Q. Can rotary type pumps be used to pump slurries? If so, should users be aware of any special precautions? A. Rotary pumps may be used to transfer slurries when the application dictates. Hard-particle slurries can cause abrasive wear to efficiency-critical components in rotary pumps, which reduces volumetric and mechanical efficiency. Users must carefully select and apply rotary-type pumps in slurry service. The concentration of solids usually has the greatest effect on fluid characteristics of the mixture. A fluid containing only a trace to 3 percent by weight of fine sand content in crude oil, for example, would not be considered a slurry. A range of 5 to 15 percent by weight slurry of paper stock, however, goes through three stages of fluidity or shear characteristics, while high concentrations of finer solids can change watery carrier liquid to viscous—even thixotropic—fluid. The size and shape of the solids in a slurry normally determine whether a particular rotary pump configuration and/or cavity, or chamber size, can be used for the slurry in question. Typically, the cavity must be greater than particle size. In some pumps, the rotor configuration will accept larger particles as long as the size, distribution and shape are controlled. The size must be related to porting, rotor cavity size, configuration and interaction, and operating clearance. The hardness of solids greatly influences the wear rate of the rotary pump because of close relative motion of surfaces at the rotor tip or flank. The range of hardness is from soft solids, such as polymer chains of lubricating quality, to fibrous products that are usually soft but may carry hard particles, to very hard, irregular particles such as sand and carbon. Carbon is primarily soft, but the aggregate carries lumps with hardness approaching that of silicon carbide. A qualitative scale listing the hardness of several materials is often useful to compare solids and select pump materials (see Figure 3.3.16.1.4).
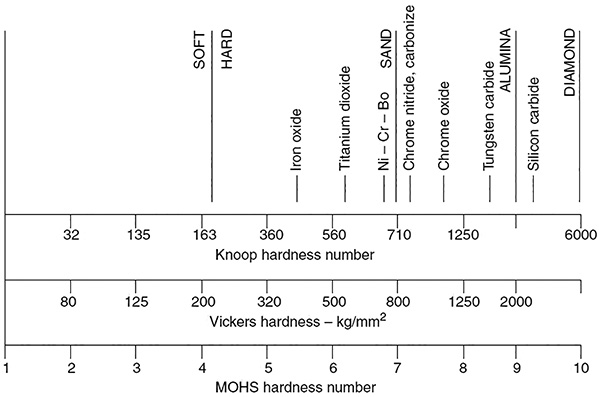