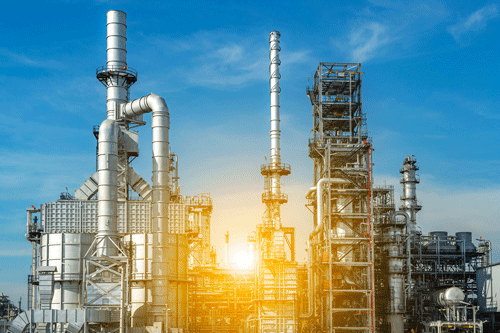
Sulfuric acid is the most commonly used chemical in the world. Sometimes referred to as the “King of Chemicals,” sulfuric acid is manufactured around the globe. China is the largest consumer (followed by the United States), and Canada is the largest exporter. Each year, approximately 265 million metric tons (MT) are produced.
It is estimated that the market for sulfuric acid will exceed 300 million MT over the next several years, representing a compounded annual growth rate (CAGR) of approximately 3%.
This growth is largely fueled by demand for agriculture, chemical and automotive manufacturing, metal processing and petroleum refining. Sulfuric acid is widely used in the production of fertilizers, pesticides, metals, detergents, gasoline, paints, paper, plastics and batteries. Sulfuric acid is produced from sulfur, through a process that involves five steps, which require a number of applications.
Combustion
Sulfur, obtained from natural deposits or through the desulfurization of natural gas or crude oil, is heated and thermally decomposed in a furnace. During this heating process, sulfur (S) reacts with oxygen (O2) in air to form sulfur dioxide (SO2). The molten sulfur is in a liquid form, and it is pumped into the furnace using a chemical service pump.
Gas Cleaning
The SO2 exiting the furnace must be free of impurities (such as ash or other solids). A quenching tower cools the combustion gas, and an acid spray mist removes any stray particulates. From there, an electrostatic precipitator removes any remaining nonsoluble dust particles. Once the impurities are removed, the SO2 gas stream is dried in a drying tower to remove any remaining water. There are multiple pumping applications at this stage, including an SO2 wash pump, an SO2 scrubber pump and an SO2 drying pump that must be able to stand up to concentrated (98%) sulfuric acid.
Conversion
SO2 gas is next oxidized and converted to sulfur trioxide (SO3) via a multistage catalyst converter with heat exchangers. During this step, the gas stream containing SO2 and SO3 exits the converter and is sent to a primary absorption tower where the SO3 is recovered from the gas stream. Compressors are used to move the gas streams at this stage.
Absorption
SO3 is recovered from the converter, where it is absorbed into concentrated sulfuric acid. This reaction produces oleum, also known as fuming sulfuric acid (H2S2O7), which is collected in a tank. The remaining SO3 has now been absorbed and is a clean gas that can be sent to the stack for safe dispersion into the atmosphere. Multiple pumps are used during this stage for primary absorption and for the final absorption of 98% sulfuric acid.
Dilution
In the final step, the oleum produced in the absorption step is pumped into a tank where it is diluted with water to produce sulfuric acid of varying concentrations (typically, commercial applications use sulfuric acid at concentrations of either 78%, 93% or 98%). Each concentration of sulfuric acid is then pumped to storage tanks.
Criteria for Selecting Pumps for Sulfuric Acid Units
Sulfuric acid is a dangerous and corrosive chemical, classified as a human carcinogen by the International Agency for Research on Cancer (IARC). Exposure from inhalation, ingestion or skin contact can cause kidney and lung damage, and severe exposure can cause chemical pneumonitis or pulmonary edema.
What makes sulfuric acid so dangerous is its exothermic reaction with water. When introduced to water or moisture, the solution reacts to create hydronium ions. This reaction releases large amounts of heat to the environment so strong that concentrated sulfuric acid can char paper by itself.
An Ideal Application for Sealless Pumps
External emissions are one of the biggest issues relating to pumping equipment used in sulfuric acid production. More than 85% of pump failures involve a mechanical seal failure or leakage through static seals.
When it comes to pumping sulfuric acid, leaks are to be avoided at all costs. One of the best ways to avoid leaks is to use sealless pumps. Sealless pumps operate much like conventional centrifugal pumps, but instead of packed glands or seals, they feature a sealless static containment shell that forms a completely sealed liquid end or pressure boundary.
Magnetic drive sealless pumps are hermetically sealed, eliminating any potential for leaks or emissions.
Worker Safety & Environmental Protection
Even though sealless pumps offer a safe and leak-free environment, some chemical processes demand additional protection. Many sealless pumps offer sensors and instrumentation packages that alert operators to system failure conditions, such as cavitation, overheating, low flow, dead heading or no flow. For the most hazardous pump services, sealless pumps should also have secondary containment options that can withstand the design temperature and pressure needed for the application to provide additional protection in the event of a primary containment breach following a system upset.
Reliability via Chemical Resistance
Materials of construction for a pump’s internals must be carefully considered. The harsh nature of sulfuric acid can wreak havoc on a pump’s internals. Many of the chemical catalysts used in the process add further demands on pump materials. A wide range of both metallic and nonmetallic materials of construction should be available for pumps used in sulfuric acid production to ensure suitability with a variety of concentrations, including 316SS, high-nickel alloys and ethylene tetrafluoroethylene (ETFE)-lined pumps.
Simplified Maintenance
The sheer volume of sulfuric acid production illustrates the need for reliable equipment that minimizes plant downtime, as many plants run operations around the clock. The ability to streamline maintenance (and plan predictive maintenance activities) helps operators increase plant uptime. Sealless pumps eliminate the need for seals and seal support systems, and they have fewer wearing components, which minimizes maintenance costs and increases mean time between maintenance (MBTM) intervals.
Energy Efficiency
Sulfuric acid production is an energy-intensive process. Electricity can account for 40% to 50% of operating costs. In many cases, the ability to manage this expense determines the plant’s profitability. Plants producing sulfuric acid require pumps with an efficient hydraulic envelope and low net positive suction head (NPSH) hydraulics. Small footprints are always preferred, not only to save space on the shop floor, but also to facilitate simple access for maintenance.
Features such as a nonmetallic containment shell with high electrical resistance can bolster efficiency of sealless magnetic drive pumps by eliminating eddy currents and preventing hysteresis losses during operation, which would
occur with a conventional metallic containment shell. This design feature not only reduces energy costs, but also eliminates heat generation.
10 Reasons to Use Sealless Pumps for Sulfuric Acid Production
When planning a new pump installation or an upgrade to an existing installation, the financial impact of seal support systems is considerable. Once these systems are installed, further costs can be incurred by the need to comply with local, regional or national environmental requirements, which involve monitoring the effectiveness of these systems.
By eliminating the seal and the associated seal support system, sealless pumps add incremental benefits to any sulfuric acid processing unit. Ten advantages that sealless magnetic drive pumps provide are:
- no seals and seal support systems
- complete fluid containment
- zero product emissions
- zero contamination of process fluid
- reduced installation and startup costs
- simple to maintain and operate
- longer mean time between failure (MTBF)
- no EPA monitoring
- improved operator safety
- protection of the environment