10/13/2014
Centrifugal pumps often experience repeat failures. Maintenance and reliability professionals are charged with preventing them. This four-part series explains the reasons behind repeat pump failures and uses a real-world field example involving boiler feedwater (BFW) pumps. In last month’s column, I recommended best practices for pump rebuilding, lubricant selection, and coupling and seal maintenance. This last installment discusses bearings and pump reliability, focusing on additional equipment features. I will cover details such as sleeve bearing design, bearing cage materials and maintenance procedures.
Details Are Important
In the final analysis, understanding and working on details will eliminate repeat problems with centrifugal pumps. In the example that has been covered in this series, the team working on the system recognized that the braided packing installed at several of this facility’s 1950s vintage BFW pumps also provided shaft stabilizing. Eliminating the packing and replacing it with a mechanical seal could cause the first lateral critical speed to drop into the operating speed zone. Therefore, a suitable, high-performance polymer bushing had to be installed in the throat bushing space. This requirement explained why the refurbishing had to be entrusted to an experienced pump rebuilder. The facility was asked to determine if the babbitted sleeve bearings listed in the plant’s spare parts catalog were made with the proper grade of babbitt. At least three different babbitt grades are used in fluid machinery. The grades vary greatly in load-carrying capacity. The babbitt must be bonded to a substrate without liftoff or delamination. The adequacy and conformance of the existing spares should be verified by ultrasonic examination.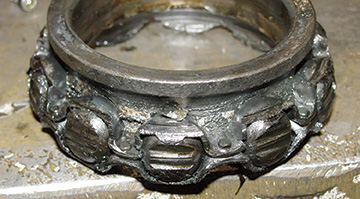
Sound Results
Because the analysis team wanted to be encouraging to the metal producer, the team assured the resident maintenance supervisors and reliability engineers that it had many positive findings. Most of what they were doing within the plant to maintain the equipment was good. Unlike the pump shown in Image 2, none of the metal producer’s seven BFW pumps required a radical redesign. However, plant personnel were asked to implement an electronic control strategy or an “operator alert” announcement system that ensured that each pump operated within 80 to 105 percent of its best efficiency point.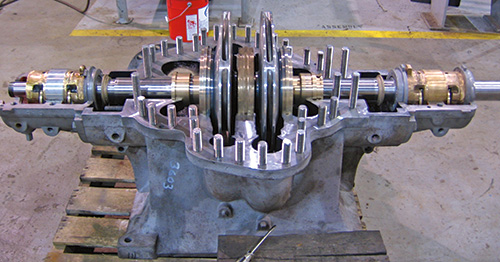