The most versatile pump used for fluid transfer in sanitary applications is an air-operated double diaphragm (AODD) pump. AODD pumps are well-known for their ability to stall under pressure, meaning that no external controls are necessary to start and stop the pump. However, the most identifiable feature is the sealless design that eliminates the need for mechanical seals, which can require costly repairs and will eventually leak. These self-priming pumps can run dry without damage. They are ideal for transferring food-related items. Food and Drug Administration (FDA)-compliant AODD pumps can handle different materials, ranging from those with the viscosity of water to less pourable materials, such as cottage cheese. AODD pumps are not used only in sanitary-related applications. Many industrial companies rely on the same pump features to handle materials in industrial applications, such as paints, chemicals, inks, cleaners, adhesives, sealants, lubricants and concrete mixtures. Larger AODD pumps can even handle viscosities more than 20,000 centipoise. In industrial applications, companies also take advantage of the non-electric requirement in metal and conductive polymer pumps to be grounded and perform safely in hazardous environments. In sanitary applications, industrial AODD pumps that have polypropylene, stainless steel or polyvinylidene difluoride (PVDF) fluid sections are commonly used to transfer and meter chemicals during the clean-in-place (CIP) process.
Basic AODD Pump Principles
AODD pumps work by creating a pressure differential between the fluid cavity inside the pump and the source of supply. As the pump strokes, one side pushes or forces the fluid away from the pump by unseating the upper check ball, which acts as a valve. While this is occurring on one side of the pump, the opposite side is simultaneously pulling the top ball check down, creating a seal, and pulling the bottom ball check upward, or unseating the lower ball. AODD pumps have four ball checks, and at any given time, two of these checks are being unseated (opened) and two are being seated (closed). How does the fluid enter the pump? Many believe the AODD pump creates a vacuum. However, the pump actually lowers the pressure in one fluid cavity to a point below the atmospheric pressure being exerted on the supply tank and line feeding the pump. The result is a pressure differential between the supply and the fluid cavity in the pump. Every time the pressure in the fluid cavity falls below atmospheric pressure, the higher pressure fluid in the supply tank and fluid line rushes into the cavity to equalize the pressure.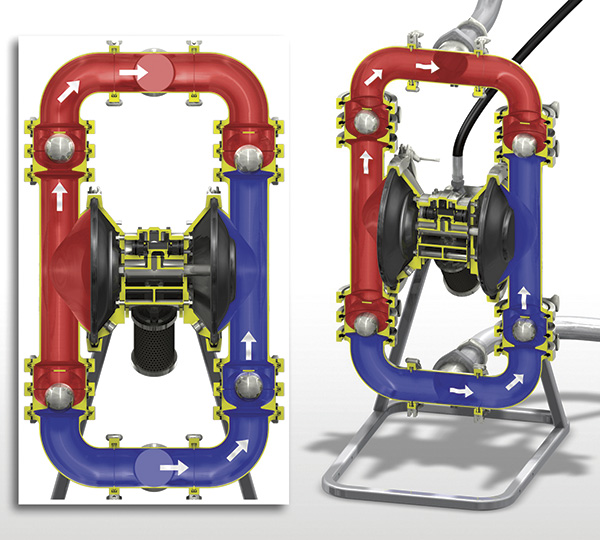
Choosing the Right Pump
Different AODD pumps serve specific applications better than others. Diaphragm pumps are versatile with flow rates ranging from less than one gallon per minute to nearly 300 gallons per minute. Pumps are available with materials including cost-effective aluminum, stainless steel and corrosion-resistant polymers like acetal, polypropylene and PVDF. In addition, fluid section configurations use different balls, seats and diaphragms to effectively handle a multitude of materials. When choosing an AODD pump, production managers should start by answering the following questions:- What is the desired flow rate?
- What material is being pumped?
- What is the material’s viscosity?
- Is the material abrasive?
- What is the particle size?
- Where is the feed tank in relation to the pump?
- What is the suction lift distance?
- What is the vertical rise?
- What is the discharge distance?
- What is the inlet hose diameter?
- What is the outlet hose diameter?
- What is the material temperature?
- What is the pressure of the shop air, if a pneumatic solution is selected?
- What certifications are required?
- What special applications need to be considered?
Potential Problems
The way the fluid flows through the pump should also be considered. Most AODD pumps incorporate a bolt-through diaphragm design, in which the fluid plate holds the diaphragm in place and is exposed to the material being pumped. Particles can get behind the fluid plate and gradually cut through the diaphragm, shortening its life. Another problem is the gap between the fluid plate and diaphragm created with every stroke, which can harbor bacteria. This area is nearly impossible to clean without completely dismantling the pump and removing the fluid plate.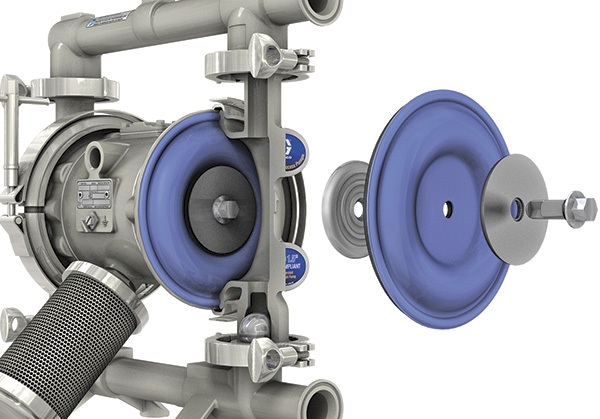
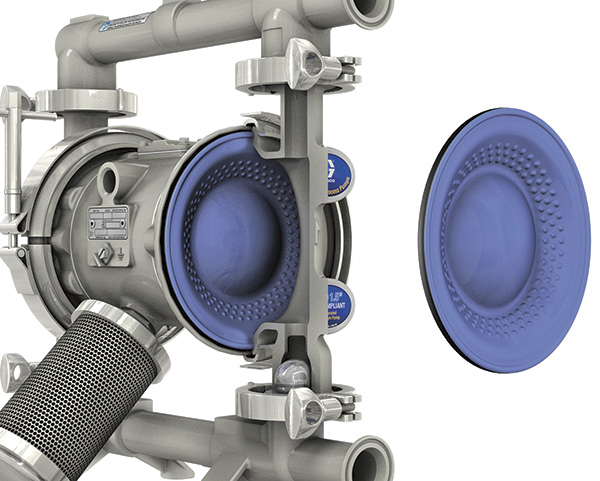
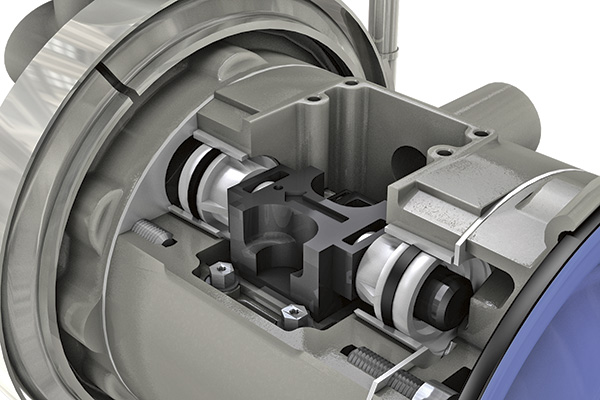
Replacement Parts
Diaphragm replacement can be difficult. Typical diaphragm change-out times are about one hour. One pump manufacturer has developed an easy-to-use diaphragm change out tool that reduces this time to between 15 and 20 minutes for its air valve. The tool prevents normal operation of the air valve and diverts air to the selected air chamber. Pins are then placed in the main valve cup’s pistons, preventing it from shifting. The main valve cup is replaced with the directional tool that includes an arrow to select direction. This tool diverts air to the side of the pump that is desired (the side that has already been assembled). When the pump has been fully assembled, the pins are removed and the main valve cup is replaced.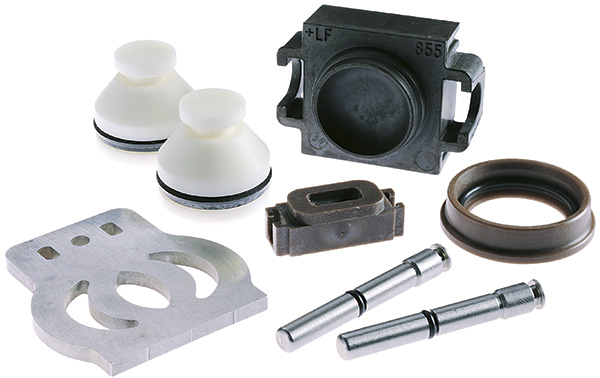