These critical aspects must be addressed to protect the environment.
Sundyne
03/14/2019
The idiom “take it with a grain of salt” implies not to take something seriously—but in the chemical processing world, salt is a serious ingredient. Almost half of the world’s chemicals depend on chlor-alkali products, which come from salt. Chlor-alkali processes introduce current into an aqueous/salt brine to produce chlorine and caustic soda (sodium hydroxide). Three methods exist for this process: membrane cell (81 percent of global production); diaphragm cell (14 percent); and mercury cell (5 percent of global production, mostly in Europe). Each method produces the following base chemicals:
- Chlorine is used to make bleach and more than 15,000 commercially traded compounds. Major markets such as plastics and pharmaceuticals require chlorine for their manufacturing process, even though chlorine does not end up in their finished products. Chlorine is a major component in the vinyl chain, which is tied to the construction industry and makes up about 30 percent of global demand for chlorine. Chlorine is the most widely used chemical in the world.
- Caustic soda (sodium hydroxide) is a basic ingredient for paper, textiles, detergents and most forms of industrial and municipal water treatment. The end-use markets for caustic soda are more numerous than those for chlorine, and in many applications caustic is valued more for its neutralizing power as a strong base and an absorbent. One of the top global markets for caustic is aluminum production. Other significant markets include pulp and paper, and production of organic and inorganic chemicals driven by the manufacturing sector. Caustic soda is the third-most popular chemical used throughout the world.
- Worker safety and environmental protection by eliminating emissions and leakage
- Reliability via superior chemical resistance
- Simple maintenance
- Energy efficiency
Safety & Environmental Issues
Chlorine is a reactive element and a strong oxidizing agent. It is toxic and corrosive, irritating eyes, skin and respiratory systems. Chlorine cannot be inhaled by plant personnel. It is harmful to the body’s moist tissue, particularly the lungs, even at low concentrations. The transportation of chlorine (via rail or pipeline) is dangerous and is highly regulated. Depending on the concentration, caustic soda can be corrosive, irritating and potentially fatal to plant employees (if high quantities come in direct contact with the skin or mouth). As a result, industrial manufacturers of this chemical use closed systems to prevent direct contact with plant employees. The wastewater from chlor-alkali production causes environmental problems.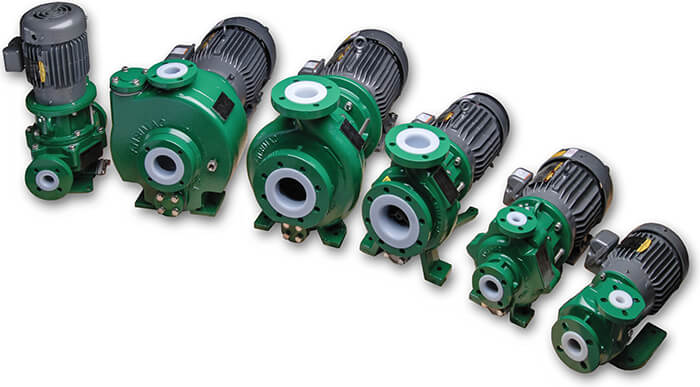
Reliability via Chemical Resistance
To lower the total cost of ownership for plant equipment, construction materials are key in pump selection. The harsh nature of chlor-alkali production can wreak havoc on infrastructure. Some chemicals used as catalysts (such as sulfuric acid to dry moist chlorine gas) add further demands on pump linings and render expensive alloys such as titanium or palladium/nickel unusable. Characteristics for the pumps used to handle aggressive chlor-alkali chemicals should include:- EFTE-linings, which provide resistance to chemical attack and can safely handle a wide range of corrosives and solvents up to 250 F (121 C) without corrosion
- a fully encapsulated inner drive, which hermetically seals the inner magnets and isolates them from process fluid, preserving the integrity of the magnets
- a Kevlar-fiber reinforced vinyl ester containment shell, which enables a burst pressure of 6X MAWP of the pump, delivering unprecedented reliability
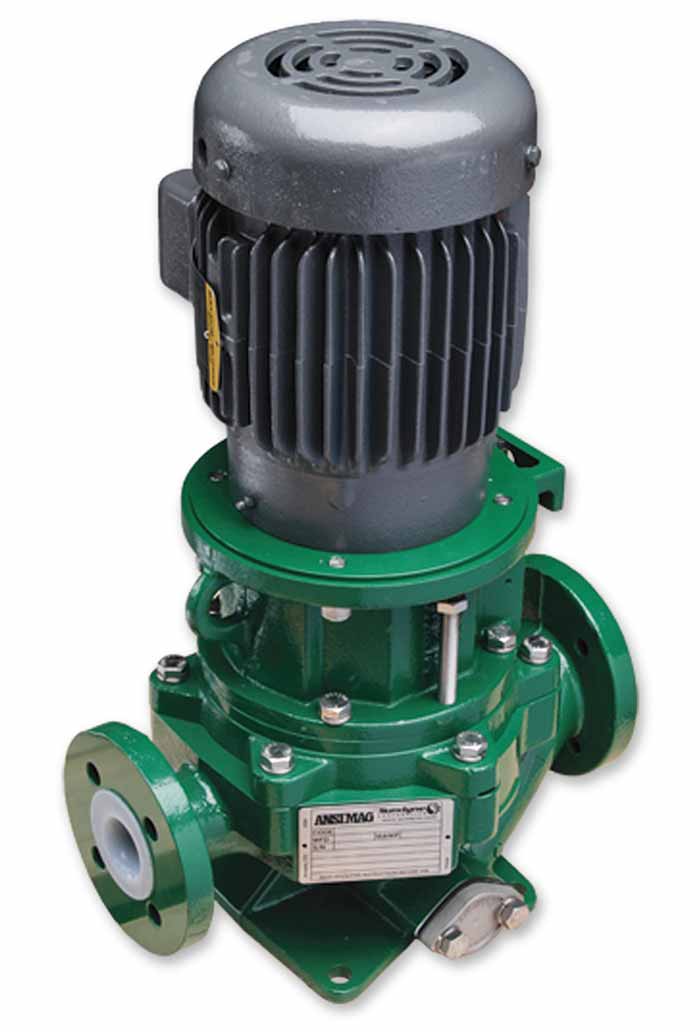
Lowering Total Costs with Streamlined Maintenance
The sheer volume of chlor-alkali products produced speaks to the need for reliable equipment that minimizes plant downtime, as many plants producing these chemicals run operations around the clock. The ability to streamline maintenance (and plan predictive maintenance activities) helps operators increase plant uptime. Sealless pumps consisting of fewer wetted parts can be repaired on the shop floor. This enables maintenance that can be performed without the need for special tools or training. Other pump features, such as a single piece replaceable impeller, provides a cost-effective approach to spare parts management and makes it easy to swap out an impeller as process conditions change. When it comes to chlor-alkali production, a feature called an axial thrust washer provides a positive thrust surface that is unaffected by cavitation or transient suction conditions. This increases the allowable operating range of the pump and improves reliability, compared to pumps with thrust-balanced methods.The Need for Efficiency
Electrolysis and chlor-alkali production are energy-intensive processes. Electricity can account for 40 to 50 percent of operating costs. In many cases, the ability to manage this expense determines the plant’s profitability. Sealless pumps can be energy efficient and plants producing chlor-alkali may want to seek sealless pumps with an efficient hydraulic envelop and low net positive suction head (NPSH) hydraulics. Small footprints are always preferred, to not only save space on the shop floor, but also to facilitate simple access for maintenance. And simple pump technology, such as a rear casing, can bolster efficiency by eliminating eddy currents and preventing hysteresis losses during operation. This type of functionality eliminates heat generation and reduces energy costs.Conclusion
Chlorine and caustic soda are basic ingredients that touch lives every day. These building blocks are pervasive in almost every industry, including pharmaceuticals, textiles, construction, cosmetics, and industrial and municipal water treatment. The world needs chlor-alkali—and the thousands of plants around the globe that manufacture chlor-alkali and its related products need pumping infrastructure that can address the key issues of safety and environmental protection. In addition, it must be resistant to harsh chemicals, have a streamlined maintenance program and be energy efficient.In North America, almost 500 different plants manufacture chlor-alkali, and more than 4,000 additional plants use these foundational chemicals in their manufacturing processes.
Chlorine is used to make:- bleach
- solvents
- resins
- PVC
- polymers
- cleaning products
- electronics
- printed circuit boards
- dyes
- cosmetics
- pesticides
- coatings
- adhesives
- aluminum
- pulp and paper
- soaps
- detergents
- cleaners
- textiles
- oil refining
- bio-diesel
- water treatment (industrial and potable)
- thousands of other chemicals
- brine preparation
- liquefaction
- evaporation
- cooling
- drying
- compression
- storage and loading