Q. How do you determine the primary cause(s) of mechanical seal failure? A. A systematic method, based on failure analysis, to investigate and correct the performance of mechanical seals provides the means to attain longer service lives and reduced life cycle costs. Failures occur when a product ceases to perform its intended purposes—either prematurely or after satisfactory life cycles have passed. Since downtime usually is even more expensive than maintenance costs, the efforts we expend on failure analysis frequently pay for themselves many times over when corrective actions are taken. To understand the primary causes of failure, we must first understand the basic features of a mechanical seal system. The function of every mechanical seal is to prevent the escape of a fluid past the clearance between a rotating shaft and the passageway through the wall of a housing or pressurized vessel. End face mechanical seals can incorporate many designs and configurations to accomplish this. As shown in the accompanying figure, typical mechanical seals have three basic components: (1) primary seal elements, (2) secondary seals; and (3) hardware for attaching, positioning, and maintaining face-to-face contact. The primary seal is formed by two materials with lapped faces that create a very restrictive leakage path from rubbing contact between them. In all such seals, one face is held stationary, and the other is fixed to and rotates with the shaft. The phrase “restrictive leakage path” is used because all mechanical seals leak – through these faces, even though one does not see leakage from most of them or any leakage is controlled to environmentally acceptable levels via ancillary systems. The leakage rates, however, are normally small; and environmentally acceptable, non-hazardous or nontoxic fluids may be allowed to evaporate or dissipate to the atmosphere in a short time period. For controlled, hazardous and toxic fluids, other means are required for containment.
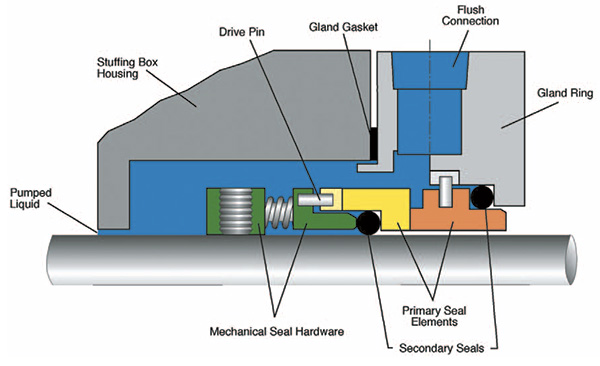
- Adapt seals to various pieces of equipment. This hardware may consist of a sleeve or housing for ease and precision of seal setting.
- Provide mechanical preloads to the seal faces until hydraulic pressures take over. This normally is accomplished by a large single-coil spring, or by a set of small coil springs.
- Transmit torque to both stationary and rotating faces. This normally is accomplished by a series of drive pins, dents, notches or screws integral with the seal design.
- Allowing the seal’s components to become chipped, scratched or damaged prior to or during assembly.
- Incorrect seal assembly, including the incorrect setting or misplacing of seal components in the seal cavity.
- Selecting the wrong materials of construction or an incorrect design for the combination of pressures, temperatures, speeds and fluid properties required for a given application.
- Improper startup and operating procedures, including failing to pressurize a double seal before starting a pump or inadvertently running a seal dry.
- Fluid contamination, which might be the presence of harmful solid particles in the seal cavity fluid.
- Poor equipment conditions, such as excessive shaft runout, deflection or vibration.
- Worn-out seals that may have completed a satisfactory life cycle.
- What the damage looks like.
- How the damage affects seal performance.
- What the types of damage indicate about a seal’s past history.
- What corrective steps can be taken to eliminate various types of damage from recurring under the same operating conditions.