Many associations, societies and regulatory agencies have rewritten and redeveloped emissions and leakage standards and controls year after year. The partial list of organizations—based on voluntary consensus, regulation or legislation—includes the Environmental Protection Agency (EPA), American Petroleum Institute (API), International Standards Organization (ISO), Manufacturers Standardization Society (MSS) and TA Luft. When the process rules are changed, manufacturers of seals, packing and gaskets are forced to implement changes as well. The manufacturers either produce seals that are better suited to handle the new regulations or they drop out of the market. These changes affect the way end users must look at the quality of flexible graphite and its ability to seal.
Installed Density
Flexible graphite is one of only a few sealing materials that increases density through compression and compaction. This significant ability is called installed density. When compacted, most materials act as a dam for leakage. Compress any material enough in a confined area and it will seal, at least, during the short term. Flexible graphite, on the other hand, begins as a lower-density material which is then compressed and densified in a contained area. The resulting increase in compaction and density, which occurs because of the flow and movement of the graphitic material, must reach the point at which the graphite component attains the proper installed density. When this happens, the fluid is contained, the graphite is properly compressed, and it remains resilient. This is what makes flexible graphite an ideal sealing material for high-temperature applications. If this installed density is jeopardized, however, as one engineer described, it will be like pouring water over sand—a graphic way of depicting seal erosion and failure.Weight Loss
Several factors can cause a flexible graphite seal or gasket to lose density, including mechanical load loss or material loss. The degradation method that is seldom identified, however, is weight loss of the base material. This is why consistent quality of flexible graphite is critical. Flexible graphite is known as a high-temperature material, but high-temperature applications pose the risk of oxidation and gasket or seal weight loss. The oxidation of flexible graphite is similar to what happens to steel as it rusts over time. In the case of flexible graphite, the resultant weight loss reduces the material’s installed density and the ability of the gasket or seal to support the compression load, which can result in leaking and gasket or seal failure. Figures 1 through 3 depict how material grade, thickness and density can affect weight loss. Flexible graphite materials have improved significantly in the last few years. Figure 1 depicts the difference between base flexible graphite materials and flexible graphite materials that have oxidation inhibitors added. The addition of oxidation inhibitors has a much larger impact on the oxidation rate than graphite purity (99 percent versus 93.5 percent) or thickness. The different properties of the materials demonstrate the importance of material selection for critical high-temperature applications in oxidizing environments.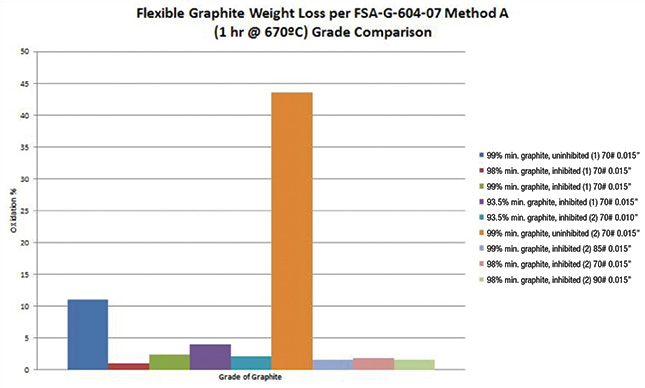
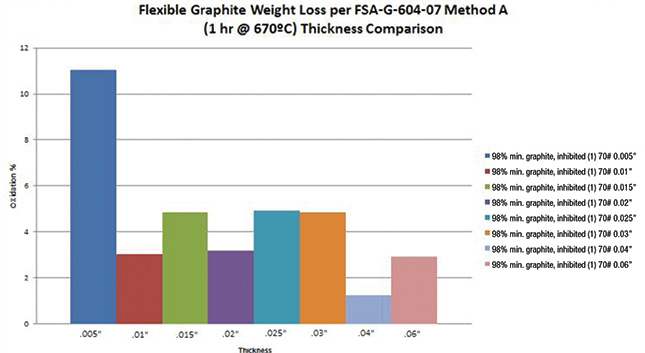
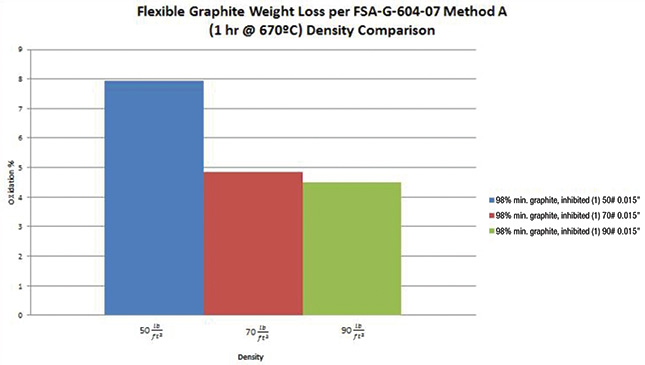