The markets for pumping systems are seeing an ever-increasing focus on energy efficiency in an effort to reduce carbon emissions, resource usage and costs of operation. Industrial pump system users have heightened their focus on efficiency initiatives as natural resource and raw material usage costs increase. External drivers include the U.S. Department of Energy (DOE), which has highlighted data showing that pump systems represent approximately 6 percent of the total U.S. industrial energy consumption.
Plant Water Usage
When assessing the overall operating efficiency of plants, water usage can become a significant energy cost of its own. Water is commonly used as a primary system in power cycles. It is also used as a secondary system for cooling, dilution or cleaning. Closed-loop water systems require pumps, cooling towers and makeup water treatment systems that can consume significant electrical and thermal energy. Open-loop systems also require effluent treatment before returning the water to its source. Efforts to reduce water use and the associated energy costs are often a component of industrial plant best practices for efficiency improvement.
Pump Systems
Significant opportunities for improvement exist for energy and water use reductions in pump systems. Pumps are often operated at suboptimal flow and head, significantly decreasing efficiency. The Hydraulic Institute (HI) introduced the educational initiative “Pump Systems Matter” to help increase focus on this opportunity.
Certain types of sealing systems can have a large impact not only on energy but water usage as well. In some cases, the combined power use can equal or exceed that of the pump driver. The opportunities to reduce energy usage in sealing systems can be far greater than those achieved by correcting pump efficiency issues.
Life-Cycle Cost Tool
The Fluid Sealing Association (FSA) and the European Sealing Association (ESA) have produced a seal life-cycle cost calculator tool that estimates the relative energy consumption of different sealing system configurations. This tool can be used to help customers identify the most efficient system option for their applications.
ISO Assessment Standard
In addition to FSA’s calculator tool, draft Standard pr ISO 14414, “Energy Assessment for Pumping Systems,” has been released for comment in 2013. The draft contains an annex that provides simplified guidance on selecting sealing systems based on energy and water efficiency considerations. Figure 1 provides a quick reference to the thermal, water and electrical efficiencies of different seal arrangements and their supporting API piping plans. This figure is based on Table B.4 in Annex B of the ISO draft with permission from ISO. This “Sealing Sense” will provide an overview of the contents of this table, with examples of selected inefficient API piping plans and their energy and water usage impacts, along with alternatives to those plans.
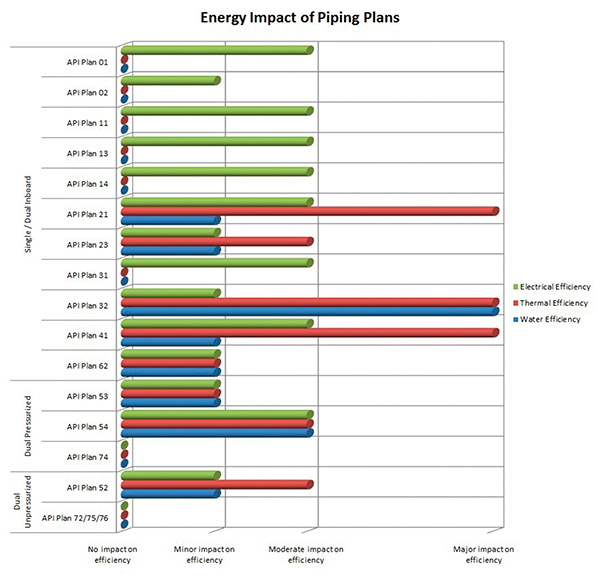
Figure 1. Energy Efficiency of Piping Plans and Seal Configurations
API Plan 32, commonly used on single seals (see Figure 2) stands out as the option with a potentially major impact on efficiency for thermal, water usage and electrical energy usage, having a rating of Major Impact in both thermal and water efficiency categories. FSA member company data indicates that approximately 15 to 20 percent of applications with temperatures of more than 200 C (400 F) use an API Plan 32. It is also a common selection in general industry slurry applications. This piping plan has long been a first recommendation for situations in which the pumped process fluid does not provide a suitable environment or lubricant for the seal. Injection of a cool, clean fluid with good lubrication properties solves this problem without requiring more expensive or robust seal designs to tolerate the process fluid conditions. However, the trade-off to using simple seal and system designs with this API plan is high energy use.
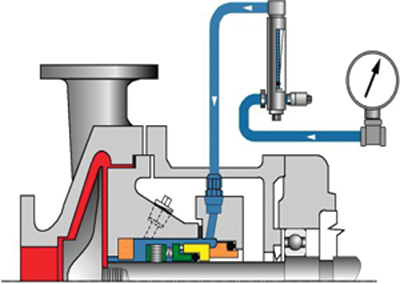
Figure 2. API Plan 32
Thermal energy usage can be very high when the Plan 32 injected fluid must be evaporated later in the process, such as in black liquor slurry applications. This is explained in detail in a case study in the draft ISO14414 Annex. In that case study, the combined energy usage of the piping plan is 84 kilowatts (113 horsepower) largely because of the need to evaporate the injected water. Water usage can also be high with Plan 32 when water is used as the injected fluid.
Alternative Sealing Systems
Alternatives to single seals with API Plan 32 depend on the application requirements. When Plan 32 is used for temperature control purposes, API Plan 23 provides a good alternative, with the use of a heat exchanger in a closed-loop system to remove heat. Dual seals with API Plan 53 provide an alternative when the process fluid does not provide sufficient lubrication for the seal. Single seal designs with API Plan 02, occasionally with a Plan 62 external quench, provide an alternative for slurry applications, although they commonly require more robust seal designs to tolerate those conditions.
Plans 21 & 23
API Plan 21 is another single seal plan (see Figure 3) that can consume large amounts of thermal energy because of the once-through flow of the process fluid within the heat exchanger. Commonly, larger heat exchangers are required by these plans to handle the high thermal load needed to cool the process temperature to a suitable level for the seal. This thermal load for Plan 21 doubles for cases in which the process temperature must be maintained, as in heat transfer applications, because the cooled fluid is reheated as it is recirculated into the process. API Plan 23 provides a good alternative to Plan 21, because the recirculation of fluid within the seal chamber cavity allows for smaller heat loads and corresponding exchanger sizes. In a direct comparison case study of these options prepared by FSA, an API Plan 21 configuration in a heat transfer oil application consumes 42 kilowatts (57 horsepower), compared to 5.8 kilowatts (7.8 horsepower) for Plan 23 in the same application.
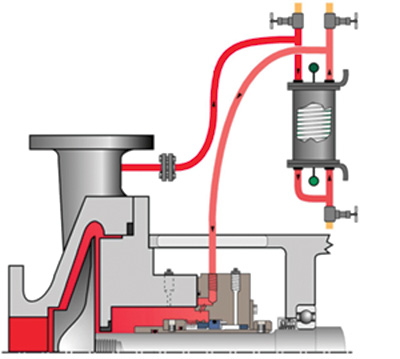
Plans 53 & 54
API Plan 54 is a dual seal plan (see Figure 4) that can consume relatively significant water or electrical energy depending on the application requirements and system design. In its simplest form, Plan 54 consists of a pressurized water source that runs once through the seal and is then sent to effluent treatment, which can result in extremely high water usage.
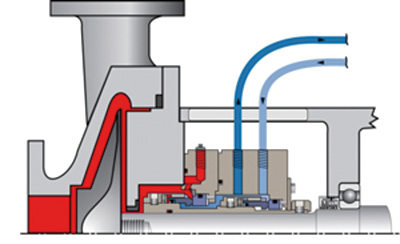
More advanced systems consist of a closed-loop system with a dedicated circulator, requiring electrical energy for that circulator, and possibly cooling water, depending on the heat load placed on the system.
In some cases, energy and water usage can be reduced by changing to more advanced technology seals, such as flushless single slurry seals for abrasive services, or dual pressurized gas seals for hazardous services.
In other situations, a dual seal must be maintained because of application considerations—including the prevention of hazardous fluid leakage, seal face lubrication requirements or several other factors.
In these situations, Plan 53 offers lower energy consumption through the elimination of closed-loop Plan 54 circulation pumps. For open-loop Plan 54 systems, conversion to a closed-loop system will significantly reduce water and energy use costs. Alternately, flow and pressure regulation devices may be employed to reduce energy usage on open-loop systems.
Conclusion
The selection and design of the sealing system can have a significant impact on energy and water use of the entire pumping system. The new ISO standard 14414 Annex will provide a simple selection guide for determining which options can minimize this impact, and the FSA/ESA Life Cycle Cost Estimator Tool can be used to further analyze the potential savings. In many cases, significant overall energy savings can be achieved by changing from less efficient to more efficient sealing system designs.