Any coupling that connects rotating equipment generally serves two main purposes: transmitting torque and taking up misalignment. While in principle this can be fairly straightforward, there are many ways this has been accomplished. The primary design challenge has always been getting a coupling to transmit as much torque as possible, yet require as little force as necessary to be bent out of alignment. Economics is generally the driving force behind a great percentage of products. A very torque-dense coupling can be economical to produce because of its smaller overall diameter. Having a lower torque-dense coupling that can be easily misaligned protects and extends the bearing and seal life of connected equipment. The forces required to misalign a coupling are called coupling restoring forces. Restoring forces of a coupling can be an important consideration when developing a drive train system. High restoring forces can result in higher vibratory loads on bearings and seals, which can lead to premature bearing and seal failure.
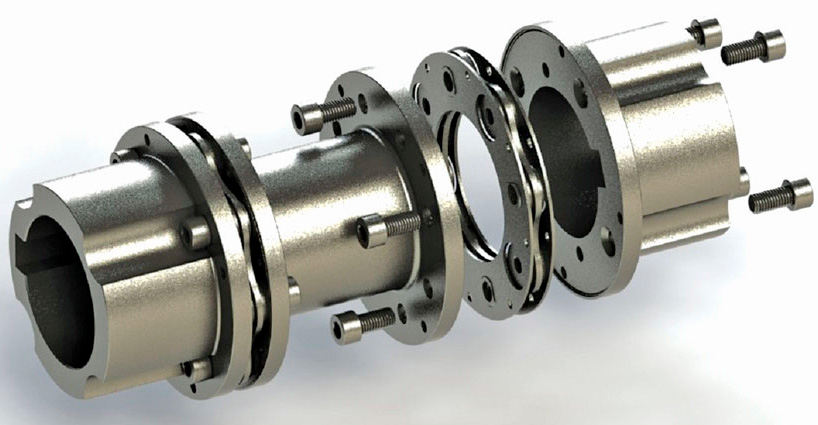
Fr = Ktang x Degmisalignment Equation 1 Where: Fr = restoring moment (in-lbs) Ktang = angular spring rate (in-lbs/degrees) Degmisalignment = coupling misalignment (degrees)
Some low-cost couplings like jaw style or elastomer donut-type couplings can generate high restoring forces because they have high misalignment ratings. Even though the coupling can take the misalignment, bearings and seals could have significantly shortened life. Gear couplings, on the other hand, have a varying level of restoring forces based on the amount of torque they are transmitting. This is because the gear teeth are transmitting torque through the same plane that needs to slip when being misaligned. The higher the transmitted torque, the higher the force required to misalign the coupling because the teeth do not want to slide due to friction. This can worsen significantly if lubrication is neglected. Gear couplings are very torque dense, which makes them economical, but they can have some of the highest restoring forces in the industry. Table 1 shows some basic comparisons between different styles of coupling and their respective restoring forces. Selection of a style of coupling depends on the application requirements.
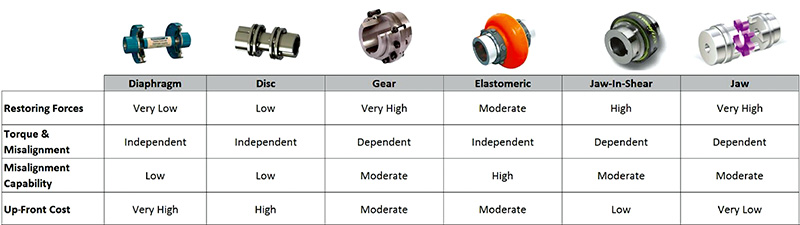