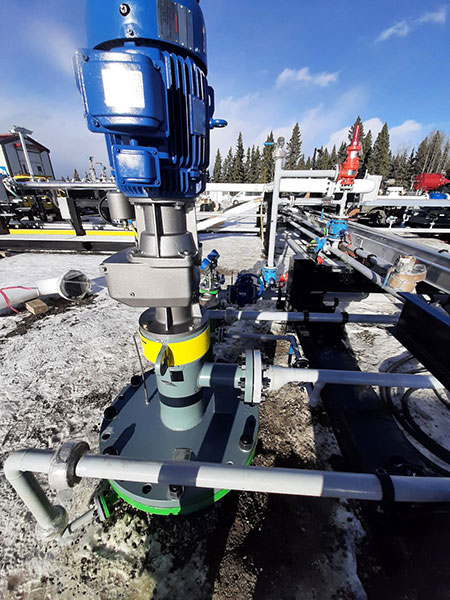
The company eventually opted to replace the two-pump system with a vertical, semi-submersed progressive cavity sump pump that could lift the heavy oil out of the tank and had the capacity to achieve 700 pounds per square inch (psi) (48 bar) of differential pressure, should the system require it in an upset condition.
The pump included a customized mechanical seal and a common pump length with a drop tube and strainer to accommodate any changes in sump depth. The pump also eliminated the need for universal joints by incorporating a flexible connecting rod; even if it leaked, the oil would drop back into the tank. The pump was also designed to operate in reverse, requiring the seal to be on the discharge side and the entire housing to be pressurized. The pump’s rotor/stator system was located at the lowest point, thus avoiding dry-running. The entire pump’s space-saving design (besides the drive and discharge flange) disappeared into the tank, providing for a clean installation. No additional effort was needed to heat and isolate external equipment—an important attribute in ambient operating temperatures down to -40 F (-40 C).
To date, there are many of these pumps operating in the field. A number of these pump stations operate in remote locations, so the single pump solution has reduced operational costs and field maintenance.
Great distances must often be covered to reach ports or refineries. Progressive cavity pumps can maintain a high conveying pressure at the lowest possible pulsation, making them an optimal solution for such applications.