What are the recommended valves in a pumping system?
A pumping system typically requires three valves: an inlet (suction) shut-off valve, an outlet (discharge) shut-off valve, and a check valve between the pump discharge nozzle and the discharge shut-off valve to avoid reverse flow and protect the pump from backpressure.
Occasionally, a foot valve can be installed on the inlet pipe to maintain pump prime or to protect it from reverse rotation. However, potential drawbacks to foot valves such as impacts to net positive suction head available (NPSHa) and risk of water hammer (a pressure surge caused by an abrupt change in the pump rate of flow) must be considered.
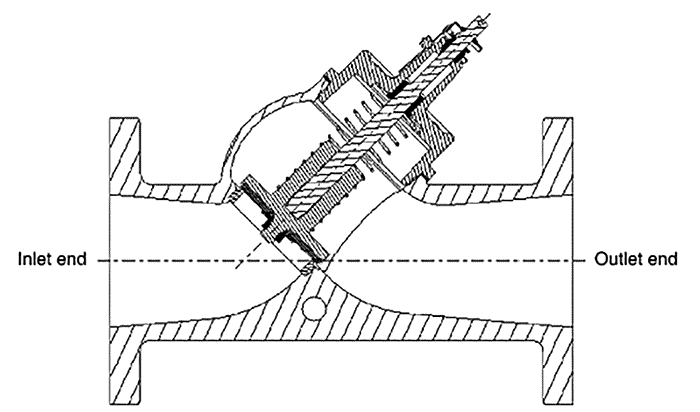
Note that some systems will not require these valves, and some will require additional valves for isolation and control. Specification and application for these valves and control valves can be referenced in ANSI/HI 9.6.6 Rotodynamic Pumps for Pump Piping, and HI’s “Pump System Optimization: A Guide for Improved Energy Efficiency, Reliability, and Profitability.”
Sometimes, the discharge isolation valve and the check valve can be replaced by a triple-duty valve, which provides both isolation and back flow prevention in one piece. They can also provide circuit balance.
The initial installment of triple-duty valves is typically less expensive than the initial installment of separate valves.
However, triple-duty valves may exhibit higher head loss, which could lead to higher life cycle costs. Refer to HI’s “Pump Life Cycle Costs: A Guide to LCC Analysis for Pumping Systems” for information on how to calculate the life cycle cost of a pumping system.
Read more HI Pump FAQs by clicking here.