
Reliable mine dewatering is critical for effective and safe surface mining. It creates better working conditions, improved geotechnical stability and greater efficiency for the mining operations.
Dewatering was needed at a mining complex in the Midwestern part of the United States.
The complex contained 1.3 billion tons of clean, recoverable coal reserves. Unfortunately, there were several ponds and other materials overlying the mineral deposit.
A local mining company—one of the largest underground coal mining companies in the U.S.—began working with an area distributor to procure the use of pumps in order to dewater the multiple existing ponds on the property and then refill new ponds being dug on the property. This process needed to continue from pond to pond throughout the entire expanse of the complex, as the water was being used to supply the entire mining operation.
Unfortunately, this required high-head, high-volume dewatering pumps, and the pumps provided by the local company for the operation did not have this capacity. The pumps were failing, likely due to the high volume of water.
Using these lower-head pumps meant crews were spending a lot of unnecessary time trying to move the water, which was slowing down the entire operation.
The mining company knew it needed pumps capable of handling the high-head, high-volume dewatering needed, so the project managers called Jared Stratton, rental manager at Service Pump & Supply Inc.
Stratton knew that to handle the project’s demand, he needed heavy-duty, portable bypass and dewatering pumps.
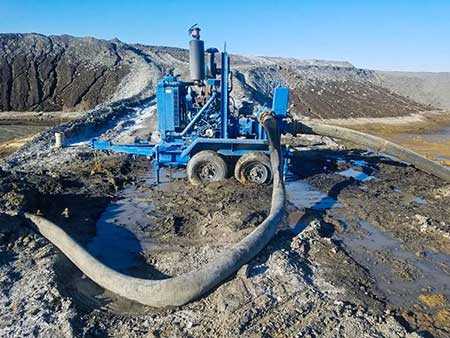
A Solution for Increasing Capacity
Stratton spoke with the project managers and immediately knew they needed pumps with increased volume capacity, especially as they were moving the water over distances of a half-mile up to a mile. Dewatering pumps available in the area could not meet the project needs and getting other pumps meant a greater expense and longer wait times—some needing electric turbines installed and running new wiring, floats, etc.
Stratton knew which pumps should be used for the different needs of the project. He brought in 12-inch pumps to move water from pond to pond, and 8-inch pumps to deliver water for the mining operation itself. The eco-friendly, dry-priming, electric-driven pump models provided large solids-handling capabilities.
In addition, the compressor-assisted priming system eliminated product blow-by and worked quickly.
The 8-inch pump has flows up to 3,200 gallons per minute (gpm), high heads up to 300 feet and handles solids up to 3 inches. The 12-inch pump has flows up to 5,200 gpm, high heads up to 350 feet and handles solids up to 3.38 inches.
Starting with two of each pump, water began flowing more efficiently and quickly. To increase capacity even more and cut down on the dewatering time, Stratton added more pumps for a total of five each, with the system running across the entire mining property.
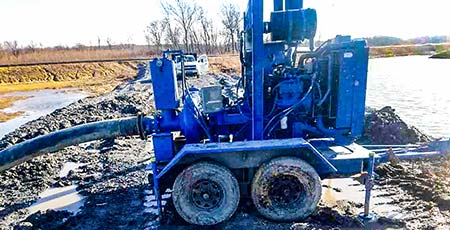
Results
The pump system remained on the property for two to three years while the surface mining project continued. The pumps’ ability to handle high-head, high-volume dewatering capacity, as well as low maintenance needs and automatic priming—which enables the pumps to run dry unattended—helped keep the project on track, on time and on budget.
“Without this pump system, the project would have run into numerous setbacks and unforeseen expenses,” said Stratton. “I’m glad we were able to get this job done thanks to these pumps.”
Due to the demand for minerals, surface mining continues across the country and the world. As projects begin and expand, dewatering continues to be a critical component of each. Investing in a reliable and cost-effective pump system, customized for each project, helps keep time and cost under control.