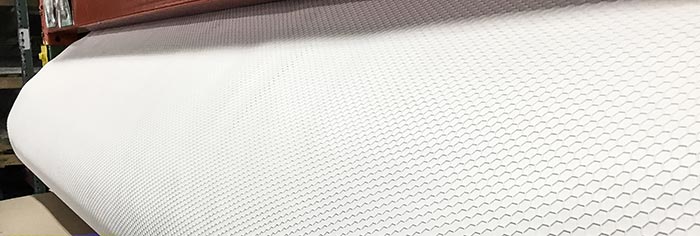
There are many aged and aging process plants in operation today. In fact, many of the processing plants for power, chemicals, oil, etc., have been in service for more than 50 years. And while the piping itself may remain intact, their bolted flange gasket joints and connections are becoming misaligned, corroded and damaged due to repeated handling, chemical exposure and thermal cycling. This can lead to costly ruptures that may result in millions of dollars in damages, downtime, noncompliance penalties, irreparable environmental impact and litigation. There is a solution that can extend the life of aging piping systems, preserving their functionality: raising the surface profile on polytetrafluoroethylene (PTFE) gaskets. This design modification can prevent leaks, spills and other releases in chemical processing plants by reducing and managing the contacted area of the gasket, thus achieving and maintaining a strong seal.
A Brief History of Gasket Technology
Traditionally, gasket thickness and sealability always involved a performance tradeoff. One could use 1/16-inch-thick (1.6 millimeter) gaskets when flanges were in good condition, achieving a tight seal with reduced creep. However, when the flanges had bad or misaligned surfaces, the seal integrity was degraded. In those instances when the flanges are in poor condition (or if the shape of the flange condition is unknown), one would choose a 1/8-inch-thick (3.2 mm) gasket. The reason? A user does not want to risk installing a thinner gasket and discover that it does not seal properly, which then requires a timely and costly uninstall and reinstall. However, the thicker gaskets do not seal as well as their 1/16-inch counterparts when placed under comparable load. Additionally, with the thicker gaskets, creep is higher, requiring re-torque. To address the limitations of both gasket options, the ideal gasket should combine the creep resistance of a 1/16-inch gasket with the compressibility and conformability of a 1/8-inch gasket—easier said than done. Historically, gaskets have not always been forgiving, easy to use or simple to remove. Yet technology has evolved, allowing sealing products to be engineered and designed to optimize the work that is put into them, delivering a tighter, more durable seal. The approach is one that does not focus on the gasket thickness but rather its surface profile. The results produce gaskets that reduce leaks, spills and other releases from piping systems, including those of aging chemical plants.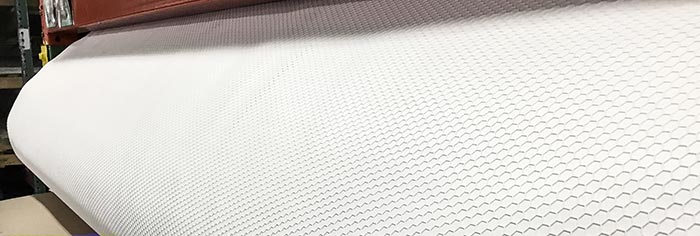
Raising the Gasket Profile
The concept of using surface profiling to reduce area and increase stress is found in many products, such as running shoes and car tires. Reducing the contact area while maintaining a given amount of compressive force results in increased stress. In the case of shoes or tires, this stress provides traction. In the case of gaskets, traction or friction between a gasket and a flange face is critical to holding internal pressure. If the downward force created by the fasteners in a flange is evenly spread over a larger area, the created stress contributes to making a seal more effective. This approach enables the aging piping system to maximize its sealing potential.Impact on Raising a Gasket Profile
Surface profiling positively impacts gasket technology in five key areas: compressibility, pressure resistance, scalability, load retention and dimensional flexibility.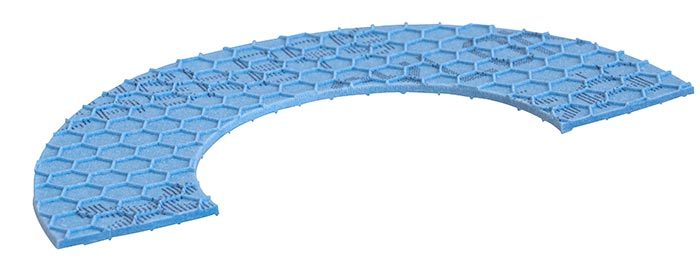
Compressibility
Compressibility is a critical functionality of gaskets, as it represents the ability of the gasket to conform to the surfaces that it seals. Adding raised features to the surface of a gasket directly impacts compressibility by reducing the contact area and increasing the resulting stress. When flange surfaces are worn, pitted or scratched—such as those in aging piping systems in chemical plants—it can be cost prohibitive and nearly impossible to repair/replace the flange to a “good as new” condition. The more compressible the gasket, the better chance of producing an effective seal with the flanges.Sealability
To create an effective seal, a gasket must perform two functions:- Conform to the flange face. This will help prevent the media from passing between itself and the flange faces. This is where compressibility becomes important.
- Resist or prevent permeation. On a microscopic level, most nonmetallic gasket materials have small voids or spaces. The key to preventing media from permeating through these voids or spaces is to close them off through the use of compressive force. This can sometimes be difficult if a gasket is extremely hard, or the surface area of the flanges is relatively large. The use of surface profiling or raised features can be beneficial as the force is concentrated, generating higher densification (improved gasket consolidation), which results in improved permeation resistance. This concentration of the compressive force is exerted at the point where the raised features contact the sealing surfaces/flanges. This results in higher surface stresses and, ultimately, more efficient sealing.