Size matters when it comes to pumping infrastructure. Larger pumps are more powerful than smaller pumps, but they’re also more expensive. A pump’s footprint brings added costs to the shop floor or to the offshore platform. Whether it’s a refinery, a chemical plant or a power plant, the footprint and ergonomic design of pumping infrastructure plays a key role in the efficiency of the plant. When it comes to metering pumps, the quest to make smaller and lighter pumps that do not compromise performance has previously been constrained by the size of the diaphragm, which dictates the size of the liquid end and the stainless steel surrounding the pump’s head. Today, new enhancements with polytetrafluoroethylene (PTFE) diaphragm designs are producing smaller, lighter and less expensive metering pumps that offer greater efficiency without compromising performance.

The Role of the Metering Pump
Metering pumps are positive displacement chemical dosing devices that deliver measured volumes of chemicals. In chemical or petrochemical plants, metering pumps are used to dose specific volumes of chemicals (under certain temperatures and at specific pressures) to make products. In offshore environments, metering pumps deliver flow assurance chemicals that prevent hydrates from forming and ensure the smooth flow of oil through long subsea tiebacks. In midstream applications, metering pumps dose chemicals that dehydrate gas or treat heavy crude to make it easier to move through pipelines. In power plants or refineries, metering pumps inject corrosion inhibitors and anti-scaling chemicals to protect pumping and piping infrastructure. For each of these applications, the accuracy of the metering pump is paramount, because over-injecting treatment chemicals in one part of the process can result in additional costs to eliminate those chemicals further along in the process.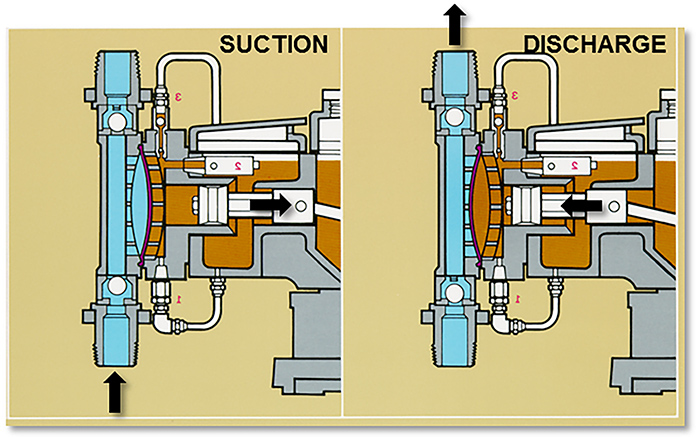
How Metering Pumps Work
Chemicals enter a pump’s wetted chamber when the motor drives a piston to create a vacuum that sucks chemicals into the liquid end from external tanks. Alternating piston strokes create pressure that closes the inlet valve, opens the outlet valve and forces the liquids out to the process. Within the liquid end is a diaphragm, which acts as a barrier between the piston and the process fluid (see Figure 1). The piston’s pumping motion is applied to hydraulic fluid, which causes the diaphragm to flex back and forth as the piston reciprocates. The movement of the piston, which is called deflection, flexes the diaphragm between concave and convex positions. The periphery of the diaphragm is clamped and does not move during the deflection. The greater the deflection of the diaphragm, the higher the flow rate. For processes that require high flow rates, pump manufacturers have always had to build large diaphragms, with large liquid ends and large housing areas, to deliver the volume and pressure required. As expected, this results in large and heavy pumps. Metering pumps must be able to deliver a wide range of harsh and corrosive chemicals at different concentrations and temperature levels. To accommodate this diversity, all the wetted parts of the pumps’ liquid ends should feature materials that are compatible with those chemicals. The pump should be equipped with a diaphragm—either metallic or plastic—whose material plays a key role in the equipment cost and weight.PTFE vs. Metallic Diaphragms
- Flow: PTFE allows for a smaller diaphragm diameter thanks to a higher deflection.
- Chemical compatibility: PTFE has a larger chemical compatibility than most metals due to its naturally high resistance to chemical corrosion.
- Pressure: Without the slippery properties of the PTFE material, metallic diaphragms can easily be clamped to withstand piston pressures up to 20,000 pounds per square inch (psi) and above, whereas reaching high pressure levels with PTFE diaphragms is said to be the biggest technical challenge for metering pump manufacturers.
- Temperature: Metallic diaphragms can withstand higher temperatures than PTFE without compromising accuracy. Temperatures in excess of 150 C negatively impact PTFE/plastic. On some occasions, the diaphragm could soften, impacting the degree of deflection and the resulting accuracy. API675 requirements stipulate that metering pumps must be able to inject chemicals with +/- 1 percent accuracy. So to be considered a viable alternative for offshore applications, pumps with PTFE diaphragms needed to overcome this limitation.
PTFE Diaphragms Deliver Smaller, Lighter & More Efficient Pumps
PTFE has one of the lowest coefficients of friction for any solid. Almost nothing sticks to PTFE, and the material is essentially impervious to corrosive chemicals. PTFE allows far greater deflection than a metallic diaphragm, enabling higher flow rates in a much lighter package. A smaller diaphragm enables pump manufacturers to design smaller liquid ends, which leads to smaller and lighter pumps that can still produce high flow rates. PTFE liquid ends can be 50 percent less expensive than metallic liquid ends. The primary limitation associated with PTFE diaphragms is high pressure. When pressure is amplified, the motion of the piston pushing aggressively on a frictionless surface could degrade the material density of the disk. A Catch-22 scenario had previously existed: clamping the round disk too tightly negatively impacted the density of the material, but not clamping it tight enough prevented it from withstanding the pressure required for certain applications.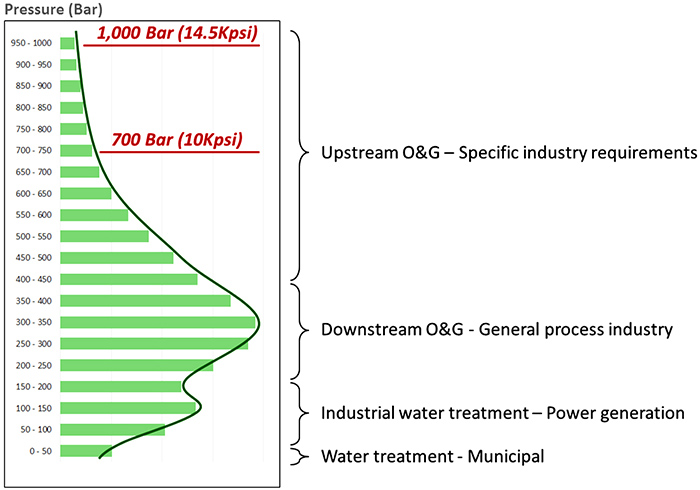