On January 4, 2011, President Barack Obama signed the Food and Drug Administration (FDA) Food Safety Modernization Act (FSMA), a reform designed to encourage proactive prevention rather than reactive response to food contamination. While there are many companies within the mature air operated double diaphragm (AODD) market, very few offer product lines that conform to the strict regulatory guidelines of the FDA. To manufacture pumps used in this industry, companies must devote the necessary resources to education as well as research and development. This process starts in the engineering department where the correct materials are specified and dimensional drawings are created. Quality assurance evaluates the parts, ensuring correct surface finish, dimensions and materials requirements have been implemented. The FDA does not certify pumping equipment. In the case of AODD pumps, materials and processes that comply with FDA standards include:
- Water chambers, manifolds and outer diaphragm places are made from CF8M (Cast 316) stainless steel that has been electropolished per ASTM B912.
- Valve seats are made from 316 stainless steel, virgin PTFE, Hytrel 4069 or Santoprene 273-40.
- Valve seat O-rings are made from virgin PTFE.
- Diaphragms and balls are made from virgin PTFE, Hytrel 4069 or Santoprene 273-40.
- Center sections, air chambers and air valves are made from nickel plated aluminum or polypropylene.
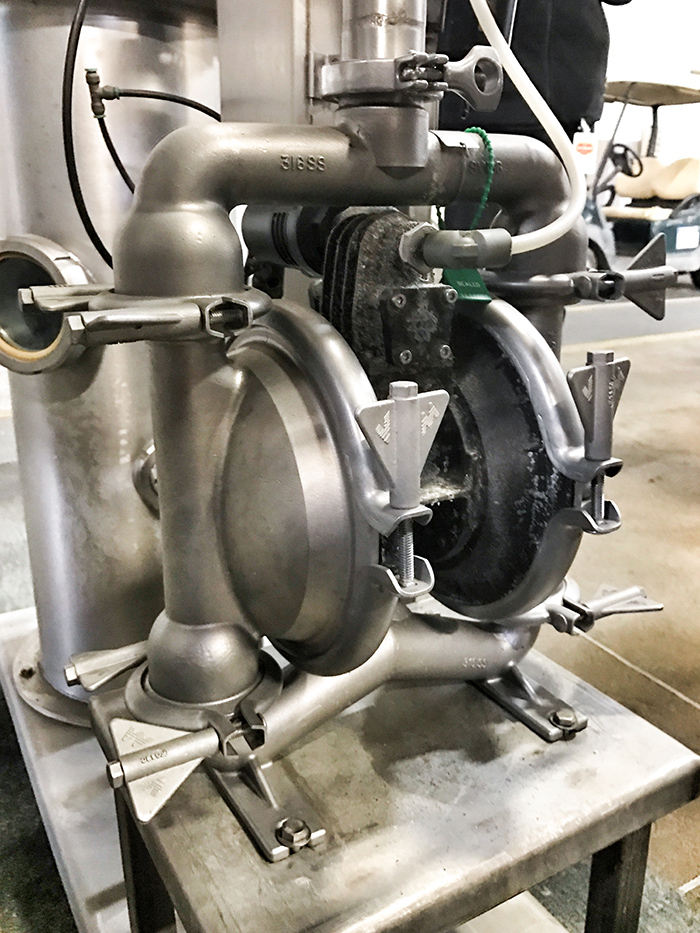