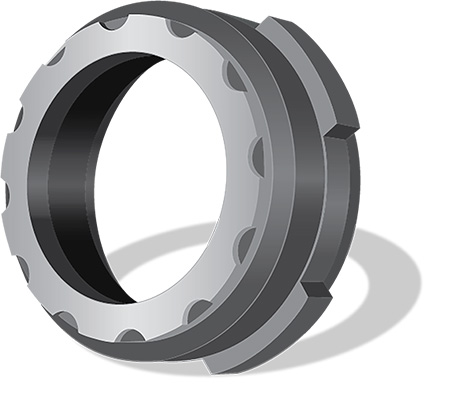
When a company in the design, manufacture and maintenance of binary Organic Rankine Cycle (ORC) power systems entered the geothermic energy market, its engineers knew the existing turbines would be put to the test.
The working ORC principle is similar to the thermodynamic Clausius-Rankine Cycle (CRC), a widely used process for power generation. CRC converts heat into work via a closed loop that typically uses water as the working fluid. An ORC system instead vaporizes an organic fluid, which is characterized by a molecular mass greater than water.
This organic fluid has a lower boiling point and a higher vapor pressure compared to water. As a result, it can use low temperature heat sources to produce electricity without harmful emissions. At the same time, ORC applications have recently become more and more challenging due to turbine mandrel space constraints, corrosive media and increased shaft speed. The European-based company knew it needed to focus on a cost-effective turbine design for power outputs up to 40 megawatts (MW) per single generator.
As part of the new design, the ORC company introduced new silicon-based fluids into the process. The new fluids not only presented temperature concerns but also corrosive condition challenges to the turbines’ existing double-cartridge mechanical seals.
To accommodate the silicon-based fluids, the company worked with a seal manufacturer to provide reliable solutions to the new, demanding operating challenges. The seal provider had worked with ORC companies for more than 10 years, supplying engineered products and services including mechanical seals, couplings, hydrodynamic bearings and seal support systems.
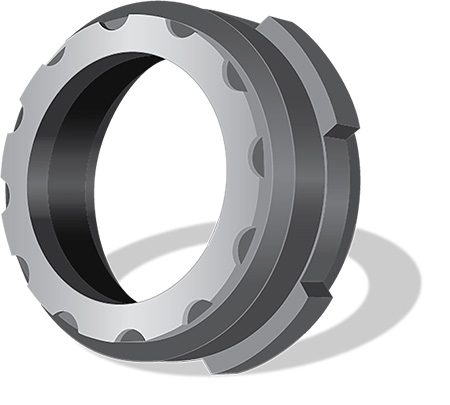
Ensuring Seal Design Reliability & Performance
Working closely with the ORC turbine manufacturer, the engineers evaluated numerous seal designs to address the increased heat and corrosive conditions. The designs included traditional heavy-duty, double O-ring pusher seals, with primary rings made of plain face abradable inserts in metal carriers, incorporating different elastomers, including polytetrafluoroethylene (PTFE), hydrogenated nitrile rubber (HNBR) and silicone rubber.
Based on experience with double O-ring pusher seals, the engineers tried a number of solutions that would stand up to the high thermal load—230 F to 644 F (110 C to 340 C). Different seal primary ring designs were tested as well. However, none met the heat transfer, leakage and other performance criteria. In addition, concerns were raised about maintaining proper levels of fluid film needed to lubricate the seal faces and the amount of leaking of the process fluid.
A Recessed Solution
As a result of the testing, the metal carrier press fitted carbon inserts were discarded in favor of graphite loaded silicon carbide (SiC) primary rings, providing deformation resistance with a better heat exchange coefficient. The requirements for fluid film formation were addressed by incorporating hydropads into the seal design.
As the name suggests, hydropads are slots on the sealing surface that generate hydrodynamic separation force between sealing rings. This technology has been successfully used for years in the presence of fluids that tend to evaporate, including propylene, butane and others. Because oil has low vapor pressure, leakage does not vaporize and disappear.
Users often request the oil leakage rate to be much lower than the typically acceptable leakage rate. As a result, traditional hydropads technology, while effective in many high-pressure applications, did not meet the criteria for the new ORC turbine conditions.
The seal manufacturer decided to move forward with recessed hydropads technology. This technology is specifically designed for the double pressurized O-ring pusher seal working with oil barrier fluids. The recess technology optimizes the liquid film thickness formation.
Fluid film thickness impacts every aspect of seal performance. Too low thickness causes contact between seal rings, resulting in high wear and absorbed power. On the other side, leakage is correlated to film thickness with a cubic factor. Traditional hydropad technology operates with a full, noncontacting working mode, but can have an unacceptable amount of oil leakage.
The recessed variant reduces the risk of uneven contact across the seal interface while providing better and stiffer lubrication, making the seal interface less sensitive to seal ring distortion. It takes the advantage of a noncontacting seal (low wear and generated heat) but with much less leakage. The ORC turbine manufacturer directly verified what was claimed above, performing a long-term qualification test that compared the old and the new design.
At constant intervals of 1,500 hours, the seals were dismantled and examined at a service center. At each inspection, the sealing rings were found in good condition without signs of wear or damage. The testing confirmed the capability of the recessed hydropads technology to prevent the risk of uneven contact, even with low film thickness. The absence of thermal damage (heat checking) was also the result of effective heat removal.
Results
In part due to the seal upgrade, the ORC turbine manufacturer can offer its turbine technology as a reliable income generator to the geothermal energy market. Seal leakage and overheating issues have been resolved.
In direct comparison with the previous design, leakage was reduced by 65% and power requirement decreased by 32% (average calculated at three different pressure values). Finally, the turbines consistently meet performance goals, including a five-year seal mean time between maintenance (MTBM) track record.