The reliability of an end-face mechanical seal depends on three factors—application, installation and operation.
One factor stands out as the primary cause of premature seal failure—application. This involves defining the conditions inside the seal chamber, which dictates how long and how well the seal performs.
The highest reliability comes from:
- choosing the appropriate design to meet the specific equipment and operational demands
- selecting materials that are compatible with the process conditions
- controlling the environment within the seal chamber or stuffing box
Design
The variables that most affect design selection are equipment characteristics, application and operating conditions, and the leak rate objective. The first decision rests in determining if one or multiple seals will be required, which often has the potential for a devastating impact on overall performance and reliability.
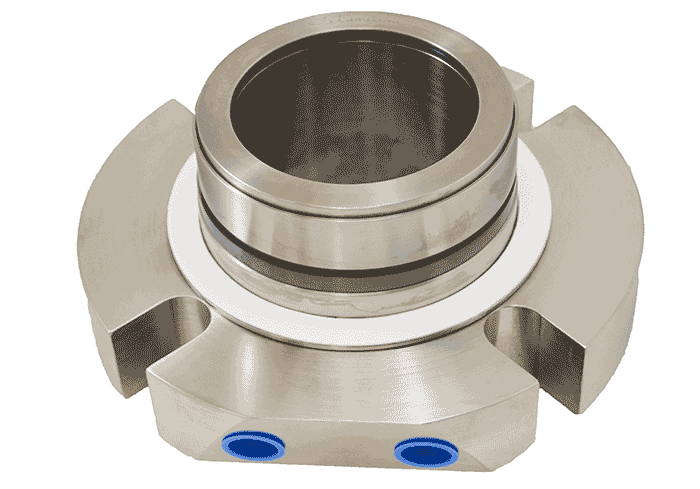
One of the primary requirements when applying end-face seals on high-speed rotating equipment is ensuring that lubrication is sufficient at the primary seal interface.
Excessive rubbing friction between the rotating seal ring and the stationary mating ring must not occur. It can quickly wear and deteriorate the sealing components, causing rapid failure.
Relatively clean process fluids with adequate lubricating properties can be effectively contained with a single-seal arrangement. Single-seal arrangements are usually less expensive to install and simpler to operate and maintain.
However, the following applications will not provide adequate lubrication:
- slurries
- polymers
- viscous fluids
- process liquids operating near
- flash point
- vacuum or dry-run operating conditions
These fluids require the injection of an external flush. This flush may require a multiple-seal arrangement if process dilution is undesirable or prohibited.
The design must operate at fluctuating peripheral speeds and pressure. It must also stand up to complex equipment conditions, such as when axial and radial shaft movement exceeds allowable tolerances.
Design considerations also affect the amount of leakage to atmosphere, dictated by the plant’s leak rate objectives. All end-face mechanical seals operating effectively on high-speed applications allow a small amount of vapor to pass through the primary seal interface. Average leakage will be in the 1 cubic centimeter (cc) per day range, which is within acceptable tolerances of most process fluids.
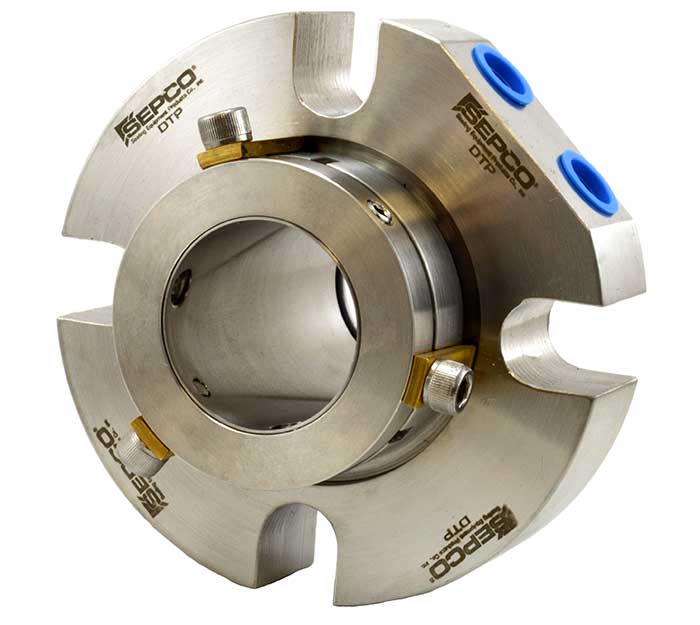
However, allowable leakage rates to atmosphere of hazardous or toxic process fluids are regulated and mandated by government agencies, such as the Occupational Safety Administration and the Environmental Protection Agency (EPA). Safe sealing can only be met by specific configurations and designs that minimize leakage rates to the accepted tolerances.
Materials of Construction
The selection of materials in the application process is also critical to achieving reliable mechanical seal performance. This includes alloys for manufacturing the hardware and mechanical loading devices along with materials for the primary seal faces and the secondary seals.
Careful consideration is required to ensure all the selected materials are compatible to the process fluid and the environment where the seal will be exposed.
Misapplication of materials of construction is a common error that rapidly leads to premature seal failure. For example, process fluids that are sticky, such as glue, molasses, and paint, can bind the faces together. When placed under excessive mechanical stress, the fluids may fracture and destroy fragile materials causing immediate and catastrophic failure.
Erosion and abrasion from solid particles in the process fluid also rapidly wears soft-face materials, as well as the seal hardware. Without careful selection of the seal alloys, corrosive penetration may exceed the maximum allowable rates.
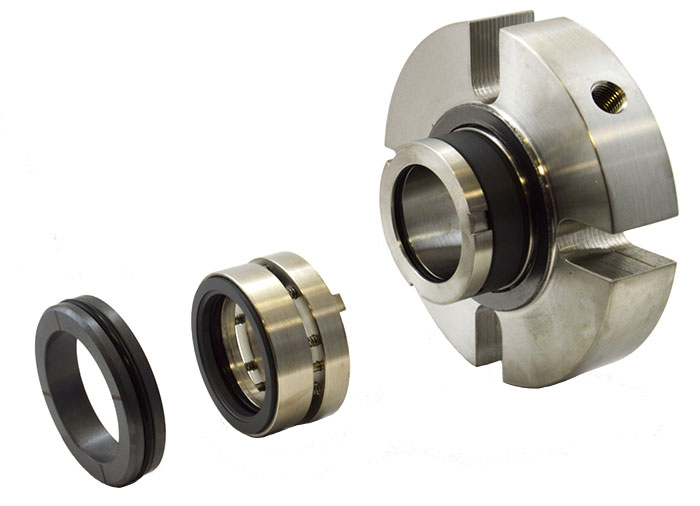
Excessive heat will also lead to deterioration and rapid failure of face materials and secondary seals. The quality of materials should also consistently meet the highest degree of standards available to minimize heat and wear.
Ensuring that the materials are ideal for the application will extend seal reliability.
Environmental Control
Even with the ideal design or carefully selected material, problems may arise. Any hostile conditions within the seal chamber or stuffing box can override the capabilities of the design and materials, diminishing reliability.
For example, in wastewater treatment plants, raw sewage must be moved with high-speed centrifugal pumps. These water-based solutions are entrained with solids that can hang up the seal and quickly wear and erode the selected materials should the slurry migrate into the chamber or stuffing box.
Flush water from an external source is a common solution for preventing premature failure. It floods the seal cavity with a clean, cool water. This flush must be maintained at higher pressure than the wastewater.
It provides a clean, cool environment which is essential for safeguarding the life of the mechanical seal. These single-seal systems operating properly will increase water consumption and will also dilute the pumped product.
In some facilities, water consumption may be a primary concern or process dilution cannot be tolerated. For these situations, a dual-seal system operating in conjunction with an independent clean liquid flush will be required.
Other environmental factors, such as temperature and pressure, must also be carefully controlled to prevent leakage. In addition, careful attention should be given to the environmental control systems specified for sealing hazardous or toxic fluids. They must meet the allowable leakage tolerances for the fluid being sealed and prevent excessive leakage if a seal fails.
The Whole Application Picture
Extending the life of end-face mechanical seals hinges primarily on clean and cool operation. The application in which the seal will be installed directly affects this required clean and cool requirement.
Every application, process fluid, and change in the environment adds a new and often unconsidered mix of consequences, which is why the application has such a tremendous impact on seal reliability.
Consideration of all the applicable factors must be made available and carefully considered by experienced seal personnel. This will maximize the chance that the specified seal system is properly applied. Good application combined with input from an experienced seal manufacturer will ensure that the recommended system results in a high level of reliability.
Read more Maintenance Minders articles by clicking here.