How Gulf Coast service providers managed the aftermath.
Flowserve
07/04/2018
Oil refineries stand to lose millions of dollars each day when a shutdown occurs. That is why refineries adhere to strict equipment inspection and preventive maintenance schedules and do everything possible to minimize equipment downtime and keep operations running smoothly. In short, they have learned to anticipate and plan for the unexpected events. But what if the unexpected turns out to be a Category 4 hurricane barreling toward the oil refinery at 130 miles per hour? That is what Gulf Coast region residents and businesses experienced in 2017 when Hurricane Harvey made landfall along the Texas coast.
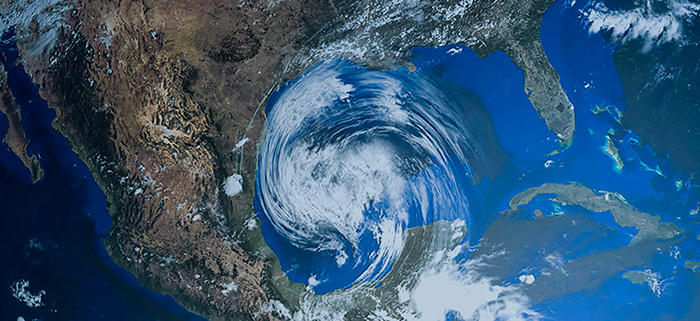
Getting Refinery Equipment Back Online
Anticipating that many Gulf Coast refinery customers would need urgent equipment, spare parts and field service support, service engineers and equipment were rerouted from a vast network of quick response centers in North America to the Gulf Coast facilities to support the recovery efforts. Having these experienced service teams at the ready meant they could be at sites to evaluate equipment repair needs as soon as possible. Field service personnel worked with refineries to evaluate the level of damage to equipment and determine what repairs and replacement parts were needed. For some refineries, getting their pumps back online required flushing the units’ bearing housings or filling them with new oil. But some equipment needed to be pulled from the refinery and sent out for repair. The extent of the repairs varied. One facility in Deer Park, Texas, lost the nitrogen system to all of its mechanical seals. The facility sent four pumps for repair and ordered four new valves to replace those they could not salvage. A facility in Cedar Bayou, Texas, which had not yet begun operating before the storm, had to pull all of its pumps, valves, motors and positioners for repair or replacement. Twenty-two valve associates and 10 field service personnel were on-site to help with equipment repair and replacement. The refinery’s service team inspected 34 pumps and sent 25 pumps to the Gulf Coast quick response center for repair. Another refinery in Sweeney, Texas, flushed 30 of its pumps to get them back into service but had to send five pumps, four seals and an automated valve for repair. A company with refineries in Beaumont and Baytown, Texas, sent four pumps, 10 valves and 30 seals for repair. That facility also had to replace seven valves. In total, more than 100 pumps, 50 motors and 60 seals were repaired by one service company, and 173 new motors and 250 positioners were purchased and installed. Because additional service engineers had been staffed by rapidly mobilizing them to the disaster area, the team was able to assess the damages, repair, deliver, reinstall and commission these pumps, seals and valves quickly, sometimes in a matter of days, while still using genuine original equipment manufacturer (OEM) parts.Preparing for Future Disasters
While it might not be possible for refineries to completely protect their facilities from a natural disaster, there are specific steps they can take to protect equipment and be better prepared in the event of an outage. Refineries should have service agreements with a reliable service partner who not only has the capabilities to support them on a day-to-day basis but can also scale up quickly in the event of a large-scale equipment outage. By having a service agreement in place, a refinery will not have to scramble to find a service partner and negotiate terms and conditions after a disaster strikes. Another important aspect in preparing for the unknown is for refineries to stock the recommended critical OEM parts with their service partner. Some pumps require engineered parts, which OEMs manufacture as needed. Should a refinery need to replace several of these components, it could take weeks or longer before their equipment is back online. However, users can order these parts ahead of time and store them with their service partner. By keeping engineered parts stocked on-site, their service partner can get their equipment up and running quickly in the event of an outage.Restoring Production to Normal
Hurricane Harvey packed a powerful punch, knocking out more than 20 percent of U.S. refining capacity. A few weeks after the hurricane struck the Gulf Coast, 15 of the 20 affected refineries were back to or near normal operating rates. The remaining facilities would restart operations within one month. This faster-than-expected recovery was a result of the extensive preparedness of the Gulf Coast refineries as well as the experienced service professionals who worked tirelessly to repair essential equipment and help customers weather the major storm.References
- CNN Money. “Texas oil refineries still badly hurting from Harvey.” [http://money.cnn.com/2017/09/11/investing/harvey-refinery-texas-gulf-coast/index.html]