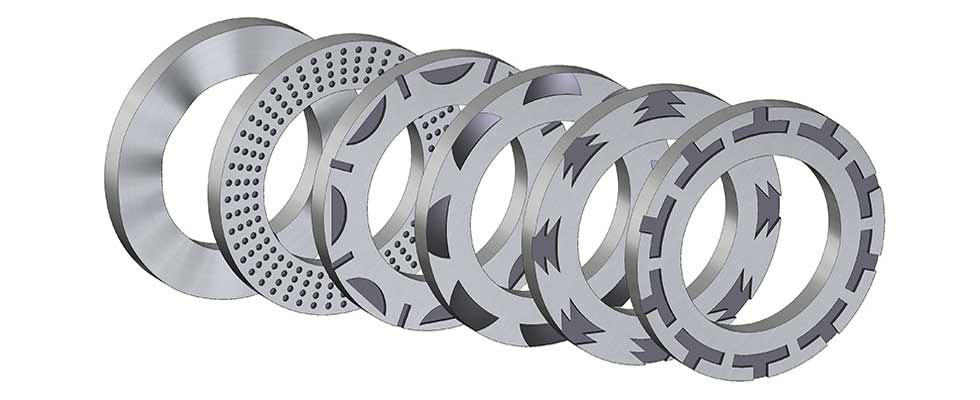
A mechanical seal is a common, yet incredible, piece of technology. From the simplest applications to the most difficult conditions, designs have been created to reliably prevent leakage in rotating equipment. A singular design cannot possibly address every set of conditions and the multitude of applications that exist. Relying on the experts that develop the designs and materials used in mechanical seals is often the most prudent approach for extracting the best value.
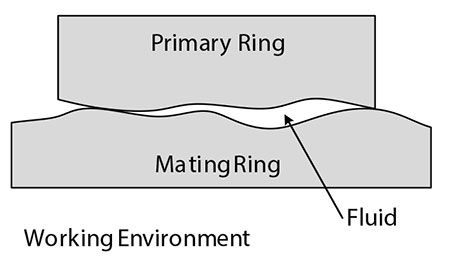
The faces within a mechanical seal are probably the two most critical components to ensuring proper function. These components must handle relative motion, often varying system pressures, temperatures and rotating speeds while maintaining the integrity of an interface to a precise contact pressure that remains flat and smooth, often to millionths of inches. These faces are highly designed in terms of configuration and the materials used. Because the interface between the primary and mating ring is where fluid lubrication is critical for providing low leakage, maintaining that pristine interface usually is the prerequisite for ultimate success. The goal is to get just enough fluid between the faces to keep them pseudo-lubricated while not allowing too much, causing the fluid to escape (seal leakage).
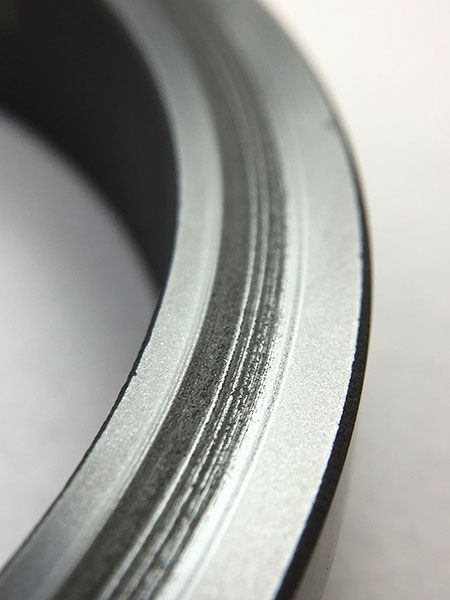
A variety of mating ring materials are regularly employed. Looking at the transition of increasing capability and hardness, stainless steel might be considered an economical entry point, then improving by moving toward oxide ceramics (alumina), coated metals, cemented carbides (tungsten carbide), then nonoxide ceramics (silicon carbide), ending with diamond-coated nonoxides.
It is important to use the option that provides the best value for the application. Because these mating materials are not self-lubricating, a softer resin or metal-impregnated mechanical carbon graphite is often run against the mating ring and is called the primary ring.
As application demands increase, there are more instances with the need for both faces to have increased hardness that can be achieved primarily with the use of carbides and ceramics. Because these materials, excluding the premium diamond-coated option, are not inherently self-lubricating, additional consideration is taken to manage the interface conditions. Running carbides against each other in the absence of some form of lubrication will generate damage, often called phonographing, to one or both surfaces quickly, creating potential leak paths or frictional heat generation.
With a hardface mating pair, “too smooth” can actually be “too bad” in terms of reliability because the surfaces can wring together and generate excessive torque and heat generation. Larger surface areas can also limit capability because of the challenges associated with lubricating the entire mating surface.
In general, the challenge of interface lubrication has been addressed through mechanical seal design with innovative surface modification. Image 3 highlights some of the more popular options for mechanically enhancing interface lubrication and resulting cooling.
The features can also serve to moderate the closing force through hydrodynamic lift management, further enhancing reliability. Varying levels of success can be projected and depend on the level of abrasives in the system which, when present in excessive levels, can trap the abrasives and then damage the interface. The use of hybrid nonoxide ceramic materials that combine the hardness and stiffness of a silicon carbide with a softer, graphite phase has also been used successfully to improve the interface conditions.
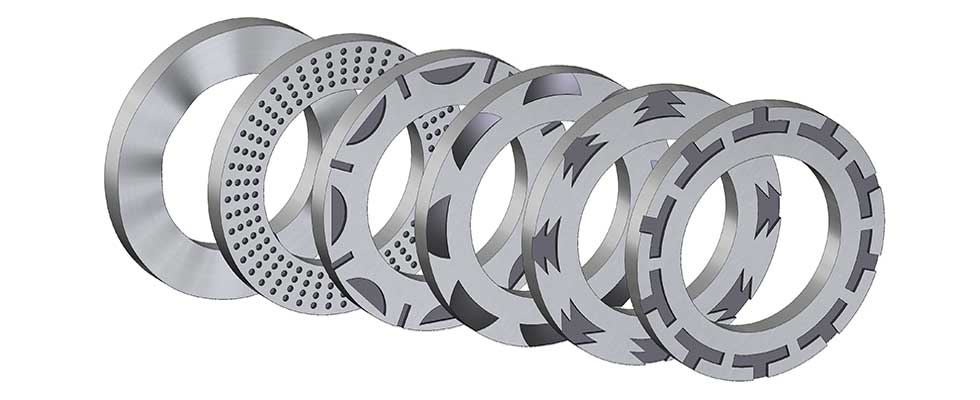
These material combinations, in conjunction with proprietary machining techniques, provide a permanently unique and controlled surface topography that enables:
- controlled surface roughness to precisely enhance fluid presence at the interface
- increased thermal conductivity to efficiently transport generated frictional heat away from the interface
- high hardness to effectively pulverize any solids that tend to come out of solution near that interface
- minimal tendency to trap those abrasives at the interface
One example of a mechanical seal system that will likely perform better with a hard face combination involves the pumping of fluids that contain abrasives and/or high solids contents.
The conditions can be further aggravated by the precipitation of solids from the sealed fluid, typically occurring nearest a heat source. A case-in-point is antioxidants that are used in glycol cooling systems to maintain the thermal transfer capability of the system.
Testing was performed with a variety of face material combinations shown below and demonstrates the effect of mating pairs on tribology.
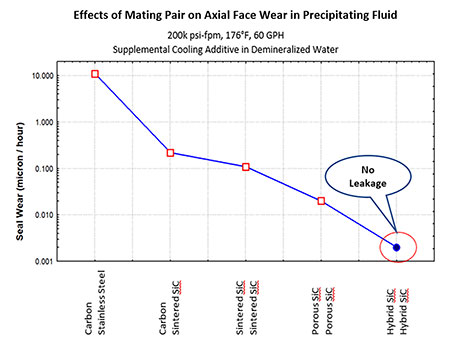
The faces of the parts were polished in this testing; surface modification was not evaluated. The horizontal axis provides the primary and mating ring materials evaluated. Axial wear and seal leakage were measured. In the conditions established, one hybrid silicon carbide (SiC) provided the best results in terms of tribology and was the only combination to provide leakproof sealing.
Mechanical seals are a sophisticated technology that can provide reliable service for extended periods of time through the appropriate application of component and material design.
We invite your suggestions for article topics as well as questions on sealing issues so we can better respond to the needs of the industry. Please direct your suggestions and questions to sealingsensequestions@fluidsealing.com.