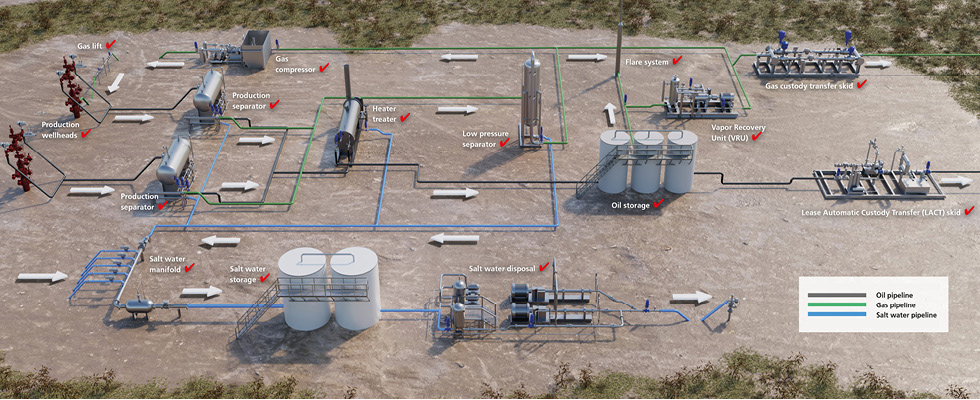
Methane is a greenhouse gas that traps heat in the atmosphere and is the second most prevalent human-made greenhouse gas behind carbon dioxide (CO2). Because methane is more than 28 times as potent as CO2 at trapping heat in the atmosphere over a 100-year period, it has become more critical for governments and businesses worldwide to minimize total methane emissions from industrial processes.
The oil and gas sector emits around 80 metric tons (Mt) of methane yearly, accounting for roughly 40% of total human-caused methane emissions. These emissions may be reduced by over 75% by implementing leak detection and repair programs and upgrading leaky equipment. Methane abatement in oil and gas is highly cost-effective to do. Approximately 40% of methane emissions may be eliminated at no net cost. The automation of upstream oil and gas operations helps reduce emissions while providing enhanced control, decreased power usage, high dependability and ease of field servicing. The installation of electric actuators is an effective way to reduce upstream methane emissions.
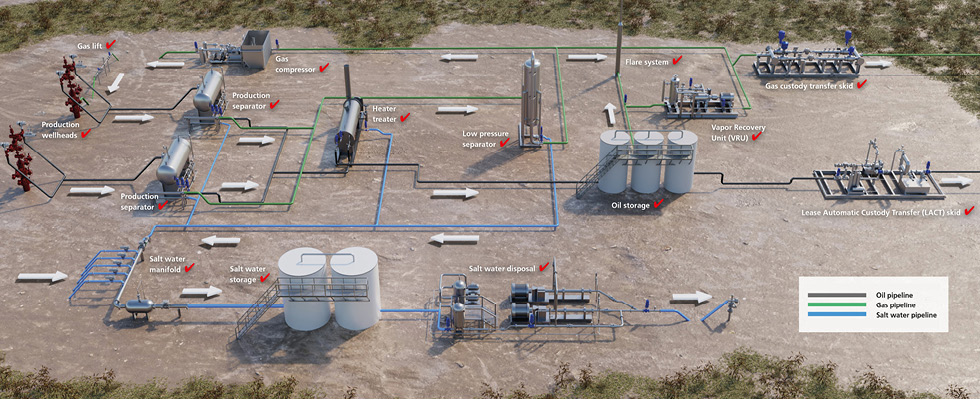
Electric Actuators vs. Pneumatic Actuators
In upstream production, control valves have historically been operated by pneumatic diaphragm actuators that use the well-stream gas as their motive power, releasing methane every time the valve is stroked. However, electric actuators do not vent during operation.
Electric actuators can require lower maintenance than pneumatic actuators and control instruments. Using self-contained electric actuators instead of pneumatic solutions with multiple parts and systems can result in cost savings and increased operational efficiency.
Electric actuator technologies can offer advantages over pneumatic ones. Pneumatic actuators have multiple parts that can be affected by air quality fluctuations, temperature variations and other environmental factors.
On the other hand, electric actuators are less susceptible to such influences. They are more energy efficient, as they only consume electricity when in operation. In contrast, pneumatic actuators and controls require a constant supply of either motive pipeline gas or locally produced compressed air. The specific benefits of electric actuation can be seen in various sectors of the oil and gas industry.
Production trees
The production tree (or Christmas tree) is an assembly of valves, spools and fittings that regulate the flow of oil or gas from a well. In the event of overpressure, a surface safety valve (SSV) is a fail-safe/shutdown valve installed at the upper wellbore for emergency shutdown to protect the production tunings. A production choke valve controls the flow of well fluids being produced and regulates the downstream pressure in the flowlines.
Production processing
Pneumatic diaphragm actuators have traditionally operated control valves in the upstream production process. These actuators primarily use well-stream process gas to power the valve, releasing methane every time the valve is stroked. Many operators have started using compressed air instead of well-stream process gas to reduce methane emissions. They achieve this by deploying air compressor units at production sites.
Gas metering and LACT skids
Natural gas production metering and Lease Automatic Custody Transfer (LACT) for oil production metering are two crucial aspects that connect upstream operations to midstream gathering infrastructure. The pipelines and valves used in midstream operations are usually larger and require higher torque/thrust ranges for valve actuation than those used in upstream production processing infrastructure.
Multiple flow control systems operate together on a custody transfer metering skid to ensure low measurement uncertainty and high metering accuracy. The flow control on metering skids must be highly accurate and reliable and always provide safe valve operation. To automate large control valves with high-pressure ratings, a high-output actuator can deliver increased linear thrust and stroke length.
Gas lift system
When extracting oil from underground wells, a gas lift system is used to lift the fluids to the surface. This system works by injecting high-pressure gas into the well to reduce the density of the fluids and create a “scrubbing” effect that lowers the pressure at the bottom of the well, allowing the fluids to flow more easily.
A reliable and adequate supply of high-quality lift gas is required for the gas lift system to work correctly. A control valve modulates the flow and pressure of the gas being injected into the well.
Saltwater disposal systems
Produced water is the largest liquid produced in the oil and gas industry. The water from the well can be four to five times the volume of produced gas or oil from the same well. This water is then transported to recycling tanks or saltwater disposal wells through an intricate gathering line network.
Reliable and advanced automation solutions can help operators reduce emissions, improve process efficiencies and increase production output. Electrification of valve actuation will aid in reducing emissions from oil and gas operations. Selecting smart, low-power solutions that are perfectly suited for upstream oil and gas processes will help operators achieve emission reduction goals.
References
epa.gov/ghgemissions/overview-greenhouse-gases
iea.org/reports/global-methane-tracker-2023