Considering the long history of electric motors powering the industrial world, it is no surprise when the need arises to replace a large induction motor. This article details what should be considered when attempting to replace an outdated or failed machine with a new induction motor. Many factors could lead to the replacement of a motor, including defects, a desire to operate at higher efficiencies or a demand to achieve higher power factors. Every case is different and specific to each operation. However, there are universal considerations that should be accounted for when upgrading a large induction motor. Frames within the National Electrical Manufacturers Association (NEMA) range of small to medium industrial motors are not complicated to replace due to the universal dimension standards. However, medium- or high-voltage motors do not have dimensional standardization. Additionally, unlike motors with power less than 500 horsepower (hp), large motors are not required to maintain comparable torque or current levels from manufacturer to manufacturer.
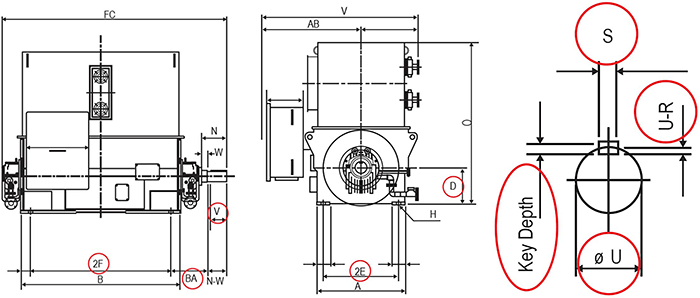
Mechanical Interchangeability
Images 1, 2 and 3 illustrate the dimensions that the replacing motor needs to match to be considered a “drop-in replacement motor.” The descriptions of each dimension in Table 1 explain their relevance. Included is a column to indicate the similar nomenclatures of the International Electrotechnical Commission (IEC) standard. Motor manufacturers must ensure the proposed replacement motor is capable of matching shaft dimensions, shaft height, the position of assembly holes and the BA dimension. All other dimensions may vary.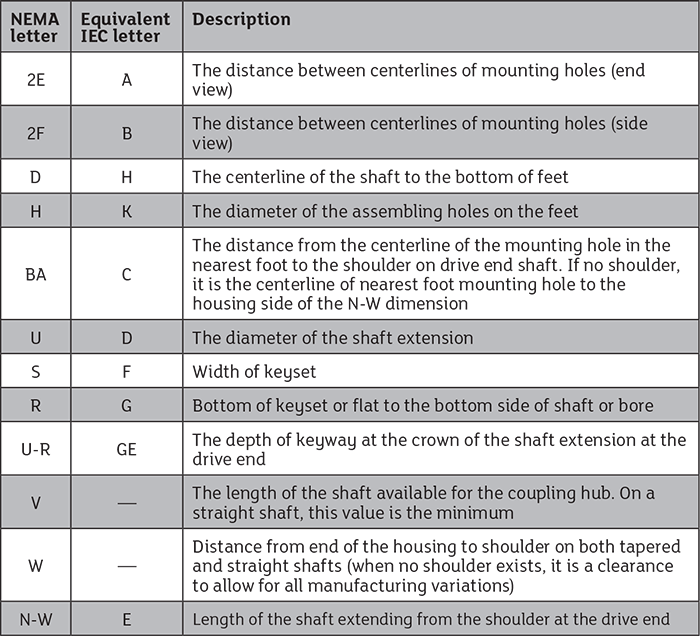
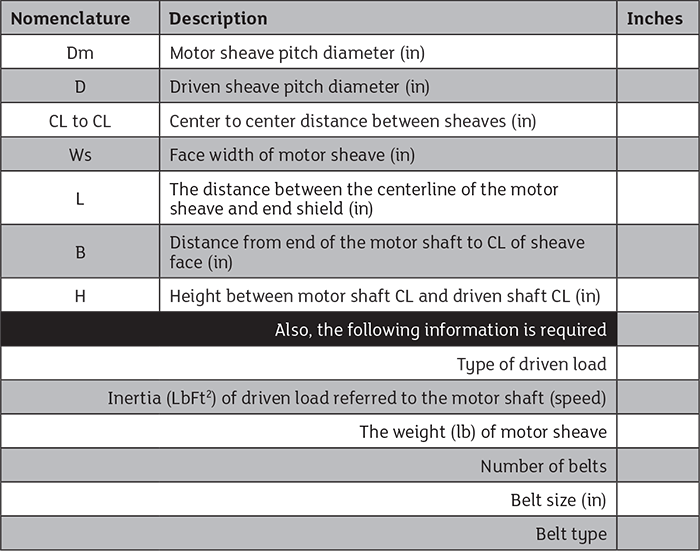
Coupling
Most motors couple directly to fans, compressors, pumps and other process machinery. In this case, the motor outline drawing will provide the necessary shaft dimensions. However, in applications where the motor couples through a sheave and belt or a tapered, hydraulic coupling, the motor manufacturer should request details exceeding the basic dimensions of the shaft to replicate a shaft end for a tapered hydraulic coupling. The motor owner can provide a drawing with these details. In most cases, due to radial forces applied to the shaft, belt-sheave couplings require a particular bearing, end shield and high-strength steel for the shaft. This is not included in standard products. Image 4 and Table 2 provide a checklist for belt and sheave data collection to consider before a quote request is sent to the application engineer.Accessories
Unless specifically requested, the end user can request the same model be provided to ensure the same controls and interfaces are used.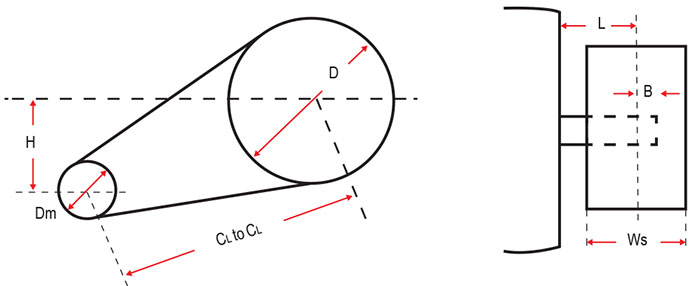