The addition of a cardan joint helps resolve wear and failure and delivers improved angularity and smooth transmission of radial and axial loads.
05/16/2014
Progressive cavity (PC) pumps solve many of the issues that occur in demanding pulp and paper processing and production. They are chosen for many applications, including:
- The pulper
- The paper machine
- Coating kitchen
- Waste treatment and recovery
PC Pump Advantages
PC pumps are energy efficient and experience long life in harsh applications. Self-priming and with a low net positive suction head required, their positive displacement flow is proportionate to the speed and independent of discharge pressure. With their large capacity, PC pumps reach flow rates up to 1,500 gallons per minute and have high-pressure capability. With friction losses, pressures as high as 2,000 psi can be achieved. Though end users should never let a pump run dry, PC pumps can achieve a vacuum of 28 inches. Regardless of fluctuations in media viscosity, temperature or abrasive characteristics, PC pumps provide low pulsation and smooth, repeatable flow, providing precise metering in real-world applications. If the pumped media is shear-sensitive, these pumps are ideal solutions because of their low internal velocities, which add little energy to the media, minimizing the degradation of sensitive products.
- Pumping of multiphase media
- Quiet operation
- Simplified maintenance because no special tools are required
- Decreased downtime for maintenance
- Flexible mounting arrangements—such as vertical mounts or mounting a twin shaft grinder directly on the inlet
Cardan Joint
All PC pumps have quality manufactured rotors and stators, and optimizing these components is important. However, just as important is how each pump handles the eccentric motion and strong radial and torsional loads. Initially, this was accomplished with an unsealed pin on each end of the connecting rod. The connecting rod and pin are typically made from hardened steel or stainless steel and combine to connect the concentrically rotating drive shaft to the eccentrically rotating rotor. The pin is subjected to extreme concentrated load and lubricated by the product, which is often abrasive, resulting in premature wear and failure. The pins and connecting rod become the sacrificial lamb of the pump. A sealed pin joint was developed and incorporated by many manufacturers. This helped because the pin operated in a well-lubricated bath, but it was still subjected to extreme concentrated loads, and this change was not a substantial upgrade for the tougher applications.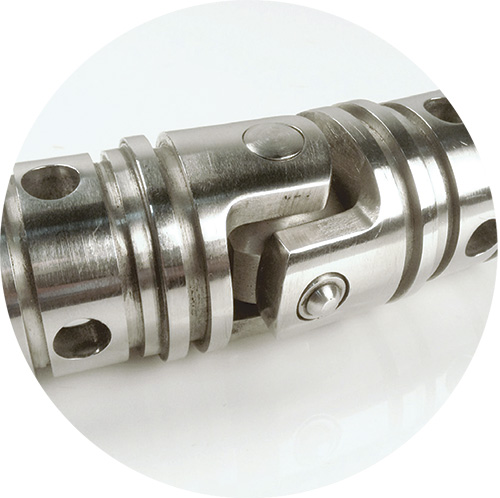