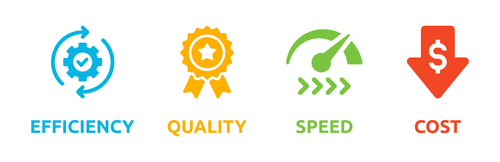
In the world of industrial pumping systems, seals may not always get the attention they deserve. However, they play a crucial role in the overall efficiency, reliability and longevity of pump systems. Seals are essential components that ensure fluid containment, minimize leakage and prevent contamination. When seals are not functioning optimally, the entire system can suffer from decreased efficiency, higher energy consumption and increased maintenance costs. This article explores how seals directly impact the efficiency of pump systems and why proper seal selection, maintenance and management are key to achieving optimal pump performance.
What Seals Do for Pumping Systems
Seals are designed to prevent fluid from leaking out of the pump casing while preventing contaminants from entering. This is particularly important in pumps used for handling hazardous, corrosive or high-value fluids. Effective seals also help maintain the internal pressure and operating conditions of the pump, ensuring it runs at peak efficiency.
Key roles that seals perform in pump systems include:
- Preventing fluid loss: Leaks in the sealing areas can lead to the loss of fluid, whether it is oil, chemicals or even water. Fluid loss not only affects the efficiency of the pump but also leads to safety hazards, regulatory violations and environmental damage.
- Minimizing friction and wear: Seals help reduce the friction between moving parts of the pump, including the shaft and casing, which decreases wear and tear. Lower friction results in less energy consumption, making the pump more efficient.
- Protecting against contamination: Seals act as barriers, preventing contaminants from entering the pump. Contaminated fluid can damage pump components, reducing their life span and increasing the likelihood of failure.
- Ensuring consistent performance: By keeping the system's internal environment stable, seals contribute to the pump's ability to maintain its performance across a wide range of operating conditions, from varying pressures to fluctuating flow rates.
Impact of Seal Performance on Efficiency
The performance of the seals directly influences the overall efficiency of a pump system in the following ways:
1. Energy efficiency and operational costs: When seals wear out or fail, they allow fluid leakage, which increases the amount of energy the pump needs to compensate for the lost fluid. For example, in centrifugal pumps, leakage can reduce the pressure and flow rate, forcing the motor to work harder to achieve the desired output. This inefficiency increases energy consumption, which can lead to higher operational costs.
Additionally, improper seals can cause overheating, as the pump's energy is wasted on unnecessary friction and leakage rather than effectively moving fluid. This puts extra strain on the motor and other components, leading to more frequent repairs and replacements.
2. Seal wear and maintenance: Over time, seals are subject to wear from the abrasive nature of the fluid being pumped, operating pressures and temperatures. This wear and tear can lead to leaks and eventual pump failure, causing unplanned downtime and costly repairs. The more often seals need to be replaced, the higher the maintenance costs. Additionally, downtime for repairs means lost productivity, which can significantly affect the overall profitability of a business.
By choosing high-quality seals designed for specific applications and ensuring their proper installation and maintenance, businesses can minimize wear and tear, extend seal life and reduce the need for frequent replacements.
3. Preventing contamination and downtime: In many industries, such as pharmaceuticals, food and beverage and chemicals, contamination is a significant concern. A failure in sealing can allow dirt, air or other contaminants to enter the pump, which can degrade the quality of the fluid being processed. In such cases, seal failures can lead to system contamination, product spoilage and even legal liabilities if safety and quality standards are violated.
Regular maintenance and the proper selection of seals for the operating environment can prevent these issues. Seals that are resistant to chemicals, heat and abrasion ensure that pumps maintain a consistent level of cleanliness and safety, ultimately avoiding costly contamination events and the downtime that comes with them.
How to Optimize Seal Performance for Efficiency
To optimize seal performance and ensure long-term efficiency in a pumping system, consider the following strategies:
1. Select the right seal: Choosing the correct seal for the specific fluid, temperature and pressure conditions is the first step in ensuring system efficiency. Mechanical seals, for example, are often used in high-pressure and high-speed applications, while lip seals are suitable for lower-pressure systems. The material of the seal—whether it is elastomeric, polytetrafluoroethylene (PTFE), ceramic or another advanced material—must be compatible with the fluid being pumped to resist wear and corrosion.
In addition, seals designed with energy efficiency in mind (such as low-friction seals) can further reduce energy consumption and increase overall pump efficiency.
2. Regular inspection and monitoring: Monitoring seals for early signs of wear is essential for preventing unexpected failures. Routine inspection for leaks, changes in vibration or excessive heat buildup can provide valuable insights into seal health. Using advanced technologies like vibration analysis, thermal imaging or even smart sensors can help detect seal degradation before it leads to significant issues.
3. Proper installation: Proper installation is crucial for ensuring the seal performs as intended. Incorrect alignment, poor surface finishes or improper tightening can all lead to premature seal failure. Ensuring seals are installed by trained professionals and following manufacturer recommendations is vital for maximizing seal life and maintaining system efficiency.
4. Proper lubrication and cooling: For seals that operate under extreme conditions (such as high temperatures or pressures), ensuring proper lubrication or cooling is critical. Without adequate lubrication, friction between the seal and other pump components can cause excessive wear and heat buildup. This can lead to seal failure and inefficient operation.
5. Choose seals with low leakage: Seals with lower leakage rates are essential for maximizing fluid retention and pump efficiency. Even small leaks can result in significant energy losses over time, especially in large-scale pumping systems. Advances in seal design, including advanced lip seals and improved mechanical seal designs, have helped achieve lower leakage rates and better overall sealing efficiency.
Seals are not just an ancillary component of pumping systems—they are fundamental to the overall performance and efficiency of the system. By preventing fluid leakage, reducing friction and protecting against contamination, seals help ensure pumps run smoothly, consume less energy and experience less wear and tear. Understanding the role of seals in pump efficiency and taking proactive steps to select the right seals, maintain them properly and monitor their condition will help operators improve system performance, reduce operational costs and extend the life of their pumping equipment.
Investing in quality seals and adopting best practices for their maintenance is an investment in the long-term efficiency of the entire pumping system.