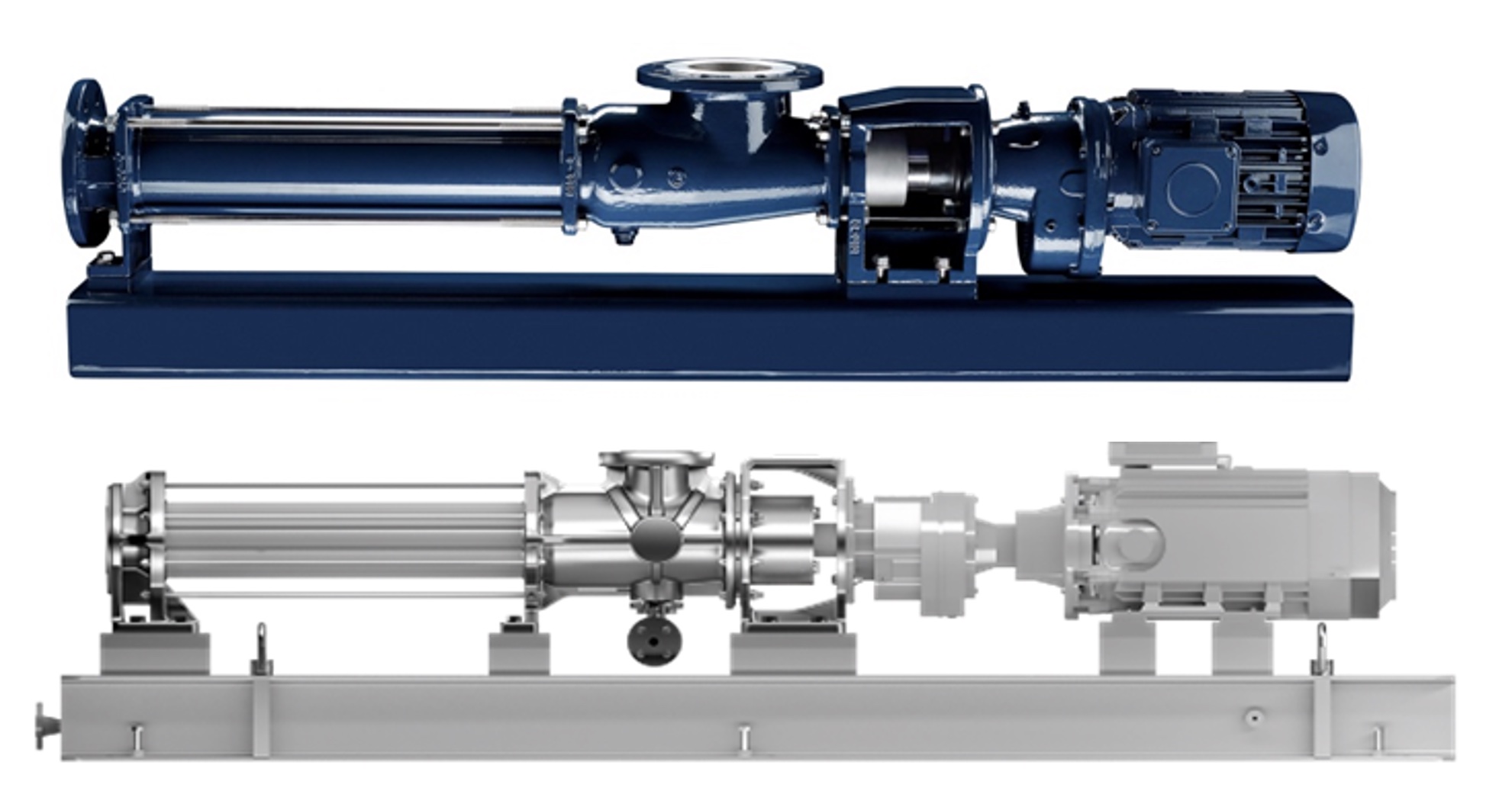
The oil and gas industry presents some of the most challenging pump applications. Engineers often encounter multiphase fluids, a wide range of viscosities, sensitive oil-water mixtures and high temperatures when selecting the appropriate pump. While centrifugal and multiscrew pumps are frequently used, there are many applications that could benefit from progressive cavity (PC) pumps. This article will explore these applications across different industry sectors and examine some of the features that distinguish these pumps in the field.
Upstream
In exploration and production, pumps must typically handle solids-laden fluids. On a drilling rig, the prime mover for the drilling mud is generally a triplex piston pump. This type of pump is selected due to the high flow rates and pressures required. Drilling mud is pumped down the drill string and exits through jets on the bit. As the mud returns through the annulus, it carries cuttings from the rock formation. These cuttings are filtered out in a process called “solids control.”
As the mud passes over the shakers, cuttings are filtered out and transferred into a bin. The remaining mud is then pumped to a centrifuge to further remove solids so it can be circulated back to the pits. In the solids control process, there are two areas where a PC pump is well suited.
The mud coming from the shakers still has residual solids and higher viscosity, which can be a challenge for centrifugal pumps. The PC pump can handle high viscosity and solids-laden products due to the large cavity openings and sealing line that prevents slip.
The second area is in flocculant metering before the mud enters the centrifuge. In some cases, it is necessary to dose flocculant into the mud stream to increase the efficiency of the centrifuge. A PC pump works well in this application because it delivers consistent volume with each revolution in a steady, nonpulsating pumping action. This prevents overdosing and is more cost effective than other positive displacement metering pumps.
Once the well is drilled, completed and put into production, operators face the challenge of handling the produced fluids. Traditional operations stored produced oil and water in tanks located near the wellhead and flared off excess gas. However, with efforts to reduce carbon emissions, companies have been exploring the use of tankless operations and capturing excess gas for sale or use in generators to power existing equipment.
In tankless operations, a pump is required to move the fluids to a central gathering location. PC pumps are suited for this application because they can handle high gas content (up to 99%) as well as a wide range of viscosities with minimal effect on performance. They can also handle solids well due to the large cavity openings. Specialty stator elastomers have been developed to resist wear from abrasive solids and chemical attack from hydrocarbons and hydrogen sulfide, a common contaminant found in production fluid.
Midstream
Before midstream operations, the fluids produced from the well must be separated and accurately metered for distribution. If a pump is required to boost the pressure before entering the separation equipment, a PC pump is a great choice. With the sealing line running the entire length of the pumping element, slip is minimized. These pumps also operate at low speeds (up to 400 rotations per minute [rpm] typically) which makes them inherently low shear. A low-shear pump is critical in this application because it limits the formation of oil-water emulsions that make separation difficult.
The measuring process is known as lease automatic custody transfer (LACT). This is typically handled by a prepackaged skid known as a LACT unit. The skid features a basic sediment and water meter, a flowmeter and various valves to control the path of the fluid. If the sediment and water content is too high, the fluid is directed back to storage. If the sediment and water content is within tolerance, the flow is totalized and recorded to facilitate the transfer between the operator and the midstream company. After the oil passes through the flowmeter, it must be pumped into the pipeline. This pump is known as a booster pump since it must overcome the relatively high pipeline pressure. PC pumps are well suited for this application because they can handle this task with minimal pulsation. Other positive displacement pumps capable of these pressures typically have a reciprocating action that causes pulsations that can damage attached equipment and reduce the metering accuracy on the LACT unit.
Downstream
After the midstream operator transfers the hydrocarbons to the refinery, some of the most demanding applications in the industry are seen. The American Petroleum Institute (API) has even developed specifications for process pumps and mechanical seals intended for use in petrochemical services. PC pumps fall under API 676: Positive Displacement Pumps – Rotary, and mechanical seals fall under API 682: Pumps – Shaft Sealing Systems for Centrifugal and Rotary Pumps. API 676 was written for a variety of different rotary positive displacement pumps, with multiple screw pumps at the forefront. Therefore, it is important to understand the requirements as they apply to PC pumps.
Due to the eccentric kinematics and elastomer stator, PC pumps are not well represented in API 676. Some deviations and clarifications are always necessary. Most PC pump manufacturers have options to upgrade industrial pumps to a higher degree of compliance with API 676; however, more compliance will always increase the overall project costs and typically provide little benefit to the user. It is advisable to have an open discussion with the pump manufacturer about the actual application requirements during the requisition process.
Typically, downstream refineries will require a higher degree of compliance to API 676 than upstream or midstream operators. Some common modifications to increase the compliance of industrial PC pumps are:
1. Housing design
API 676 pump housings are designed to handle increased pressure. It is common for purchasers to specify the suction housing is designed for the same maximum allowable casing pressure (MACP) as the discharge in accordance with section 6.3.3.2.
Housings are also designed to handle API nozzle loading as specified in section 6.7.1. Purchasers commonly require 2x API nozzle loads, so many manufacturers offer this as an option by providing additional support for suction housing.
If a casing drain is required, API 676 specifies a flanged design rather than a threaded design typical in industrial PC pumps. Manufacturers must account for this in the design of the suction housing.
Welding of process parts is permitted; however, it comes with increased documentation requirements. It is beneficial for the purchaser if pump manufacturers utilize cast housings to limit the quality assurance testing and documentation.
2. Seal design
Shaft seals, according to API 682, are typically larger than traditional seals, so most PC pump designs need to be modified to accommodate the larger footprint. The drive adapter or lantern is typically designed to adjust for these features.
API 676 also requires the seal to be removed without disturbing the driver (motor). To accomplish this, a bolted gland design is used, which is not typical in standard industrial PC pumps.
3. Baseplate design
Standard pump baseplates are typically bent steel in the shape of an inverted “u” or a top hat profile. API 676 requires flatness tolerances between all mounting points that are not possible with the standard design. To achieve the flatness requirements, manufacturers must use fully welded structural frame bases with large mounting blocks that are precisely machined. This provides little benefit in most cases, with a high overall cost. With the low-speed operation and elastomer stator element of a PC pump, alignment is not as critical as other pumps represented in the specification. Usually, a compromise is found in a standard baseplate modified with a drain connection, lifting lugs and leveling screws, which satisfies many of the other requirements in section 7.4.
Once the requirements are determined, there are critical applications where a positive displacement (PC) pump can be preferable to other designs. In a refinery, nonvolatile liquids are collected in an open-drain vessel, while volatile liquids are typically collected in a closed-drain vessel. When these vessels are full, the liquids must be transferred for separation and treatment.
In an open-drain system, users typically find a mixture of oil and water. As previously discussed, the low-shear characteristics of a PC pump can help prevent emulsification, thereby aiding in the separation process. Closed-drain systems are typically operated at vapor pressure equilibrium, which means the net positive suction head available (NPSHa) is extremely low. PC pumps can effectively handle such low-NPSH situations due to the compression fit between the pumping elements.
Additionally, a vertical PC pump may be installed in a can below the closed drain vessel to increase static head and prevent cavitation.
The applications mentioned in this article do not encompass all the possible uses for a PC pump. However, readers should now have a fundamental understanding of where a PC pump can be beneficial in optimizing system performance. While a PC pump may not be suitable for every application, its simple yet robust design offers unique advantages, particularly in situations involving solids, high-viscosity, shear-sensitive media and low NPSHa.