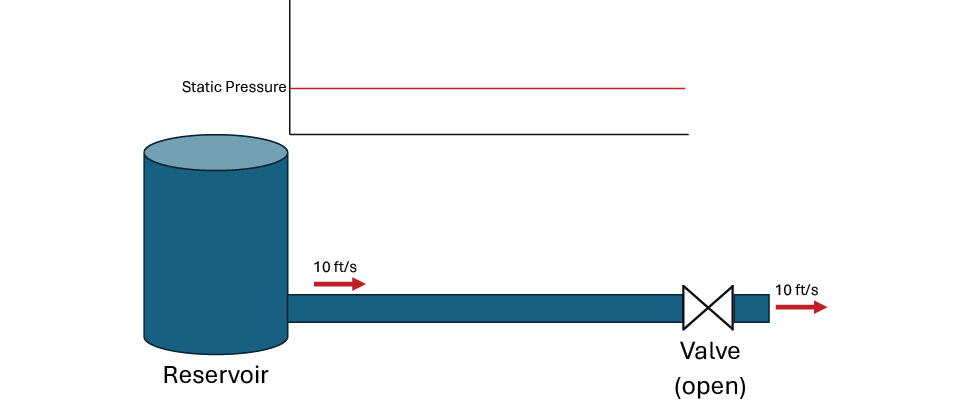
Several years ago, this author published an article titled “How Not to Use a Rubber Expansion Joint.” The article addressed common installation and application issues, but it did not discuss water hammer. That subject deserves a separate article due to the unique circumstances and extreme effects, which can exceed the design criteria of the system and individual components, including the expansion joints.
Once or twice each year I speak with a distressed engineer, and it is usually after a system startup. The conversations are very similar:
Engineer: When a pump starts (or stops, or a valve opens or closes), the pipes jump off the supports. It sounds like something is going to explode in the piping. I want to add an expansion joint to absorb the shock.
Author: Although I like solving problems and selling expansion joints, that would be a really bad idea.
Engineer: %@$#&!
This is an understandable reaction, because the problem manifests itself at the worst possible time. The construction team must turn the building over to the owner. Maybe the project is behind schedule. All construction and design issues have been resolved, the equipment is powered up, the switch is flipped and suddenly there is another problem and potential delay.
Adding an expansion joint to fix a hammering system is usually not a good idea, although it can help in some circumstances.
Transient Events: Water Hammer
Water hammer is one of four types of transients, or short-duration dynamic events, that can result in extensive damage to a piping system. The four types of transients are:
- Liquid
- Liquid and vapor
- Liquid and gas
- Gas
Elastomeric joints are almost exclusively installed in liquid systems, most often with water as the medium, so the focus of this article will be on water hammer.
Water hammer is an event caused by a sudden change of velocity of a moving column of water, resulting in a large pressure spike that travels through the pipe at a high velocity. Common causes can be a hard start or stop of a pump or a fast valve closure. The terms “sudden” and “fast” are relative, depending on the event duration and the total length of affected pipe.
For a demonstration of how high the pressures can rise, consider a simple arrangement of a reservoir, long pipe and valve. The valve is normally open, allowing water to flow from the reservoir through the valve and on to the downstream equipment.
If the valve closes quickly, the flowing water will stop suddenly. The sudden deceleration down to zero velocity comes with a price, which is a large pressure wave starting at the valve. This pressure wave propagates opposite the direction of flow back to the reservoir. The wave moves at the speed of sound of the fluid and pipe, which will be about 4,300 feet per second (ft/s) for water in a steel pipe.
That is not the end of the story. Once the wave reaches the end point (the reservoir), it will reflect through the pipe. The reflected pressure wave is now about the same magnitude, except it is below the static pressure in the system. This continues within the system until friction and pipe wall elasticity dampen the pressure spike energy.
If the valve has a near-instantaneous closure, the magnitude of the pressure spike can be estimated using the Joukowsky equation:
The pressure spike will be 579 pounds per square inch (psi). Remember, this is above the system static pressure. If the expansion joint has a maximum working pressure of 150 psi and the system is running at this pressure, the joint can be subject to a pressure spike of 729 psi. This may be surprising, but water is heavy (62.4 lb/ft3). Water is also nearly incompressible. Even if the pipe is relatively small, say 6 inches in diameter, the bulk flow at 10 ft/s works out to 125 pounds per second coming to an instantaneous stop.
If the expansion joint survives the positive pressure spike, a negative pressure spike is not far off. The pressure wave will now reflect from the terminal point of the system not only in the opposite direction but of the opposite magnitude—a negative pressure wave, which can create vacuum conditions if the system is closed to atmosphere. Moreover, cavitation is a real possibility and may increase the pressure spike even higher than the Joukowsky equation predicts.
If the “expansion joint as shock absorber” idea is not recommended, what options are available? The good news is that most systems can be modified to eliminate water hammer. The bad news is that the system will have to be modified. There likely will not be a cheap way out of the problem. Typical sources of water hammer for heating, ventilation and air conditioning (HVAC) or plumbing systems are:
- Fast-closing valves (e.g., solenoid valves) or incorrect check valve selections
- Hard-start pumps (pumps that are either on or off, no modulating)
Fast-closing valves may be replaced with slower-acting valves. For example, a solenoid valve may be replaced with a slower-acting ball or butterfly valve. If the problem is with a check valve, several manufacturers offer models that reduce water hammer risk at a pump discharge. A soft-start or variable frequency drive may be added to a motor to modulate the start and stop. If these modifications are not possible, another common solution is to add an accumulator near the source of the water hammer. In this example, the accumulator can be added in the vicinity of the valve.
Surge
If the event is not as sudden or near-instantaneous, there is good news. There will still be an increase in pressure, but it will not be as extreme. This is known as surge. The resulting pressure increase should still be assessed, but the potential for damage is less than with a hammer condition. If we use our previous example but with a valve closing time of five seconds, the surge calculation will be much different:
If the flow is 10 ft/s, the surge pressure will be 0.67 psi.
The difference between surge and hammer is the duration of the event compared to the propagation time of the pressure wave through the piping system, defined as:
- t = 2L/a
- L = distance from point of disturbance to end of pipeline
- a = speed of sound in full pipe
Until this point, the length of pipe was not a factor in the determination of the pressure increase, but pipe length is now necessary to determine the difference between hammer and surge. If the pipe length in the previous example is 500 feet from valve to reservoir, the limiting event time will be 0.23 seconds. Any event lasting approximately 0.23 seconds or less would have the potential for water hammer. Events lasting much longer than 0.23 seconds will likely result in a surge event. A large, direct-acting solenoid valve can change state in 20 to 40 milliseconds (.02 to .04 seconds). This type of valve would not be a good choice for the system, and a slower-acting valve would be better. Similarly, a motor start/stop event lasting 0.23 seconds or less has the same potential for water hammer.
If the issue is with a check valve, the action should actually be fast-closing. A fast-closing check valve prevents the flow from accelerating in the opposite direction before the valve closes. Specifically, check valves should have the following characteristics to reduce the risk of water hammer:
- The mass of the moving elements should be low.
- The moving elements should not have far to travel from being fully open to shut.
- Springs are needed to initiate and assist closure.
Piping systems are designed to be static. If the pipes jump, people will pay attention and look for a quick solution. If the system is experiencing water hammer, an elastomeric joint will not address the source of the disturbance and may sustain damage due to the extreme pressure. Another solution is required to address hammering. By contrast, surge events are longer in duration and result in much less dramatic pressure increases. Elastomeric joints are more compatible with surge conditions and can provide isolation between the source and the connected piping.
References
- Antaki, George A., Piping and Pipeline Engineering, Marcel Dekker
- Ballun, John V., A Methodology for Preventing Check Valve Slam, Journal AWWA March 2007, pp.60-65
- Thorley, A. R. David, Fluid Transients in Pipeline Systems, Second Edition, Professional Engineering Publishing, Ltd.
We invite your suggestions for article topics as well as questions on sealing issues so we can better respond to the needs of the industry. Please direct your suggestions and questions to sealingsensequestions@fluidsealing.com.