An electric submersible pump provided the plant additional fire suppression when a hot spot caused a silo’s wood chips to combust.
IRONCLAD Marketing
04/27/2017
When fires occur, especially in biomass energy facilities, a quick response is critical to keeping workers safe and minimizing damage to the plant. Plant managers must ensure that a wide range of dependable equipment is in place to take action—from spark-detection technology to fire-suppression systems. Because fires occur even with the best systems in place, having a backup plan is important.
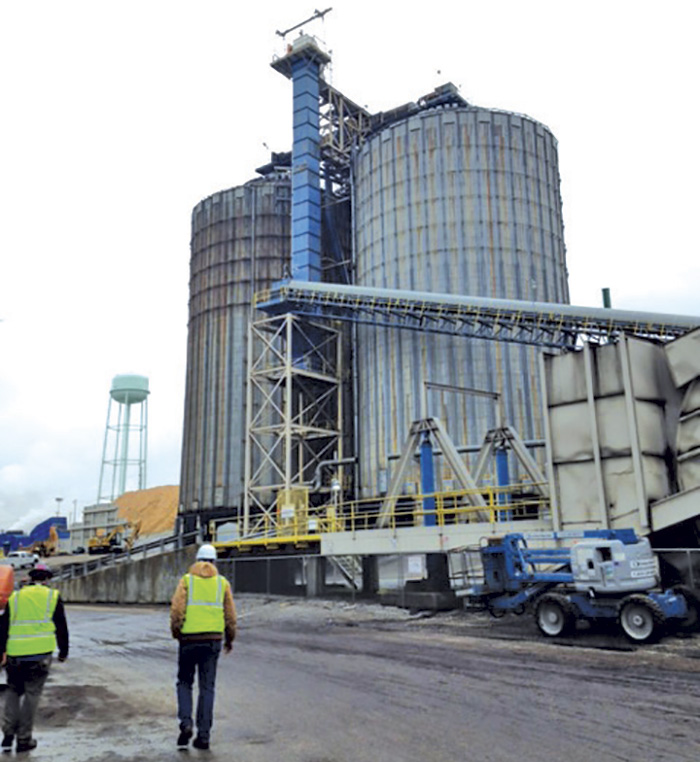
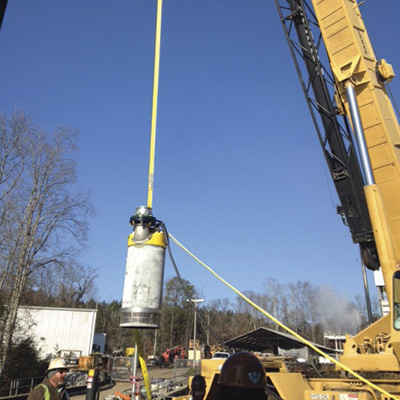
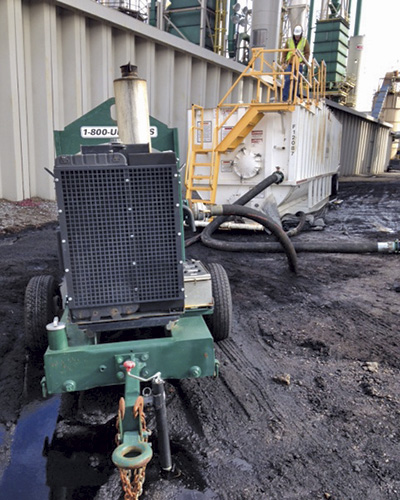
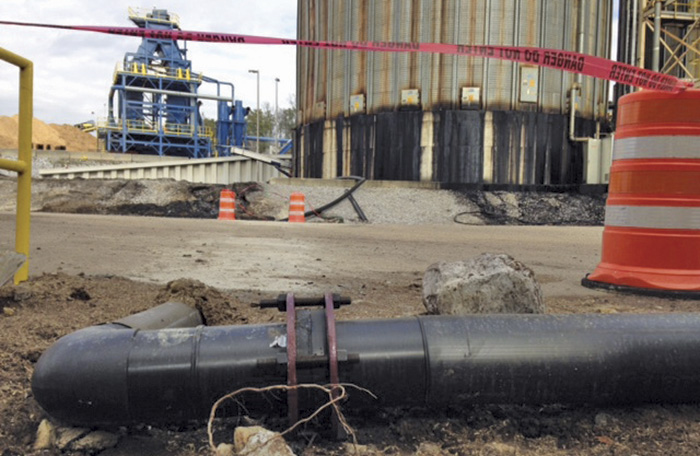