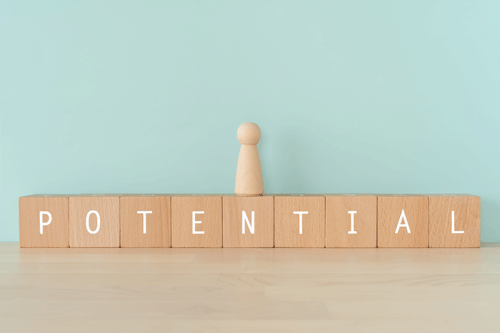
We often think of variable frequency drives (VFDs) as a component that controls a motor. However, we frequently fail to utilize—or are unaware of—the secondary uses of a properly implemented VFD-driven pumping system. In many cases, VFDs are utilized with pumps to implement proportional-integral-derivative (PID) control, lower energy consumption and easily vary pump flow rates, among other reasons.
Other uses of modern VFDs are often overlooked. Typically, a drive is controlled via analog speed reference, preset speeds or over a network. The drive is routinely used to communicate its operational status, output frequency and current. Contemporary VFDs are capable of much more to operators. In the era of Internet of Things (IoT), we assume we need to add dedicated sensors to collect data. Users should consider making better use of their VFDs, such as using them as advanced sensors.
More Than Just a Device to Spin the Pump & Motor
When a human machine interface (HMI) or supervisory control and data acquisition (SCADA) system is used in conjunction with a VFD, monitoring and data analytics can be provided. For example, the VFD can monitor incoming line voltage, output current, consumed power, hours of operation, torque and energy savings, among other values.
In most pumping systems, the drives are the most likely component to announce a problem in the system. Unlike systems with motors started directly on-line (DOL) with contactors, motors controlled by VFDs provide a means to output useful information to operators and maintenance technicians. Motor overloads, motor overtemperature and loss of network communications are some examples of the conditions that will cause a drive warning or fault. While a contactor with an overload relay can only communicate open or closed status via an auxiliary contact, a VFD can provide clear text and/or graphic status indication of the drive and pump. When an HMI or SCADA system is utilized, even more information can be easily communicated to operators and maintenance personnel from the drive. The net effect of providing users with understandable, pertinent information is a quick identification of the root problem and a rapid resolution of the issues.
Mechanical Failures & Faults
Often, a VFD alarm is not an indication of a VFD problem but rather an issue with the motor, pump or valve. It can be difficult to identify the root cause, as it is a human tendency to blame the messenger or, in this case, the VFD. Modern VFDs have methods to better pinpoint the root cause of the issue. A user can now configure a normal operational range by defining a system curve, upper limits and lower limits. The drive can also learn the pump system’s normal operational range and automatically populate system curve points and limits. If the system performs outside of the defined operational range, the drive will either generate an alert to warn operators or a fault to shut down the drive.
For instance, if the pump coupling breaks, the drive would generate a load warning or fault, notifying the operator of the issue. Likewise, if a pump bearing is damaged, additional torque would be required to operate the pump. This additional torque requirement would cause the VFD to operate outside of the established operational range. The abnormal load warning or fault alerts the operator to an abnormal condition, identified by the VFD but originating in the mechanical system.
Prediction of Future Issues
When we think of preventive maintenance for pumping systems, techniques like vibration or oil quality monitoring are typically the highest priority. Because of this, operators often ignore the built-in predictive maintenance functionality of contemporary VFDs.
A high-quality, modern VFD can predict its own demise well in advance of drive failure. Many VFDs are installed and operated in atmospheric environments that are corrosive to modern circuit boards. VFD manufacturers combat environmental corrosion by conformally coating the VFD’s circuit boards and even the drive bus bars. Conformal coating extends the useful life of VFDs, but the drive will eventually succumb to the environment. Some VFDs have sensors embedded in the circuit boards that measure the decay of the conformal coating. These sensors allow the VFD to alert operators and maintenance personnel to the impending failure of the conformal coating and subsequent failure of the VFD. Advance notice of pending VFD failure allows for drive replacement on the user’s schedule, rather than creating unplanned downtime. VFDs also monitor internal fans, capacitors and other components to determine how much longer a VFD can be relied on to function.
Monitoring the condition of internal VFD components is key to predictive maintenance; however, VFDs can also be used to automatically correct issues in the mechanical system. In some pumping applications, like lift stations, both fluid and solid materials flow through the pumps. Fats, oils, grease and rags cause over 40% of the issues encountered in lift stations. Implementing an anti-clog or deragging routine can minimize or eliminate issues caused by these materials. When triggered, the cleaning routine can oscillate the pump shaft, dislodging clogs and jams.
Most drives provide a configurable routine that can be easily optimized for the pumping system. Some pumps have minimum speed limits, and others cannot be turned backward without causing damage. In these cases, the routine can be created to pulse the shaft above the minimum speed limit and/or prevent reverse rotation. There is some evidence that periodically triggering an anti-clog routine will prevent degradation of pump efficiency over time in wastewater applications. Typically, an anti-clog routine can be trigged by several conditions simultaneously. Elapsed time, on VFD start, PID variable value and load are just some of the common anti-clog routine triggers.
Best Use of VFDs in Pumping Systems
Unlike a DOL-started motor, VFD-controlled pumping systems can ramp up to the required flow rate rather than immediately accelerating to the system’s full flow. Ramping a pump up to speed has multiple positive impacts on pump system life, like reducing pressure surges or water hammer. Changing system flow rates in a controlled manner can also eliminate check valve slams, with the added benefit of requiring significantly less energy than starting a motor with a contactor.
Modern VFDs can be instrumental in preventing dry-running pumps and damage to mechanical seals and bearings. Advanced PID functionality can ramp a drive up to a preset frequency to pressurize the discharge header before transitioning to PID control, eliminating pressure fluctuations.
Some motors are installed in environments where temperature and humidity fluctuate. These conditions can cause condensation in the motor windings, and when moisture condenses inside the motor, corrosion and insulation degradation can occur. Both conditions lead to premature motor failure. VFDs can keep the motor warm, preventing issues resulting from condensation. When the motor is not operating, the drive applies a small direct current (DC) to the motor windings, heating the motor.
Worst-Case Scenarios
For some systems, a VFD will ride through a brief power loss, drawing DC bus voltage down but not tripping or faulting the drive. In other scenarios, where power is lost for a longer period of time or the load is higher, a VFD can quickly restart a coasting motor once power is restored. On power loss, a typical centrifugal pump could coast for a long time, as the pump and motor are designed to have low friction. When power is restored, a VFD can use a frequency search function to determine the speed of the motor shaft and smoothly regain control of the motor. Using this functionality can prevent wide, rapid variations in pressure when the motor is restarted after a power loss.
VFDs can also be configured to recover from some faults automatically. For instance, if a drive is controlled via an Ethernet network, it will fault and discontinue operation until the network is restored and the drive is reset. Some VFD manufacturers allow for drives to be configured to auto restart. So, in the above scenario, after a configurable period has elapsed, the drive will attempt to restart. If the network has been restored, the drive will resume operation automatically. Other drive faults can be automatically recovered from in the same way, restoring operation while recording the issue for future evaluation.
Many pumping systems are operating at less than their potential. VFDs can do more than just turn the motor and pump shafts. Users can improve their operations by leveraging the sensing technologies built into their VFDs. The role that VFDs play in preventive, corrective and predictive maintenance makes them an essential component in pumping systems.