Coker units thermally crack the residual oil (or bottoms) from an oil refinery’s vacuum distillation tower into smaller, low molecular weight hydrocarbons that are further processed or sold. The excess or residual hydrocarbons from this process are heated and then sold as petroleum coke, which is usually a high economic margin product. Coking heater charge pumps transfer a continuous flow of process prior to the product stage, so any interruption would have a high economic impact on the unit margins and the refinery because other units will need to reduce the process to shift production. The coker charge pumps at an Indiana refinery had a history of repeated failures from the 1990s through the end of 2011. Two pumps were in service—a turbine-driven pump and an electric-motor-driven pump. The turbine-driven pump typically exhibited a longer time between repairs because it was used less often. The perception was that the turbine-driven pump also had a lower capacity threshold because it operated at a lower speed. These pumps normally have a pumping temperature of 560 F. They use an American Petroleum Institute (API) Plan 32 seal flush in which a lighter gas oil is used to cool the mechanical seals. These high-temperature, two-stage diffuser pumps had mean time between repairs ranging between six and 12 months and failure modes almost equally divided between seal leaks and thrust bearing overload. During every rebuild, the pump cases regularly exhibited heavy erosion at specific points inside—the suction eye to vane edge, the vane end to diffuser end and around the divider plate between stages.
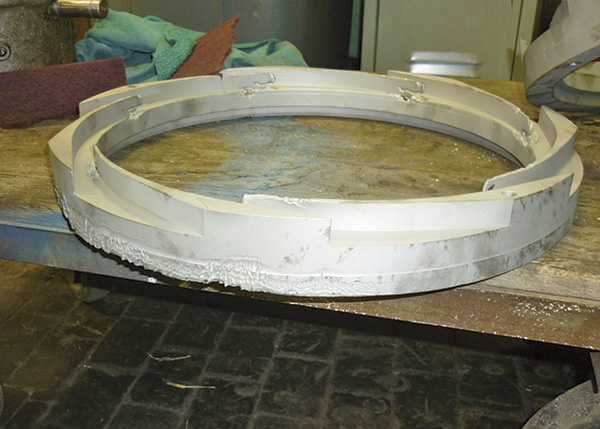
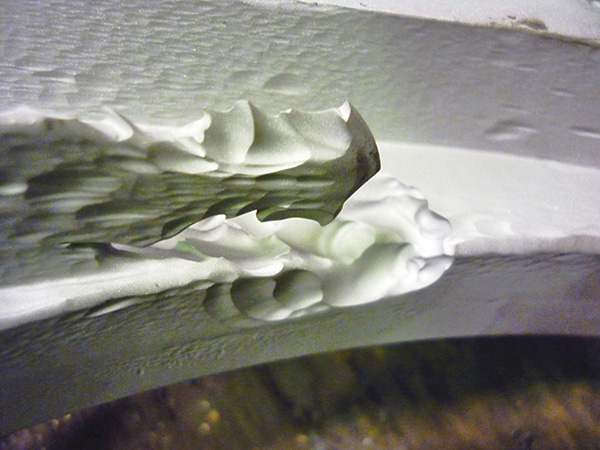
Findings
The team determined that the thrust issue was an inherent design problem and could not be addressed with field modifications. They also tackled the issues of erosion wear inside the case. They found discrepancies in pump operations and the actual design of the pump. It was determined that the flow meters used to measure pump throughput had a flow correction factor that required adjustment for temperature. Once this was completed, it was discovered that the pump had been operating at 25 percent above its best efficiency point (BEP) instead of the expected 4 percent. Rotating equipment experts determined that an operating point at this capacity coupled with the composition of the process and temperature would lead to the extensive abrasive wear that was found during every rebuild. The current geometry of the impeller and diffuser design coupled with the high-speed fluid and temperatures led to aggressive fluid directional changes that facilitated the abrasive wear.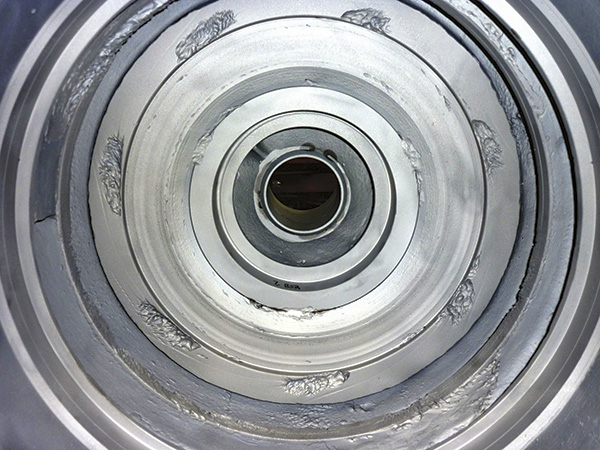
Action Plan
The team members implemented an action plan to mitigate the issues based on their findings. First, they addressed the thrust and erosion issues by procuring a new pump that would have a more balanced design. This new pump would also have a revised flow pattern design and coating of the internals with wear-resistant boron that would lessen the abrasion wear. This option, however, was not pursued immediately because the equipment would have a lead time of six months. As an immediate resolution, the team rebuilt the existing motor-driven pump with the following modifications. First, the internals were furnished with an ion-nitride hardening process, suggested by the parts manufacturer, which would help mitigate the expected erosion wear. In addition, the bearings and impellers were sized to match the original design condition. This would help mitigate any thrust concerns and help the pump operate within its expected performance. The team also implemented a weekly performance monitoring report in which the pump operating points were imposed against the pump curve to capture any gradual drop in performance and raise alarms to operations. This last recommendation proved helpful in determining the maintenance schedule and establishing a priority for the operational effectiveness on the coker unit. Additional lesser modifications included the seal flush piping, process warm-up lines, air cooled outer bearing and vibration monitoring.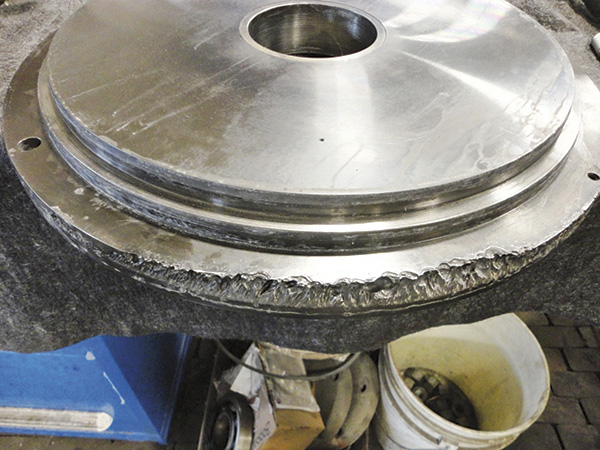