A number of options are available for controlling equipment and environmental costs in demanding applications.
03/01/2013
Abrasive media comes in many forms—from mining slurries to wood pulp and even substances as seemingly mild as liquid chocolate. This diversity rules out a one-size-fits-all solution for abrasive pumping applications. However, today’s broad range of materials, from carbon fiber packings to graphite-filled polytetrafluoroethylene (PTFE) bushings, includes products capable of meeting an equally broad range of abrasive wear requirements.
Carbon Fiber Packing
Few materials offer the abrasive resistance and heat dissipation of carbon fiber yarns. Braided compression packing made from this material excels under extreme conditions, including exposure to a variety of chemicals, temperatures approaching 850 F (454 C) in oxygen-rich atmospheres (up to 1,200 F/649 C in steam) and shaft speeds in excess of 4,000 feet per minute (fpm). The strength of carbon fiber yarns combined with their ability to draw heat from pump shafts make them the material of choice for resisting abrasive wear. Unfortunately, they do not seal as well as graphite foil packing. Upon closer examination, however, the speed and temperature capabilities of these two materials are similar. Consider this hypothetical scenario: An abrasive pumping application is under control using carbon fiber, except for excessive leakage across the packing set. Depending on the nature of the leaking media, it may not be desirable to have it pooling on the plant floor. Even if it is just water, excessive leaking media is lost profit. If the leakage is clean, the carbon fiber packing is effectively excluding abrasives.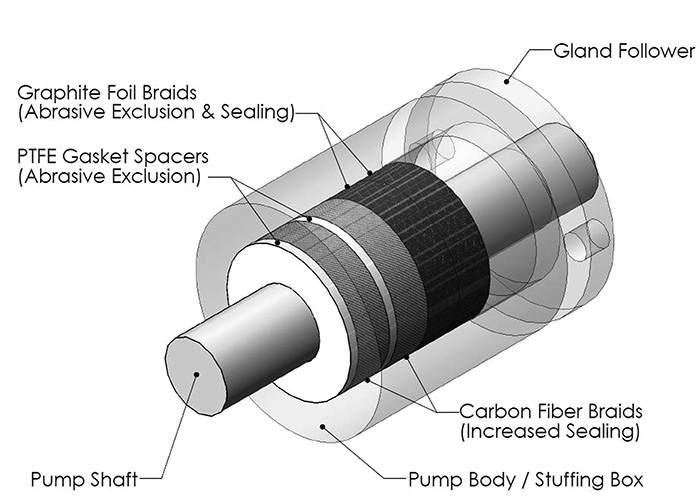
Carbon Fiber Rings and Foil Packing
When dealing with clean media, graphite foil packing becomes an option. At a subsequent repacking, it may be advisable to use just two carbon fiber rings in the bottom of the stuffing box and use graphite foil packing for the remaining rings. In this combination, the carbon packing clears the media of abrasive particles, and the graphite provides a tight seal. As a result, abrasive wear is kept in check, packing leakage is kept to a minimum, and the service life of the packing and equipment in which it is installed is extended.Gasket Spacers & Packing
Different materials and forms of material can be combined to create abrasive-resistant compression packaging for a variety of applications. For example, pure PTFE packing is required in chocolate processing to meet U.S. Food and Drug Administration cleanliness standards. However, it is not well-suited to abrasive service. This problem can be resolved by using PTFE-braided packing in conjunction with one or two spacers made from PTFE gasket material. The spacers are cut to fit tightly against the shaft and the wall of the stuffing box, creating a dam that excludes abrasives from the media. Placing one of these spacers at the bottom of the stuffing box and another between the packing rings can produce a marked improvement in performance. Incorporating gasket spacers is proven to extend packing life. In pulp and paper digesters, for example, this practice has increased the packing life from four months to more than a year, according to industry sources. As a result, some manufacturers offer packing sets engineered to meet specific application requirements. These sets are typically supplied pre-cut and packaged sequentially for installation with no additional cutting or measurements needed. Figure 1 shows a packing set incorporating gasket spacers, carbon fiber yarns and graphite packing.Flushing Systems
Sometimes, compression packing alone is not sufficient to provide protection from abrasive media, and flushing the stuffing box may be required. Traditionally, this is done using a lantern ring in the packing set. A lantern ring is a hollow, perforated spacer often positioned low in the stuffing box. When correctly used to combat abrasives, the lantern ring takes in clean fluid at a higher pressure than that of the pumping process. This higher pressure results in the fluid flowing out into the process, thereby flushing abrasive particles out of the stuffing box. Using lantern rings can be extremely effective but involves high volumes of flush media, resulting in increased operational costs. For example, if the flush media is water, it can cost more than twice as much to remove it downstream in the process as it did to introduce it.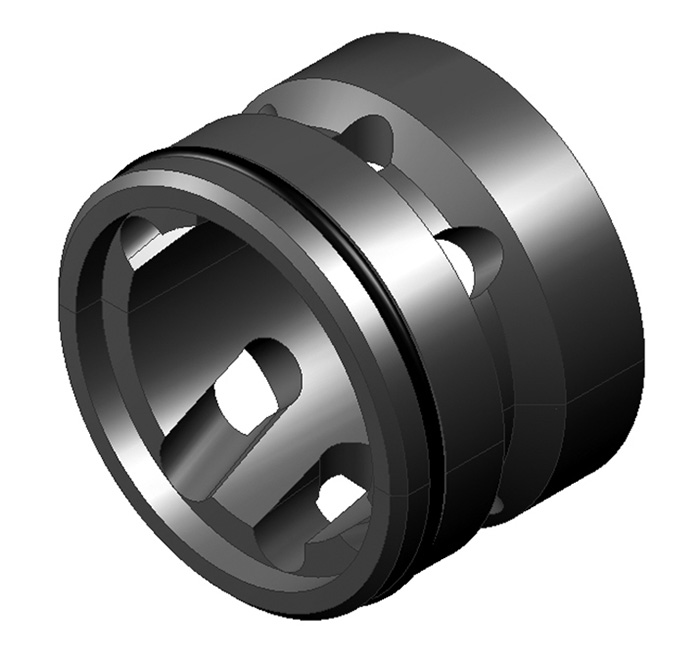
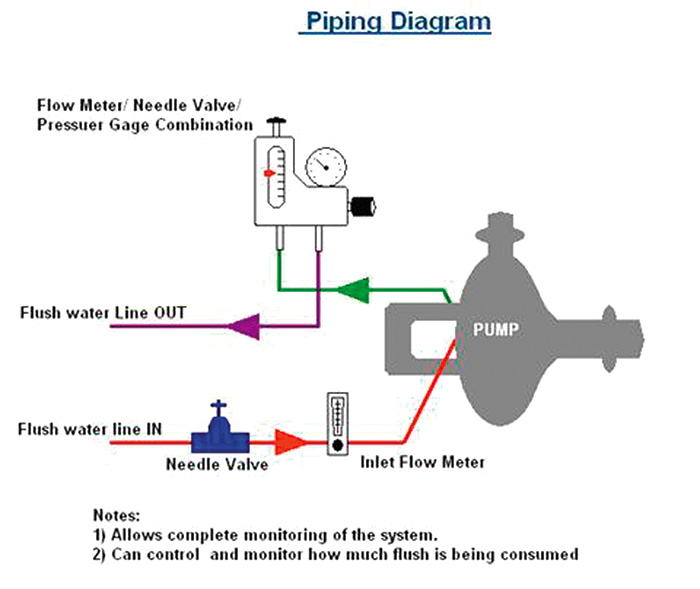