Natural gas popularity is growing exponentially because of its low cost, low risk to transport and store, and its status as one of the cleanest burning fossil fuels. With increasing global pressure to reduce greenhouse gas emissions, the need to meet growing energy demands while reducing these emissions is more important than ever. Hydrocarbons are comprised of hydrogen and carbon that release energy as they combine with oxygen to form H20 and CO2. Dry wood offers a combustible ratio of carbon to hydrogen of about 10 to 1. Coal replaced wood and powered the industrial revolution with a ratio of 2 to 1. Petroleum such as kerosene has a ratio of about 1 to 2. Natural gas is composed mostly of methane (CH4), which has a ratio of 1 to 4. That is a 40 times efficiency gain from wood to natural gas and eight times from coal to CH4. This improvement in energy efficiency also makes the energy cleaner because less ash and residue are created. Natural gas can also be a major contributor to the greenhouse gas effect because of its hydrocarbon intensity and leads to the importance of properly sealing the product in gasketed joints. There is a global revolution around natural gas—with modern technology in extraction, it is being piped and shipped globally (Image 1). Liquid natural gas transportation is unique because it must be liquified, and to do this, it must be cooled to approximately -260 F (-162 C). At this point, the gas condenses into its liquid form. This is important because liquified natural gas can be compressed to approximately 1/600 its original volume, which substantially increases the amount that can be both shipped and stored.
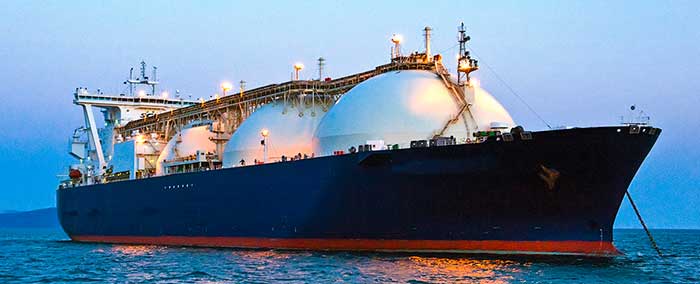
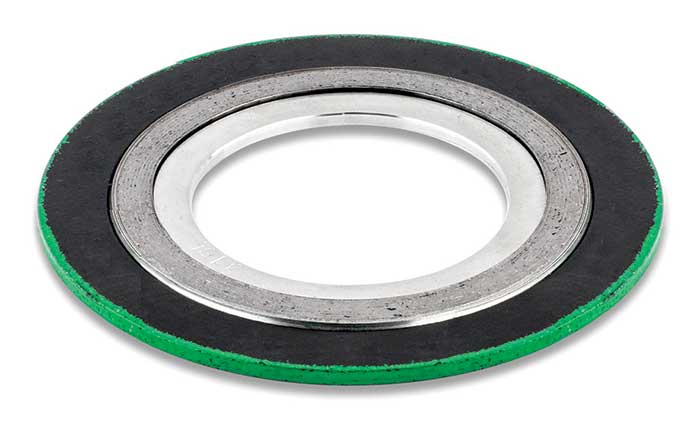
- It has a low temperature range of -400 F to -450 F (-240 C to -268 F).
- Spring-back or material compressibility and recovery show excellent properties for both thermal and mechanical cycling.
- It can also be used in a semi-metallic format in conjunction with metal components to create a spiral wound gasket (Image 2), a corrugated metal gasket with flexible graphite cover (Image 3), or a Kammprofile gasket.
- Metallurgy selection is important due to brittleness that can be found in ductile materials at low temperatures. Ideally 300 series stainless steel or nickel alloys are acceptable.
- The ease of cutting into complicated shapes provides high versatility.
- Flexible graphite gaskets can be fragile, so extra care needs to be applied when handling or transporting.
- Material can break off and contaminate the process (without an eyelet on the gasket ID/OD).
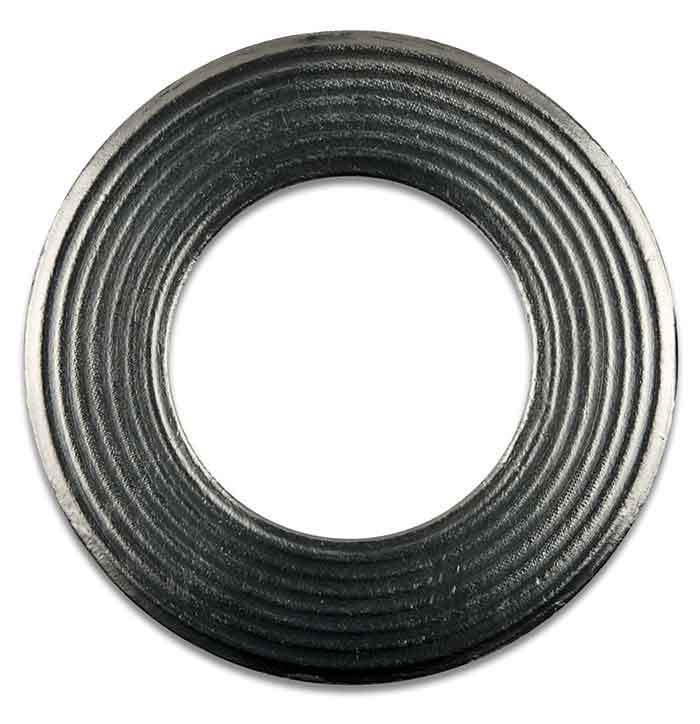
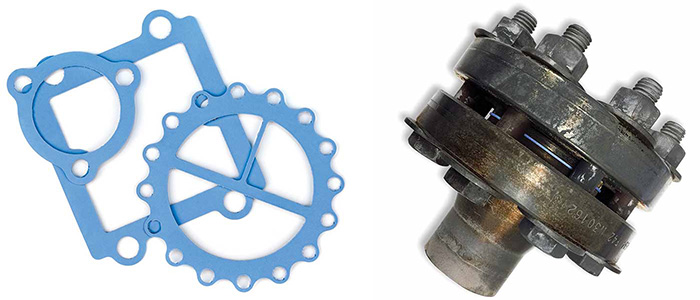
- It has a low temperature range of -350 F (-212 C).
- The material does not become brittle at low temperatures.
- As in the case of graphite, it can also be used in a semi-metallic format in conjunction with metal components to create a spiral wound gasket, or a Kammprofile gasket. The metallurgy selection is important due to brittleness that can be found in ductile materials at low temperatures.
- Eyelets are not required for pure applications such as oxygen service.
- Material can be welded to create large one-piece gaskets without a dovetail.
- Bundesanstalt für Materialforschung und –prüfung (BAM): Gaseous & Liquid O2 Drop Test
- American Society for Testing and Materials (ASTM): G86 LOX mechanical impact testing
- Det Norske Veritas and Germanischer Lloyd (DNV-GL)