Oil and gas drilling and processing operations are arguably one of the harshest industrial environments into which any equipment can be deployed. These can be high risk and high reward operations with success and profitability closely linked to maximizing equipment uptime to maintain a consistent throughput of production. This performance is imperative within the oil and gas industry, which relies heavily on the movement of fluids in closed systems and can be slowed or brought to a standstill due to a clogged pump or valve. Crude oil refineries and drilling sites are especially at risk because of the high solids content of slurries moving through these operations, particularly relating to storage tank bottom cleaning at refineries and the reclamation of drilling fluids at the drill sites. Pumps, centrifuges and liquid-solid separators, critical to keeping production moving in these operations, are subjected to extremely demanding industrial conditions under a constant onslaught of hydrocarbons like paraffins and asphaltenes and inorganic solids like rock, sand, rust and heavy metal oxides. Consequently, this equipment experiences a high incidence of interruption and repair, impacting production throughout as well as operational costs.
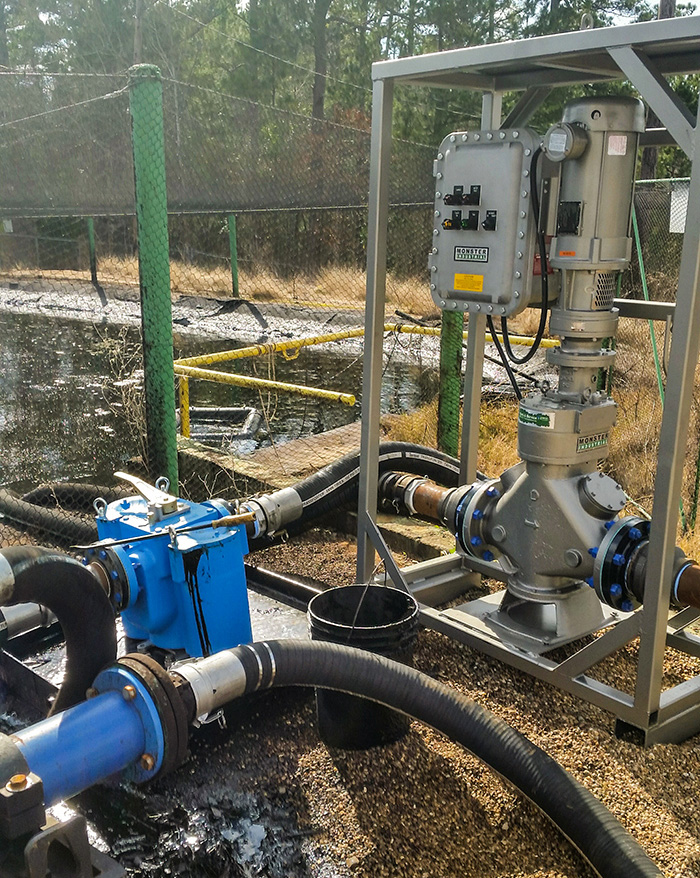
Crude Oil Tank-Bottom Sludge Removal
One of the most challenging issues for refineries is the development of methods to minimize the cost of removing and disposing of crude oil sludge in storage tank bottoms. Crude oil sludge from storage tanks is a multiphase water/oil/solid composite, composed primarily of heavy hydrocarbon deposits, paraffins and asphaltenes and possessing a semisolid physical state. It is produced under normal storage conditions by the gradual sedimentation of heavy oil components, varying in consistency, density, thickness and composition across the whole tank bottom. Inorganic solids in the crude oil, such as clay, silica, calcite and corrosion-produced residues contribute to this process, bringing more hardness and higher density to the deposit. The accumulating sediment compacts, resulting in a thick layer of sludge, which is difficult to remove. The sludge can accumulate many feet in depth and up to 100,000 barrels in volume, which causes a gradual reduction in the tanks’ storage capacity, and uncertainty of available volume. Refineries have inspection policies to verify the integrity of tank seals, flooring and roofs. To perform these periodic maintenance and inspection programs, the sludge must be removed. Tank cleaning, in the traditional sense, has involved opening or cutting a hole in the tank to remove the sludge, which is then openly transported to shaker screens, fed through a liquid/solids separator or centrifuge to reduce the volume of sludge waste, and subsequently transported to an off-site location.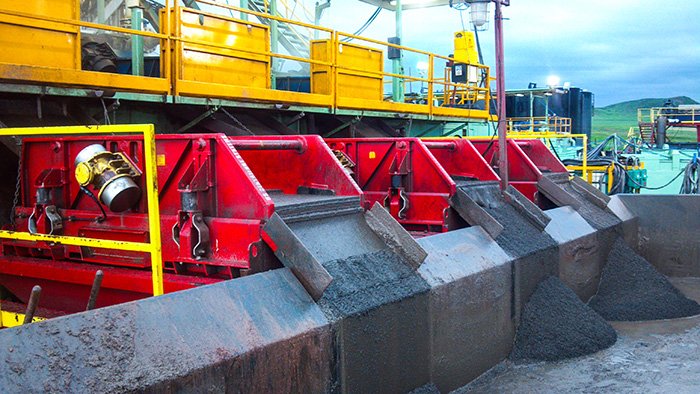
Reclaiming Drilling Mud from Drill Cuttings
Drilling fluids (drilling mud) are integral to the drilling process, serving to lubricate and cool the drill bit, as well as convey the drilled cuttings away from the bore hole. These fluids are a mixture of various chemicals in a water-based, oil-based or synthetic-based solution. Drill cuttings are broken bits of solid material that are produced as the drill bit breaks the rock. Drill cuttings vary in size, ranging from fine silt to gravel. For both environmental reasons and to reduce the cost of drilling operations, drilling fluid losses are minimized by stripping them away from the drill cuttings before the cuttings are disposed of. The drilling fluid is often reused. On drill sites, the systems used to reclaim mud are considered critically important to the process throughput and efficiency of the operation. Mud reclamation is primarily accomplished using shale shakers with vibrating screens to separate the mud from the shale, with subsequent processing of larger drill cuttings with centrifuges.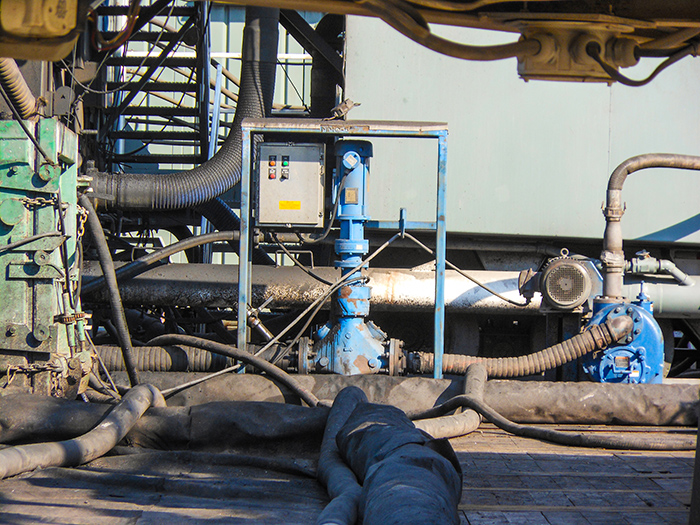
Adapting for Oil & Gas
With the increasing use of two-shafted low-speed and high-torque grinders being employed to protect pumps in petroleum-related applications, the suppliers of grinders have been adapting.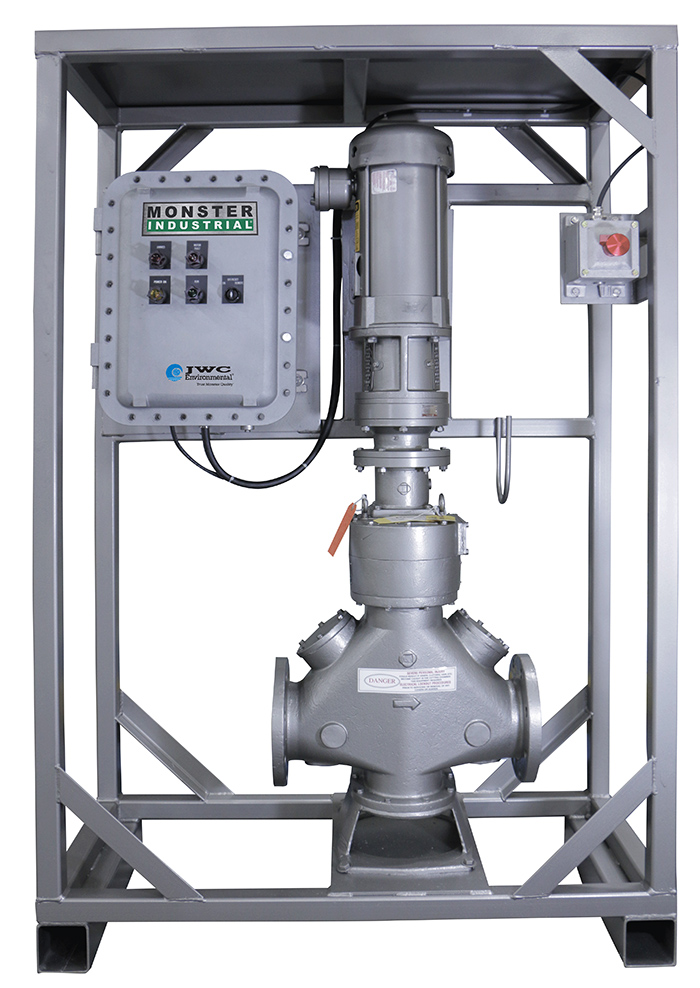