Within the oil and gas industry, the rotating shafts of equipment—such as pumps, motors, compressors, gearboxes and turbines—perform an essential function in both upstream and downstream applications. This rotating equipment ensures process flow and the safety of employees and the surrounding community. Bearings are critical to the reliability of rotating equipment. If they fail, the equipment has to be repaired or replaced. Because they support the shaft, bearings are prone to wear and damage. Lubrication starvation and contamination are the principal factors that cause premature bearing failure, so systems have been developed to prevent these issues. Methods for sealing the gap between a rotating shaft and the stationary bore have evolved with advances in lubrication and lubrication delivery systems. Selecting the right seal for a lubrication system will yield the best bearing protection. Lip seals and labyrinth seals, also known as bearing isolators, are the most common solutions. Lip seals are unidirectional contact type seals. Their geometry is important for maintaining an optimal radial load on the shaft to develop a meniscus of oil on which the lip can ride, which reduces friction and wear on the shaft and lip (see Figure 1). Depending on the direction of the installed seal, it will either prevent egress of lubrication or ingress of contamination (see Figure 2).
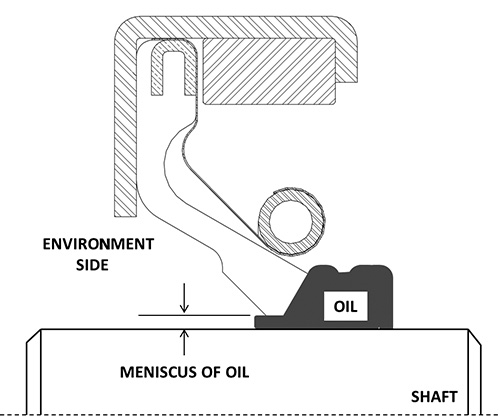
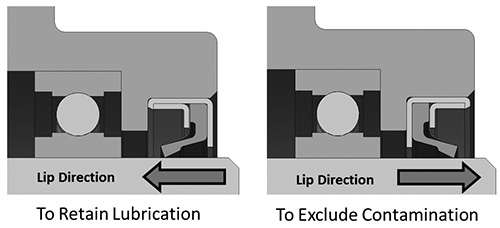
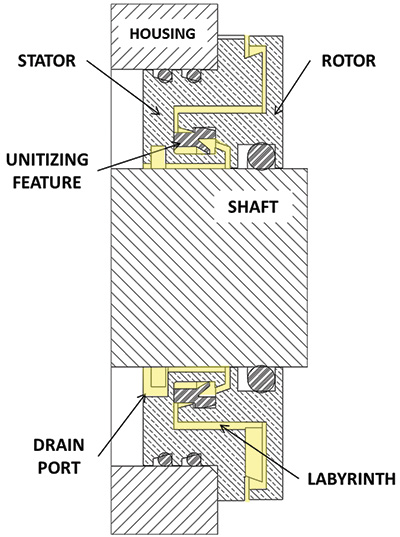
Grease Purge
Grease is an easy lubricant to apply and maintain, and it can be used to prevent contamination. Its consistency makes it easy to seal within bearing chambers. Most equipment designed for grease lubrication is equipped with a purge stream. This allows fresh grease to be pumped into the bearing chamber, replacing degraded or contaminated grease. Grease purging is a common practice, but should only be carried out with an understanding of the grease flow’s effect on the seal. Lip seals are suitable for use with grease lubrication, since only one seal installed facing the external environment is typically needed. This configuration prevents contamination of the grease by water or dirt and allows it to be purged under the lip if the discharge port becomes plugged or otherwise obstructed. Lip seals are rarely installed with the lip oriented toward the grease. Applications in which no grease should ever escape the seal, such as those in the food industry, are exceptions. In these instances, a metal case lip seal or cover plate that helps retain the seal in the bore is recommended. This helps prevent the seal from blowing out from purge pressure of the grease.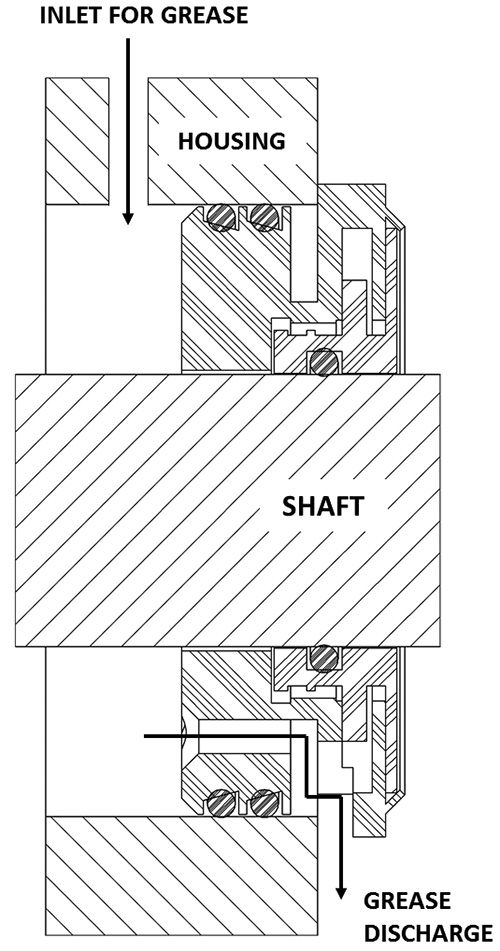
Oil Bath
Oil bath/splash is the simplest type lubrication system. It requires only minimal maintenance. A side glass or dip stick should be provided with these systems to ensure that the proper level of lubrication is maintained. The level typically should be at the center of the lowest rolling element of the bearing. With each rotation of the shaft, the rolling elements distribute the oil within the bearing. This poses a problem for lip seals. Depending on the size of the bearing and the speed of the shaft, the lip could be starved of oil and unable to develop a meniscus. This means that the lip would contact the shaft, grooving it and reducing the seal’s life. Bearing isolators are designed for this type lubrication system. In addition to labyrinths that prevent the escape of lubrication, they have drain ports to capture excessive oil splash and drain it back to the sump. With the smaller footprints of today’s pumps, the distance between the bearing and the back of the seal is reduced, creating a more aggressive splash onto the bearing isolator. As a result, manufacturers have redesigned drain ports to capture more lubrication and direct it back to the sump.Oil Mist
Oil mist is becoming a popular lubrication system, especially in the oil and gas industry. Oil mist systems are approved by the American Petroleum Institute (API) 610 specification for centrifugal pumps for the petroleum, petrochemical and natural gas industries. An oil aerosol is dispersed within the bearing chamber to lubricate the bearings. If not vented properly or applied in a closed-loop oil mist system, the pressure will increase within the bearing chamber. This increased pressure makes capturing the mist within the bearing housing difficult because the higher pressure in the bearing chamber attempts to obtain equilibrium, carrying the oil mist into the environment.